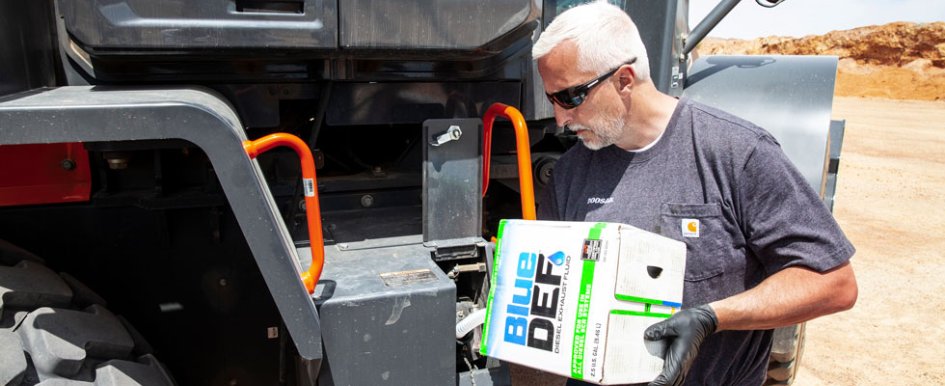
As supply chain issues continue to impact the inventory of construction equipment and the availability of machine parts in 2022, now it is more important than ever to have a parts strategy in place.
Contractors who have a parts stockpile or a way to access critical parts can minimize and often even prevent machine downtime. Here are some tips on how to ensure you have the parts you need on hand, exactly when you need them.
1. Most Commonly Needed Parts
It’s important to have easy access to some of the most frequently used parts to keep your machines running. For many machines, it’s the everyday filters and fluids that can require the most regular maintenance.
Additionally, you may need to replace teeth on buckets, cutting edges on dozer blades or pads on excavators. Other items that often need to be replaced due to routine damage are lights, mirrors, windows and hydraulic hoses.
It’s a good idea to keep these common parts on hand at your facility or with your crews in the field. Store items like filters and fluids inside a building or trailer at the jobsite.
It’s not a good idea to keep these items in the back of a pickup where they may be subject to adverse weather conditions. This is particularly true of diesel exhaust fluid (DEF), which can be sensitive to temperature variations that may impact the quality of the fluid.
2. Partner With Your Local Dealer
To ensure that the machine parts you commonly need are in stock, it’s vital to communicate your needs with your dealer. Alongside your dealer’s parts and service department, you can create and manage a parts supply plan for your fleet.
The more machines you have, the more regular maintenance is needed. Similar parts, such as fluids, can be used in multiple machines — communicating this ahead of time with your dealer can make maintenance easier for both parties.
If your dealer doesn’t have the items you need on hand, they can source them from a regional parts distribution facility.
Some questions to ask yourself as you plan your parts supply strategy include:
Is this a part I want to buy ahead of time and store myself? If so, where will I store it?
Do I have an in-house service technician that does all my maintenance? Or do I contract out with a dealer or a third party for equipment service?
Does my dealer’s maintenance plan cover parts and service support?
If a plan does cover parts and service support, will the dealer cover the repair costs?
3. Genuine vs. Nonbranded Parts
There are a few differences between genuine and nonbranded (generic) parts. A key difference between the two is that a genuine part is made for the machine and expected to be compatible. Additionally, the genuine part is included in a machine warranty, making it easier to get fixed or replaced if necessary. A generic part is not under the same warranty.
A part from an original equipment manufacturer (OEM) is quality tested, known to be a proper fit and works with other components within the machine’s systems. For example, a genuine oil filter meets the right flow and pressure specs for your machine. This oil filter won’t damage the engine or the air filtration housing. The same can’t be said for the generic part.
4. Telematics Monitoring
Telematics data can come in handy when planning ahead for parts. The use of service alerts from telematics systems allows you to track and stay on top of machine maintenance. If you know you need to order a 1,000-hour service kit, you can plan ahead on when to order it.
When there is a failure in a machine system, the telematics data can be very helpful in identifying the root cause of the failure. This can potentially go as far as communicating when a machine sensor is having issues. This can trigger actions in a couple of different areas. First, you or your technician can contact the dealer (or the dealer contacts you) to report an alert on the machine. From there, the dealer can dispatch a technician with the needed parts that will help solve the problem and get your machine running properly.
It can be difficult to keep up with machine parts. However, taking time to work with your local dealer and developing a parts plan can help avoid long wait times, extended machine downtime or lost revenue. If you’re ready to develop your parts plan, contact your local dealer today