All contractors should know their equipment needs to meet Tier 4 Interim and Tier 4 Final emissions regulations. However, many question how emissions solutions adopted by construction equipment manufacturers will impact their operations. The answer requires a basic understanding of technologies OEMs use to manufacture Tier 4-certified machines.
Two Primary Technologies
Manufacturers have narrowed the technology options down to two choices for most classes of heavy equipment. One is selective catalytic reduction (SCR). The second is cooled exhaust gas recirculation (CEGR). Both reduce particulate matter and NOX emissions in keeping with the Environmental Protection Agency’s mandates. NOX is produced when the engine is at its hottest. Particulate matter is created when not all fuel is burned during combustion, usually when the engine is cooler.
SCR reduces particulate matter formation in the combustion chamber and treats exhaust gases with diesel exhaust fluid to eliminate pollutants. SCR technology has been well accepted for several years for on-highway diesel applications throughout North America and Europe.
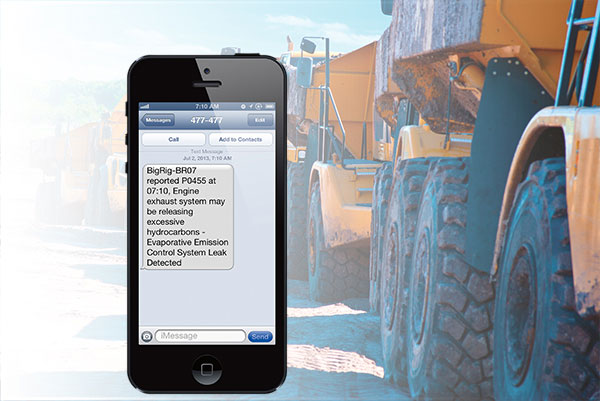
Engines that use SCR systems are highly efficient. The higher combustion temperatures reduce particulate matter levels but increase NOX levels. To address high NOX levels, the aftertreatment-only system creates a chemical reaction by adding diesel exhaust fluid. This transforms the NOX into nitrogen and water, which occur naturally in the atmosphere. The aftertreatment system includes a diesel exhaust fluid supply module and tank, a dosing module and an SCR catalyst. No particulate filter is required, as high combustion temperatures lead to low particulate matter levels. SCR improves performance because it allows the engine to breathe more freely. In many applications, it delivers enough improvement in fuel economy to offset upfront cost increases within the first year of operation.
With a CEGR system, exhaust gases are cooled, blended with fresh air and returned to the engine. The process lowers combustion temperatures and reduces NOX. The cooler combustion temperature results in a higher particulate matter level, which is then reduced by an aftertreatment diesel particulate filter. The system’s components include an exhaust gas recirculation valve, the exhaust gas recirculation cooler, the diesel oxidation catalyst and the diesel particulate filter. In some cases, a regeneration burner is also needed. The diesel particulate filter requires periodic regeneration (re-gen) for optimal operation. This re-gen process is usually automatic and does not require operator intervention, although manual re-gen is required in some applications.
The practicality of SCR and CEGR technology varies. SCR technology on most skid steer models would have a greater impact on the cost of the machines because their purchase price is lower. Also, traditional skid steers run at steady engine speeds and loads, creating consistent heat to decrease particulate matter. Therefore, CEGR is the better technology for this application.
Additionally, a diesel oxidation catalyst-only solution is a match for skid steers that have multiple operators and travel among jobsites regularly. Using the maintenance-free diesel oxidation catalyst-only solution for these models creates greater convenience and more efficient operation compared to CEGR with diesel particulate filters or even SCR to meet emissions within this horsepower range.
Wheel loaders are a different story. SCR is used on these machines because their application does not create the steady engine operation conditions like those experienced with skid steers. Wheel loaders’ tasks are more variable, creating inconsistent engine loads and power demands. SCR enables the wheel loader’s engine to run at peak performance while regulating emissions.
Simple Maintenance
Maintenance for both SCR and CEGR systems has turned out to be easier than contractors anticipated. The SCR system simply requires regular filling of the diesel exhaust fluid tank. This can be performed as part of regular maintenance when checking fluid levels or refueling. Filters in the diesel exhaust fluid circuit are usually easy to access and have the same maintenance schedule that engine oil has. SCR-equipped machines will continue using standard oils and do not require special fuel.
CEGR maintenance revolves around the diesel particulate filter, which includes regeneration, along with changes in oil and fuel requirements. The filter is designed to last for thousands of hours and is easily accessible. CEGR machines typically go through passive and manual regeneration cycles to heat the diesel particulate filter to burn off accumulated particulates. On many machines, passive re-gen occurs periodically during normal operation. Manual regeneration, which may be required daily depending on the nature of operation, takes 10 to 20 minutes and requires the operator to ensure the machine is clear of combustibles before starting.
Some CEGR systems require the use of higher-spec, more expensive oil to deal with the effects of higher soot levels that result from lower combustion temperatures. Most manufacturers recommend using oil that meets the API CJ-4 oil specification. CJ-4 oil is designed to protect emission control systems, help comply with emission standards, reduce engine wear and control piston deposits and oil consumption. Also, CEGR engines with diesel particulate filters should use ultra-low-sulfur diesel fuel (15 ppm maximum sulfur) because even small amounts of sulfur can impair the filters’ effectiveness. Although some CEGR-equipped machines will require more frequent oil changes, most manufacturers are increasing engine-oil capacities to lengthen oil-change intervals.
Beyond Maintenance
Operators need training to understand new dashboard warnings and indicator systems. Also, operators of CEGR machines requiring manual regeneration need to ensure the machine is clear of combustibles each day before use. Fleet managers and business owners should use telematics systems to keep track of machine hours and maintenance intervals, as well as unusual changes in temperatures, pressures or other unusual operating characteristics.
To understand and adapt to Tier 4 changes, contractors can rely on dealer networks that have teams with expertise in Tier 4 technologies and are well versed in proprietary technologies of the manufacturers they represent. Dealers and manufacturers have long prepared for Tier 4 regulations. As a result, Tier 4-certified machines should be easy to incorporate into your business.