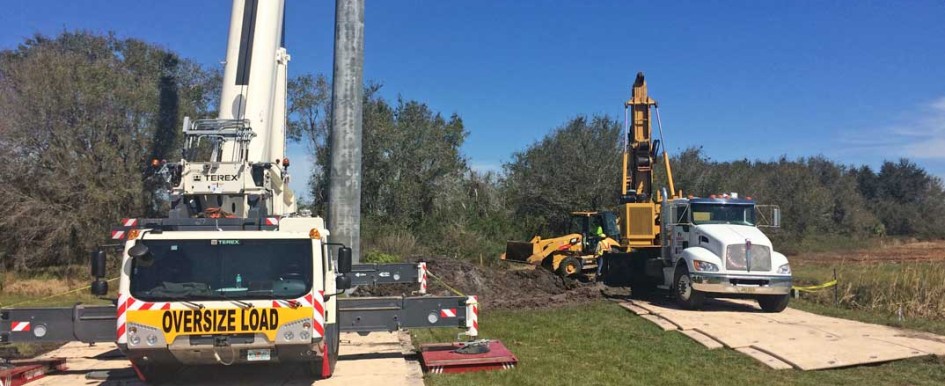
Over the past several years, market research has shown the increasing use of composite matting on a variety of projects and applications, including to create temporary roads and work pads in challenging environments. Research points to an uptick in demand due to the advances in composite matting technology and manufacturing that produces a cost-effective, reliable product. In addition, the use of composite matting has grown alongside our global culture’s heightened awareness and protections of employee safety and the environment. Today’s advanced, engineered composite matting systems help mitigate risks to equipment, personnel and the environment, while increasing the bottom line.
Composite Matting
Composite access mats are specifically designed to provide stable, fail-safe, temporary roads and working platforms for vehicles, equipment and personnel over any type of ground condition. They are typically made from HDPE (high-density polyethylene), which allows the mat to bend without breaking and to conform to ground contours, while providing tremendous strength and resiliency. Composite mats are 100-percent recyclable and are an ideal low-cost, environmentally-friendly ground protection solution. The mats maintain strength when wet, prevent vehicle slippage, increase worksite safety and provide companies with long-term cost savings, while simultaneously reducing the time and hassle associated with worksite preservation. Because composite mats are made of plastic, they have a weight-bearing load that is more than double that of wood.
But, much more than just better functionality, composite mats are designed to be safe. Mats are produced without nails or screws, eliminating the dangers of employees being punctured through their boots and flattening tires. Composite mats lock together to form one solid and continuous road or platform, therefore eliminating the possibility of individual boards coming loose and puncturing the underside of vehicles. Their surfaces are patterned for protection against slips and improved traction for both workers and equipment. The specially-formulated composite material is nonconductive to avoid problems with static electricity. While composite mats are lightweight and easy to transport and install, they are also durable (12 to 15 years) and require little maintenance.
Environmentally, composite mats are a much more responsible solution due to their nonabsorbent material, which allows for easy decontamination at the end of the project, meaning crews can prevent chemicals and other materials from entering the environment on the next project. Advancements in materials, design and manufacturing have led to the creation of a high-quality product that can be used in a myriad of applications, conditions and environments. Composite mats can be used to create anything from temporary roadways for remote utility repair to parking areas for a construction project.
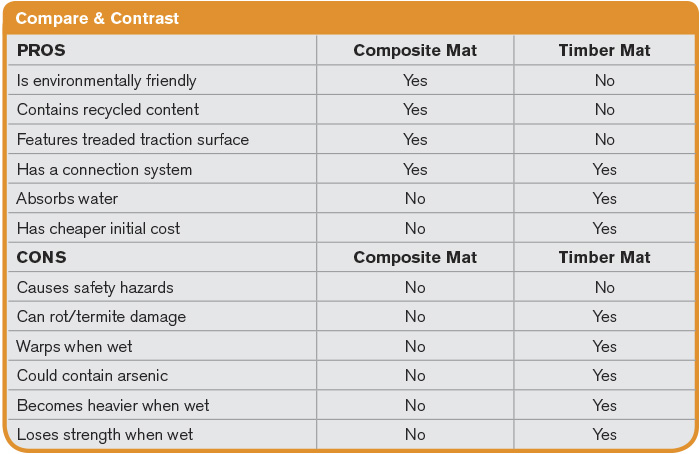
A Safer Jobsite
A jobsite is a dangerous place when it is not equipped with the right materials. Risk of liability and personnel, heavy-duty machinery, and the worksite can be costly. In addition to the immediate risks, a single accident can happen and companies are at risk of losing time and money in production and individual and class action lawsuits. Damage to a company’s reputation and brand are less quantifiable, but just as real.
In addition to creating a safe jobsite for crews and equipment, a safe environmental practice is good for the planet and good for business. Trees are a natural resource that can take up to 60 years to be regrown, so it’s important to be conscientious with the use of them. The cost of cross-contamination is a major concern to all companies. New rules and legislation are being implemented to protect sensitive areas against preventable contamination. Currently, in Western Canada, oil field work trucks are required to be washed top to bottom before they are permitted to go to another jobsite.
Wood Mat Hazards
Wooden mats have been in use for years as a cheap, readily available solution to create a temporary road or work area, especially in soft, unstable or sensitive ground conditions. But wood mats are fraught with hazards and problems. Initially, wooden mats are economical, but because of their short lifespan and high-maintenance requirements, they can prove to be costly in the end. The life of a wood mat is short (2 to 3 years), as they warp, rot, splinter and break down over time. Environmentally, since wood is highly absorbent, these mats will retain contaminants that can be transferred to other projects. The potential hazards of cross-contamination can be lethal to sensitive environments and have become an increasingly important consideration for engineers and project managers. Complete cleansing of wood matting is impossible. Often, these mats end up in landfills or are burned. These nonsustainable disposal practices can have a deleterious effect on the environment.
The Market Shift
Composite mats have been used in the oil and gas industry as drill pads since the 1990s. It is only in the last 10 years that composite matting has been used as an alternative to wood mats in other industries. Composite mats offered critical advantages over wood, including easy access to remote locations and sensitive environments, regardless of climate and weather conditions. Composite mats are a good solution for any project because they offer protection for the ground from chemical spills and other toxic liquids. These mats are excellent when working in ecologically sensitive areas, such as wetlands, or when working on coastal sand, marshy and muddy surfaces and other unstable ground conditions. Composite mats eliminate common problems found with timber mats, such as rot, insect infestation, warping and board breakage. As of 2016, 12 percent of the matting market is comprised of composite matting products, and that number is steadily growing. Over 20 different industries rely on composite matting for temporary roads or working platforms, including construction, utilities, pipeline and alternative energy.
Significant Savings
Composite matting is generally more expensive upfront, but it is more cost-efficient due to its durability and stability. Since composites weigh less than wood mats, more composites can be loaded onto a truck—resulting in a larger working surface area per truckload, reduced number of transport trips per project, reduced fuel consumption, reduced greenhouse gas emissions per project and reduced transport costs per project. Reducing truckloads not only saves your company money, but it is also good for the environment.