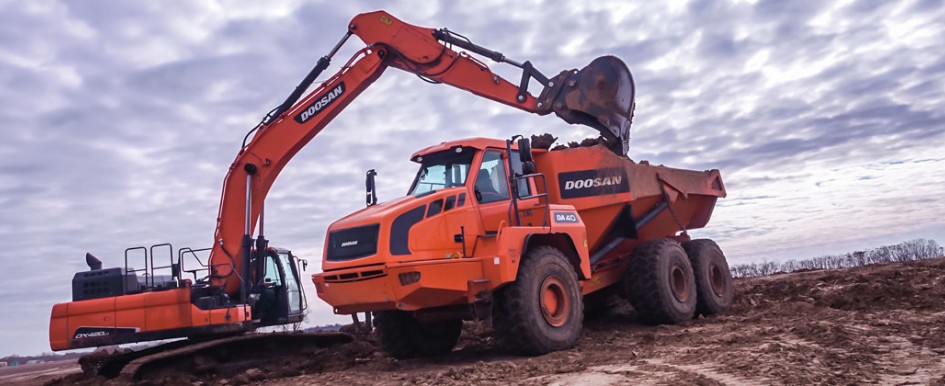
When it comes to off-highway hauling, there are two types of trucks available to help move material from one location to another—articulated dump trucks (ADTs) and rigid frame trucks. Although they both have massive hauling capabilities, an ADT’s design offers several off-road performance advantages in comparison with rigid frame trucks, especially in earthmoving and hauling applications.
Since an ADT’s simple, yet effective, design can be very different from other pieces of hauling equipment, it’s important that the truck is compatible with the specific tasks it’s needed to perform. Keep in mind that if the tasks you will be completing are routine and regular, it may be best to purchase an ADT. However, if the tasks are performed only periodically, you may decide to rent one as needed. ADTs can be a versatile solution for off-highway hauling, helping you increase machine profitability and jobsite productivity. Before renting an ADT, take a look at the following tips.
1. Jobsite Conditions
ADTs are commonly found on jobsites in the early phases of site development, typically when ground conditions are not ideal. Unlike rigid frame trucks, ADTs are designed to quickly move large amounts of material (e.g., dirt, rock, sand and gravel) in soft, wet or adverse ground conditions.
Because they are designed to operate in conditions that limit rigid frame trucks, ADTs can increase productivity and uptime. For example, they have an articulation joint, which distributes weight equally during maximum turning. In addition, they are equipped with a semi-independent front suspension, which enables free movement of one side, keeping the front wheels in contact with the ground for better traction and shock absorption.
Some ADTs have front- and rear-limited slip differentials, as well as an inter-axle differential, to improve truck performance by splitting power—one-third to the front and two-thirds to the rear. A front-mounted turning ring and rear tandem bogie are two ADT features—a design feature for some brands—that maintain maximum traction and stability when traveling over unusually rough or soft terrain.
The right tires contribute significantly to an ADT’s tractive force, which is determined by the tread design, remaining tread life and tire inflation. Jobsite ground conditions are also a factor. The most common tires for ADTs are radial E3 or E4 tires; however, E3 tires offer better traction for sites that have soft soil conditions. Individual tire manufacturers can inform you and your operators about which rubber compounds will provide longer machine life for earthmoving and hauling applications.
2. Productivity Level & Machine Size
As an equipment owner, your primary goal is to maximize productivity by reducing haul cycles. An ADT should have a good power-to-weight ratio along with an abundance of horsepower and torque to help your operators haul more and travel faster during a single cycle.
One of the best ways to maximize productivity when reducing haul cycles is to match your ADT with the proper loading equipment, such as an excavator or wheel loader, so your equipment operators do not have to wait long between loads. For example, if your jobsite calls for short hauls and you own a mid-size crawler excavator, consider renting a 30-ton ADT. If you need to move larger volumes over long distances, a larger excavator paired with a 40-ton ADT could likely fit your requirements. If you do not have the corresponding loading equipment, your dealership may have the right size wheel loader or excavator in their rental fleet. It typically takes four to six passes to fill an ADT for most material hauling tasks on sites with good production.
3. Serviceability
Before renting an ADT, make sure to ask about serviceability, especially ease of access to the transmission and engine compartment on all sides. Like any piece of construction equipment, proper, scheduled maintenance will extend the life of the machine and save you money over time. In addition to completing a daily walk-around, perform the following three preventive maintenance procedures:
- If an auto-lubrication system is installed, inspect it to ensure that there is no premature component failure due to lack of grease.
- Assess tire air pressure, wear and damage to mitigate major repair risk.
- Monitor engine temperature and revolutions per minute (rpm) history with telematics to prevent engine damage and premature repairs.
Educated and dependable product support is critical for construction equipment. Make sure to choose a dealer that offers product specialization, trained mechanics and timely response times, and keeps premium parts in stock.
4. Options & Accessories
An ADT can be equipped with multiple options and accessories to help increase its potential. Tailgates, for example, help to minimize spillage from the truck’s dump body and improve productivity. In addition, a heated body kit is also important, especially in colder climates, because it helps divert the engine exhaust through channels in the dump body, keeping materials from freezing. Cold-weather starting kits and heated rear mirrors are other useful options for ADT operators working in the northern United States and Canada.
5. Safety Features
Understanding the machine’s safety features is another important consideration before selecting an ADT. Proper location of the turning ring, or oscillating joint, allows for equal weight distribution between the front tires when the machine is loaded and turning. Unequal weight distribution can lead to instability.
In addition, some ADT manufacturers have addressed compromised sight lines with rear sloping frames, lowering the center of gravity for more equal weight distribution and improved stability when fully loaded. The frames improve tractive effort, minimize tire wear and lower ground-bearing pressure as well.
Large, well-placed and properly adjusted rearview mirrors give a continuous view of the rear wheels while the operator is backing up, providing a higher degree of safety on the jobsite. In addition, some ADTs are equipped with a rear camera.
6. Fleet-Tracking Technologies
Today’s ADTs can be equipped with on-board fleet tracking technologies, such as telematics, to track and report data in real time. Telematics systems provide you with a better understanding of how, when and where your construction equipment is being used. The location is provided in longitude and latitude, and the mapping software automatically changes to the closest address.
In addition to tracking the physical machine location, many equipment manufacturers offer a geofence, or time fence feature, to help owners and fleet managers monitor unscheduled use and track machines in the event of theft or vandalism. With a geofence, you can set virtual GPS boundaries, and if a machine moves outside of the boundary, you are notified via email or text message.
Many fleet tracking technologies use a terminal that is installed on the machine to gather and communicate data wirelessly via cellular or satellite service. The machine’s data is then sent to a website, where you, your operators and your equipment dealer can monitor the machine’s performance, operating hours, fuel usage, engine idle time and work time. You can also monitor engine and hydraulic oil temperature, as well as fault and warning codes via computer or cellular device.
By taking the time to ask the necessary questions, you can better select the appropriate ADT and available features that best meet your jobsite needs and conditions.