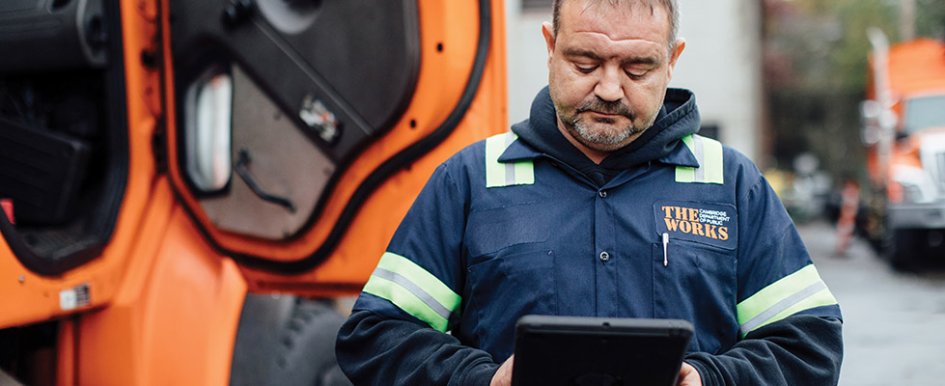
Accountability is the linchpin that holds together a well-oiled operation, especially when that operation consists of many moving pieces of equipment. The inability to know who did what, when, where and why makes it difficult to follow up and address issues such as lost, displaced and/or damaged equipment or poor maintenance management. Contractors, construction fleet owners and managers can establish robust accountability systems by leveraging technology such as telematics, equipment management systems and fleet management software (FMS). These systems benefit not only the fleet but also the operators themselves.
Real-Time Equipment Tracking & Status Updates
Relying on manual equipment tracking methods such as whiteboards, paper forms, spreadsheets or verbal assignments can lead to confusion within your crew — and sometimes even other departments. When equipment goes missing or breaks down, accountability is elusive. This lack of insight can cause communication issues and costly downtime, negatively impacting productivity and profitability.
To avoid the pitfalls of manual tracking, fleets are turning to technology-driven equipment tracking systems that offer real-time asset visibility that’s accessible. Implementing an equipment tracking system might sound daunting, but user-friendly software simplifies the process. Equipment tracking solutions allow you to monitor equipment location and manage assignments from anywhere, enhancing team collaboration and ensuring seamless communication regarding equipment health, location and status.
Tracking equipment in real time helps maintain accountability, and using a fleet solution with a mobile-first equipment tracking system provides fleets with constant asset visibility. Fleet managers can instantly update and view the status of each piece of equipment, ensuring smooth operations.
Leverage Barcodes & NFC Tags
While tracking equipment status, such as active, in-use or out-of-service, keeps you informed about equipment usage, you can go a step further and implement equipment check-in/out parameters using FMS. This allows employees to assign themselves a piece of equipment, not only giving more accurate data around usage per job and usage overall, but also improving accountability.
FMS uses barcodes and near-field communication (NFC) tags to help fleets streamline equipment management. Equipment details, check-ins/outs and assignments are just a barcode scan away. This minimizes cumbersome paperwork, allowing more time for productive tasks, and it also provides better insights so fleets can quickly spot and source the cause of issues.
NFC technology takes the barcode efficiency to the next level. By encoding NFC tags on equipment, you receive push notifications on your smartphone when you’re within a few inches of a specific piece of equipment. With a simple tap, you can make quick edits, check equipment in or out, or assign equipment to others.
Of course, a crucial aspect of accountability is knowing the last location and usage of equipment. FMS provides a “last known location” feature to help fleets cut down on time wasted trying to track down an elusive piece of equipment. Whenever a barcode is scanned using the FMS’s native mobile app, the system automatically records the equipment’s location. This significantly reduces equipment loss and theft by providing a trail of who last used it and where it was last located. The result? Countless hours and dollars saved on equipment searches and repurchases.
Assign Equipment for Accountability
One advantage of FMS and other equipment tracking solutions is the user permissions feature. You may not want just anyone to be able to check equipment in or out, whether for liability reasons or because it just makes the most sense for how your operation is run. By adjusting user permissions, you can restrict individual equipment check-in/out. Instead, you’ll have equipment assigned to individuals by a designated person, allowing you to collect the same data without having too many hands in the pie.
Equipment assignments ensure that everyone is on the same page and accountable for their assigned equipment. Managers can create and manage equipment assignments within the software which employees can access via the mobile app. As with the equipment check-in/out feature, assignments create a robust audit trail for all equipment.
Get Ahead of Repairs
Service costs take up a large chunk of a fleet’s budget, and if you’re not properly inspecting and performing preventive maintenance on heavy equipment, those costs can rack up. Equipment inspections are every bit as important as vehicle inspections when it comes to catching issues before they snowball. Whether your field crew, technicians or foremen are responsible for daily, pre- or post-trip inspections, it’s critical that the responsible party be held accountable for filling out and submitting inspections so issues can be followed up on quickly. Using digital inspections in FMS promotes accountability (and reduces instances of pencil-whipping) while ensuring real-time notification of failed inspection items.
When it comes to maintaining equipment, accountability is also critical to ensure the right communications are going to the right individuals. For example, if preventive maintenance is scheduled for a piece of equipment, who needs to know: the assigned user, the foreman, the technician to whom work will be assigned, a third-party shop? Who’s accountable for getting the equipment to the shop? Understanding who is directly accountable for each action improves communication and streamlines the service workflow.
Benefits for Operators
A key misconception around fleet asset tracking systems is that they’re put in place to micromanage employees. Holding equipment operators accountable isn’t about scrutinizing their actions, however: it’s also about empowering them. Benefits to operators include:
- Clear responsibilities — Operators have clear knowledge of their assigned equipment, fostering a sense of ownership and responsibility.
- Enhanced communication — Operators can easily report equipment issues in real time, enabling quicker problem-solving.
- Streamlined workflow — With accountability systems in place, operators spend less time on paperwork and more time on productive tasks.
- Morale boost — Feeling accountable for their equipment can boost operator morale and job satisfaction.
Empower Accountability for All
Fleet managers and contractors recognize that accountability is the cornerstone of a successful operation. Implementing technology-driven equipment tracking systems not only improves asset accountability but also empowers equipment operators. With real-time tracking, streamlined workflows and clear responsibilities, these systems contribute to increased productivity, reduced downtime and enhanced equipment health. It’s a win-win for both the fleet and its operators.
Image courtesy of Fleetio