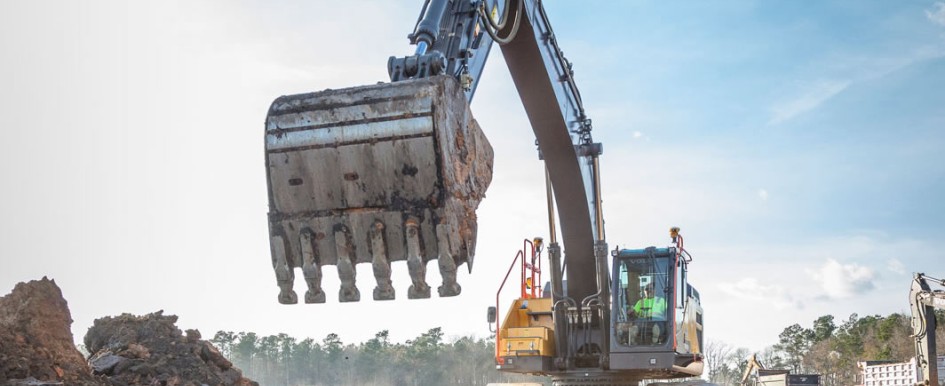
On some construction jobsites today, machine-control systems are just as prevalent as smartphones, excavators or even hardhats, while on other jobsites, you may only see stringlines and grade stakes. Often, construction business owners who are hesitant to adopt machine-control systems are intimidated by the technology, or they just don’t know where to start. However, if this describes you, your business could be missing out on a significant opportunity to improve grading accuracy and optimize productivity. Today’s machine-control systems help operators of all skill levels get to finished grade faster by relaying real-time grade information directly to the operator’s dashboard. By putting the design of the job in the cab and at the operator’s fingertips, operators can guide the bucket or attachment to finish grade much more quickly. Before you pound one more stake, consider the benefits of machine control, as well as the cost of over- or under-excavation, project overruns or missing out on opportunities to branch out and win new work. Let’s dive into the top five reasons you should be using grade control for your business.
1. Increased Efficiency
The scary truth about most construction projects is that 80 percent run into overtime. While not all of that overtime can be attributed to grading, it’s safe to assume that some of it can be. Keep in mind that grade control speeds up many of these processes by relaying real-time grade information directly to the operator. In addition, some new systems now offer a sophisticated “automatics mode.” With excavator autos, the system automatically controls the boom and bucket according to the digital design. It essentially locks onto the grade and automatically makes adjustments. From there, the operator controls the stick, and the system prevents the machine from undercutting or overcutting. These automatic options are helping operators of all experience levels achieve grade consistently, with high accuracy and in much less time. New grade-control systems also speed the transfer of files from the office to field, which gives everyone the latest design quickly and easily. Many users report being able to get to grade 30-percent faster using grade control. When evaluating the cost of grade-control systems, divide the investment by your labor rate to determine how many hours of use it will take to pay for the system. Most users can expect a full return on investment (ROI) for grade control systems at around 200 hours of use.
2. Greater Accuracy
While getting to grade quickly is important, it doesn’t mean much without accuracy. Grade-control systems use a combination of GNSS, inertial and laser or total station technology to accurately position the excavator’s bucket or dozer blade in real time. Using an in-cab display, the operator then sees the 2-D or 3-D design surface, grade or alignment inside the cab. These systems determine the position of each tip of the blade and compare it to the design elevation in the cab to compute cut/fill to grade. As discussed earlier, automatics-mode features are also available for excavators, which allow for accurate excavation in a very short time.
3. Improved Safety
Today, the best construction companies have made a serious commitment to jobsite safety. The most effective safety programs emphasize continuous improvement and ongoing training to ensure that injuries and incidents are minimized. Improving safety on the jobsite is just one more reason to consider grade control. Grade-control systems greatly reduce the number of moving pieces around the jobsite. In many cases, these systems reduce the need for staking and grade checkers, who can sometimes be put in precarious positions, such as the bottom of a trench, while checking grade. They also reduce the need for supervisors and surveyors to be constantly on-site.
Extended Wi-Fi capabilities and greater connectivity options available with grade-control packages also allow teams to remotely transfer grade control data, 3-D models, remote GNSS corrections and telematics from the jobsite to and from the office. Grade control, coupled with connectivity options, also offers the potential to save many hours each month that were once spent driving to each machine and stopping the excavators and dozers to share new design revisions.
4. Increased Revenue
One of the greatest things about machine control is that in many cases, it helps level the playing field for small and midsize contractors. By automating much of the excavator or dozer operation, operators can achieve grade and move on to the next job more quickly. And the enhanced accuracy of various positioning systems allows precise control of grades and contours in several applications like mining, earthmoving and paving. Reducing material overages when using machine control can save significant revenue.
A typical contractor will budget for 10-percent material yield on concrete, asphalt or engineered fill. For contractors using machine control, this is typically in the 1 to 2 percent range. To give you an idea of the saving on a 50,000-square-foot, 4-inch slab on grade with 6 inches of engineered fill, the contractor would save 49 cubic yards of concrete and 74 cubic yards of engineered material. Grade control also allows contractors to branch out into new areas of work or to take on bigger jobs. That might include taking on more finish grading jobs, landscaping work, site layout or utility layout, for example.
Easy-to-use 3-D modeling and automated grade-control systems specifically designed for smaller projects and smaller machines can mean a significant new revenue stream for small and midsize contractors. These systems are cost effective and can be put on equipment. In addition, because operators can reach finish grade more quickly, often with the same machine, instead of bringing in finished grade equipment, there is less travel time and coordination of machines across multiple jobsites. This translates to significant savings for contractors in terms of fuel costs, wear and tear on machines and maintenance.
5. Decreased Staffing Challenges
It’s no secret that there is a growing shortage of skilled and experienced heavy equipment operators. As many experienced operators near retirement, contractors are beginning to realize the potential of grade control solutions to help fill this skills gap. New grade control systems are much more intuitive and easy to use, which make them more attractive to new operators. This allows operators of all skill levels to be much more accurate at the first pass and create smooth, flat or sloped surfaces more easily. They can also achieve finished grade to millimeter accuracy with fewer passes. This frees up more experienced operators for complex jobs and lets newer operators hone their skills. Today, many grade-control applications are also built on familiar operating systems, which make them easy to use with a similar look and feel to smartphones, tablets and other devices we use every day. They also have a more intuitive interface and touch-screen displays, which have been optimized for productivity. New systems are also more configurable, so each operator can personalize the interface to match his/her workflow.
Whatever your personal comfort level has been with grade control in the past, it may be a good time to reevaluate the way you think about these systems. Construction business owners willing to make the leap can experience significant efficiency gains in terms of minimal rework, cost savings and more competitive bidding.