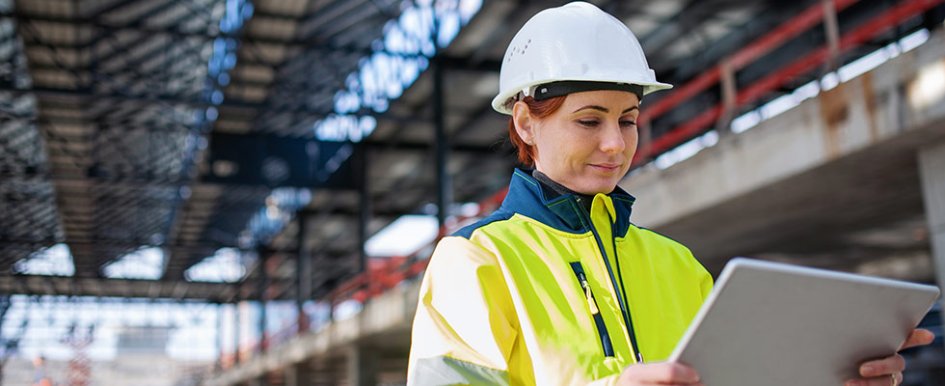
It’s not uncommon for a construction project to fall behind due to supply issues, staffing, last-minute client requests or weather. When this happens, the project manager makes adjustments to the plan and resets client expectations. What they may not realize is just how much each change nips at the bottom line. While a certain percentage of every bid factors in delays, there’s an often-overlooked data set that could minimize the impact of changes: field data.
Field data contains a lot of critical information about the skills of workers and status of projects, yet it’s not always factored into the larger project plan. When you bridge the gap between what’s happening on the jobsite and the best-laid plans mapped out in the construction business owner’s office, you can spot trends and get ahead of potential issues before they erode a project’s profitability.
Why Jobsite Data Is Overlooked
Jobsites are where the construction business owner makes — or loses — money. But the processes that many contractors use to manage projects and people make it nearly impossible to see where a project is going awry until something happens. This is because the majority of business processes on construction jobsites are still done with paper and pen.
Think about it: Workers sign in each day by scribbling their name and time of arrival on a sheet of paper. The daily log is largely based on memory and is subject to human error, especially after a long day when the supervisor is eager to get home.
In addition to the aforementioned challenges, many important conversations and activities are not documented. For example, workers may talk about completing their latest training certifications or their specific experience in the trades, but that information may not be recorded. Knowing who is on a jobsite and what they bring to it helps project managers be more effective in planning the work. It also protects the business owner if there’s an incident or investigation. For these reasons, digital tools are springing up on construction jobsites. It’s all part of the construction industry’s larger shift to digital transformation.
Digital transformation is the use of technology to modernize processes. Yet it’s more than just the use of technology on a construction jobsite: Digital transformation is also about the company’s culture and transforming the way the business is managed to ensure that digital technology is seamlessly woven into every process. Moving to digital transformation is on the radar for most construction companies.
A recent survey conducted by the National Association of Women in Construction (NAWIC) and Safe Site Check In showed that 71% of companies consider digital transformation a priority. However, data from Dodge Construction Network indicates that only 15% have implemented a digital transformation strategy.
According to Jon Broyles, corporate safety officer at AMG & Associates Inc., “Once our digital tools were in place, it made our work environments safer, allowing individuals to sign in, answer safety questions and verify manpower. We use these technologies to always know who is on site, their location, project they’re working on and supervisor. We can easily reach them and have private, digital records that are useful for other departments, including safety (meeting Occupational Safety and Health Administration standards), payroll, project management and even the CEO.”
Using Jobsite Data to Make Business Decisions
The shift to digital transformation is iterative — it’s not like constructing, building and moving on to the next project — and doesn’t need to be overwhelming. Most construction companies start small, using an app on a smartphone or tablet to automate, streamline and better document what’s happening on a jobsite. The familiarity of apps in our everyday lives makes it easier for workers to adopt a new tech process on the jobsite. Daily check-in apps are the easiest point of entry to digital transformation.
To get even more value from jobsite data, contractors are integrating it into project management platforms like Procore and CMiC. The field data, with its insights on worker attendance, skills and productivity adds additional insight into the performance of each project and the company. The information can also inform the construction business owner’s bids and operational decisions.
Zach Hoffman, director of field operations at Prevost Construction, integrates jobsite check-in data with Procore. “We rely on [data and software] to manage every aspect of a construction project,” Hoffman said. “The integration was easy, saving us hours every day spent rekeying field data into the project management platform. We can improve jobsite productivity without compromising safety or quality.”
As construction budgets and the labor market get even tighter, construction business owners are investing in digital technologies to identify hidden pockets of cost savings and productivity boosters. One of the fastest paths to a solid return on investment through this strategy is automating paper processes on jobsites and integrating that data with their existing investments in project management platforms.
Since what happens on a jobsite can make or break a contractor, it only makes sense to capture and analyze data from the field to consistently track and measure profitability and continue to use that data to make decisions that are in the best interest of clients and the contractor’s business.