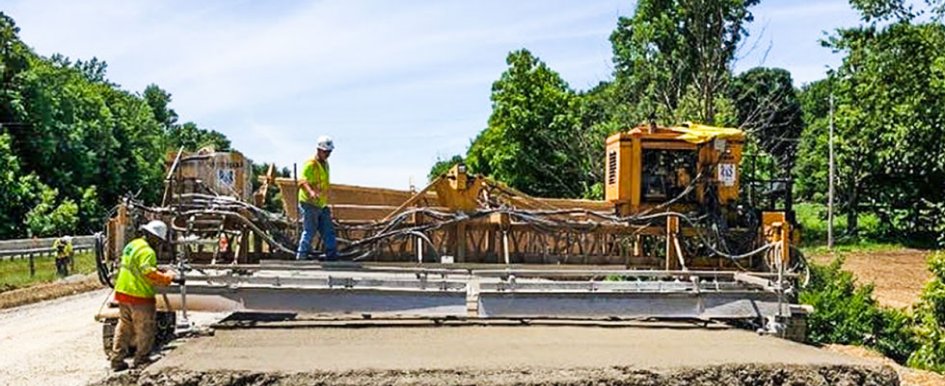
Inefficient construction scheduling is a longstanding problem that often costs the industry and society greatly.
Just a few hours of delays per floor in the construction of a multistory building can cost more than a million dollars. General contractors can incur contractual penalties of up to $50,000 a day for not meeting a project’s deadline. This is in addition to the extra costs for equipment and labor when a project exceeds its projected timeline.
Similarly, public road construction projects that surpass projected timeframes add to traffic congestion, which costs drivers an estimated 21 gallons of fuel and 50 hours of time per year. This adds up annually to a loss of more than $1,080 per commuter and a nationwide cost of over $160 billion. Each United States household, on average, spends $3,400 per year coping with infrastructure repairs and deficiencies.
Yet opening buildings, roads and bridges too early can result in structures of lower strength. This not only reduces their life span but also raises crucial safety concerns. The collapse of the Hard Rock Hotel in New Orleans, Louisiana, while under construction in 2019 and also the Florida International University bridge in 2018 — both attributed to structural flaws — resulted in not only the loss of the properties, but also multiple deaths and injuries.
Inaccurate Testing Methods Cause Costly Delays
One key problem in construction scheduling is the lack of efficient testing techniques for determining the maturity of the cured concrete. Current techniques for evaluating concrete maturity involve creating concurrent samples of the concrete as it is placed. The sample specimens are tested at predetermined times to help determine when the placed concrete can be used safely.
Unfortunately, these samples often do not accurately represent the in-field poured concrete due to differences in the retention of heat and in the exposure to environmental conditions during placement and curing. Samples typically show lower strengths than in-field concrete placements. As a result, this current testing methodology causes unnecessary construction delays — burdening society substantially in time, resources and sometimes physical injuries.
New techniques to determine concrete strength in real time (such as the maturity method), continue to be developed. However, they are still fraught with limitations and cannot address the complex reality of modern concrete mixes and applications that often include various additives, corrosion inhibitors, accelerators and viscosity modifiers that can compromise the reliability and veracity of the testing. This is particularly true when, as commonly occurs, the mix design is altered at the time of placement to address environmental variables.
Smart Concrete Sensors Offer Innovative Alternative
To address this deficiency, Professor Luna Lu’s team at the Lyles School of Civil Engineering at Purdue University is developing smart concrete sensors. These cost-effective and easy-to-use tools have the potential to address longstanding testing limitations by accurately determining proper curing time and other attributes of placed concrete. Instead of concurrent samples that must be destructively tested in off-site facilities at a later time, the sensors are embedded in the placed concrete during construction and measure real-time concrete strength on an ongoing basis.
The sensor technology takes advantage of the electromechanical effect to determine concrete strength and other attributes in just a few seconds at any post-placement time interval. Mechanical vibrations of concrete reflect its strength and stiffness. Lu’s new piezoelectric sensors convert concrete’s vibrations into electrical signals, which are then read through sensor data loggers and processed using unique software and mathematical models developed by Lu’s team. This technology works for any concrete mix design and does not require precalibration or preprocessing, which differentiates this technology from others like the maturity method. The strength information is more accurate compared with traditional off-site samples’ testing.
Accurate concrete strength data for in-field concrete can then be transmitted to superintendents and project managers, communicating the exact time when concrete strength reaches its target value and thereby accelerating construction timeframes by eliminating unnecessary delays and waiting periods.
Better data will allow project managers to efficiently schedule and assign their crews for both building and infrastructure applications such as roads and bridges. Society can benefit from minimized traffic jams and slowdowns and infrastructure lifecycles can be maximized. The potential to decrease or eliminate maintenance costs for bridges, roads, or oil rigs, the increased production rate for precast concrete applications and the general risk reduction are only the tip of the iceberg for the value of this technology.
Early Recognition of Smart Sensors’ Value
The vertical construction sector and the Indiana Department of Transportation (INDOT) are already adopting the smart concrete sensing technology developed at Purdue University. Lu’s team is working with Wilhelm Construction in Indiana to accurately determine the strength of concrete in multistory buildings under construction. INDOT adopted the technology for projects on Interstates 69, 74 and 465.
Lu’s team has also developed relationships with the departments of transportation in California, Texas, Missouri, Colorado and Tennessee to expand the use of this technology in those states. The engineering community recognized the importance of the Purdue team’s innovation when it was honored with the American Society of Civil Engineers’ GameChangers Award.
Smart concrete sensors directly address difficult construction scheduling and related problems that have been without a meaningful solution for over a hundred years. Not only can using smart sensors reduce project cost and time by up to 30%, but the sensors themselves add less than 0.1% to the construction budget — making them economically viable in the cost-conscious construction industry. Real-time concrete strength sensors have an incredible financial and safety value for the construction industry — not only now but to an even greater extent as the Internet of Things develops into a more important part of delivering vital data.