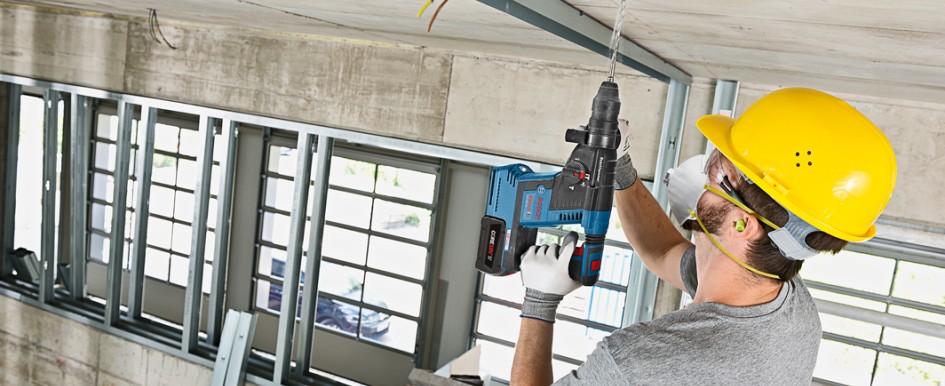
When a general contractor heads out to pick up a new 18-volt impact driver for the jobsite, what exactly is that construction pro purchasing? The answer might be a surprise, because it’s not actually a power tool—it’s a battery system. Unless a professional user is already dedicated to a battery platform, the purchase of those first couple tools may dictate the power choice down the line. So, it makes sense to choose the battery system first.
Backward and forward compatibility (fits 2007 drills/drivers and tools moving forward), increased power and runtime and diversity of tool applications from a single battery platform are the keys to a power tool purchase. This is a case where application knowledge and simplicity should intersect to make the best choice for the long term.
Down to Business
For example, with the introduction of its CORE18V battery, Bosch employed 10 Panasonic 20700 cells that offer more power and runtime than traditional 18650 cells. The 20700 cell is 2mm wider and 5mm taller. That 33-percent increase in cell size allows for a larger chemical reaction and delivers the optimization required to accommodate higher current draw.
There’s an advantage to having cells that are welded and rail-connected for maximum energy transfer, allowing advanced heavy-duty lithium-ion batteries to provide better performance than conventional batteries that can be up to 35-percent larger. Rails connect the positive and negative terminals of each cell best when highly conductive copper is used versus less conductive, deterioration-prone copper-plated steel. The issue here is that, after extended use, the galvanized coating will begin to wear off, subjecting the steel beneath to rust. Oxygen also can react with a galvanized coating and cause corrosion issues, but copper doesn’t corrode or rust over time.
In addition, use of flexible printed circuit boards (FPCB) to replace multiple rigid boards and connectors can deliver a battery that is more compact and weighs less. Power output of up to 1,440 watts from a conventional-size battery compared to the 800-watt maximum seen in most standard 6 amp-hour (Ah) packs doesn’t hurt either.
Users should look for an optimized battery package that is built to drive the high-demand tools that are on the horizon but function on the same battery platform. An improved power connector within the high-density cells ensures lower internal resistance, which means higher currents can be drawn from the cells over a longer time period. A battery that delivers more runtime versus previous-generation batteries offers more current to finish jobs.
The big focus for power tool manufacturers is building end-to-end product systems that offer superior performance regardless of the job. That not only means increased power and runtime, but also backward compatibility across the full power tool lineup—a step beyond battery power platforms that offer one system for heavy-duty, high-power tools and another for standard-duty tools. The goal is to offer a complete 18-volt battery system that can power a standard drill/driver one day and an optimized, heavy-duty tool like a rotary hammer the next.
Keep it Cool
An advanced housing design that keeps the battery cooler is better for runtime and overall battery life. Heat means a shorter product life span and also speaks to expense: Battery replacement is essentially a maintenance cost, so the longer the battery life, the lower the expense. In most cases, the tool will outlive the battery.
The battery housing should manage heat efficiently, which could include separating each cell into its own compartment. This allows heat from the cell to dissipate. Thanks to maximum heat dissipation and onboard electronics that reduce inner cell resistance, the battery should remain below thermal shutdown thresholds even when under high power demand.
An advanced heavy-duty battery may have internal circuitry that monitors the cells in the battery, but circuits can do more than that. These internal circuits can essentially manage temperature, taking action to protect the battery and the tool if cells approach 158 degrees Fahrenheit (70 degrees Celsius), which is thermal shutdown. If any cell surpasses that mark, the circuits can disable the battery until all cells are below the threshold.
With all of this capability, what does that do to charge time, a key productivity factor on any jobsite? Actually, the charge time will decrease. With all lithium-ion batteries, the temperature of the battery must be below the thermal shutdown temperature in order to begin charging. Because heavy-duty batteries with inadequate heat management could reach thermal shutdown, the battery cannot be completely discharged due to thermal shutdown prior to complete discharge. Under normal conditions, charging can begin as soon as the battery is placed on the charger, so charge time is decreased because advanced lithium-ion batteries that manage heat well don’t require cooling prior to charging. Other best-in-class battery attributes include protection to prevent overdischarging and overloading.
What about Runtime?
The Ah metric is about runtime, so a 9 Ah battery will have a longer runtime than a 6.3 Ah battery. The trade-off is that a higher Ah battery will be larger, heavier and more cumbersome to accommodate greater energy capacity. Standard 18-volt tools powered by advanced, heavy-duty batteries see an increase in runtime.
The future of battery power in the power tool industry is about shrinking the delivery mechanism, delivering power and runtime and ensuring existing tools don’t get lost in the battery shuffle. It’s important to consider the entire battery platform when choosing the power tools you will need in the future, whatever the job. It’s the battery that makes the power tool, not the other way around.