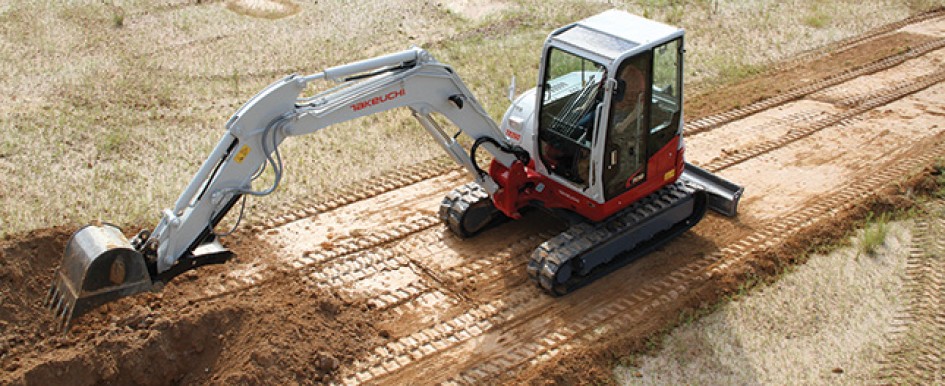
Diesel engines have come a long way in the last 120 years, and the technology will continue to evolve. Using heat of compression to ignite fuel in the combustion chamber—as opposed to spark-ignition gasoline engines—diesel engines offer the highest thermal efficiency of any internal or external combustion engine and can be up to 30 percent more efficient than gas engines. With their low cost and high efficiency, diesel engines have become standard for nearly all off-road construction equipment. The only real disadvantage to diesel engine technology has been that its emissions contain high levels of particulate matter (PM) as well as nitric oxide and nitrogen dioxide (both commonly referred to as NOx), which is primarily due to the makeup of the fuel itself and the process by which the engines are designed to burn it.
Amidst growing environmental health concerns, the Environmental Protection Agency (EPA) signed the final rule introducing Tier 4 emissions standards in 2004. These new standards, which are in the process of being phased in between 2008 and 2015, require that both PM and NOx be reduced by 50 to 96 percent compared to the existing generation of diesel engines.
Looking at the newest equipment from manufacturers, it is clear that Tier 4 compliance has been one of the top drivers of innovation that our industry has seen in a long time. As Tier 4-compliant engines are incorporated into more equipment lines, manufacturers are looking at completely new ways to boost fuel efficiency and power.
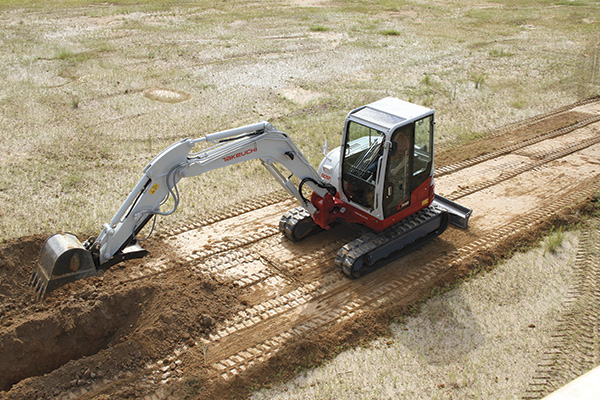
Fuel Requirements
The next generation of Tier 4-compliant diesel engines requires the use of ultra-low sulfur diesel fuel (ULSD). This type of fuel has been used since around 2006 but primarily in trucks and other on-highway vehicles. Older off-road machines and engines can continue to use the higher sulfur fuels, but because they are being phased out, the fuels are becoming more difficult to source.
The Big Differences
While every manufacturer is pursuing its own emissions compliance strategy, several technologies have been introduced during the last few years that are becoming the new standard. As far as noticeable changes to the looks of the machines, the most noticeable is usually the placement and size of the air intake system and after-treatment system to accommodate the need for increased airflow and cooling. New changes to engines will likely mean that engine compartments may need to be redesigned to house the new systems, so slightly enlarged engine compartments will be commonplace during the next few years until the technology advances further.
Exhaust Gas Recirculation (EGR)
Some Tier 4 engines use a process known as cooled exhaust gas recirculation (EGR), a technique that recirculates a portion of exhaust emissions back into the combustion chamber. This lowers the combustion temperature and further limits the formation of NOx. This is the technology that many manufacturers are incorporating into their product lines, along with Diesel Particulate Filter/Diesel Particulate Diffuser (DPF/DPD) exhaust after-treatment systems.
Regeneration
Another after-treatment process that manufacturers are incorporating into the new generation of diesel engines is regeneration. This is the process of removing accumulated soot from the air filter either passively (by using the engine’s exhaust heat or by adding a catalyst to the filter) or actively by introducing very high heat into the exhaust system to burn off accumulated particulate matter.
Evolving Maintenance Practices
The need to reduce emissions will continue to introduce changes in engine and equipment design, such as the integration of particulate filters, oxidation catalysts and other NOx after-treatment systems.
In addition to possessing a general knowledge of exhaust equipment maintenance and operation, today’s technicians need to have a general familiarity with electronically controlled engines, exhaust after-treatment control devices and other new Tier 4 technologies.
Most Tier 4 machines will use particulate filter technology that can require periodic maintenance, cleaning and replacement. The bottom line is that service technicians must keep up with the technology, and leading manufacturers should provide resources to help them do so.
Driving Product Innovation
These new emissions requirements have changed the game for most manufacturers. In fact, they have changed the way we approach the technology altogether. Many manufacturers have spent the last several years working to incorporate the new standards into their existing equipment lines, and as they have done so, engineers have developed many new technological innovations that boost fuel economy and power in ways that we never could have never imagined.
Tier 4 compliance will undoubtedly be one of the biggest forces driving innovation in construction equipment technology for the next several years, so be on the lookout for even more advanced fuel consumption and after-treatment technologies.