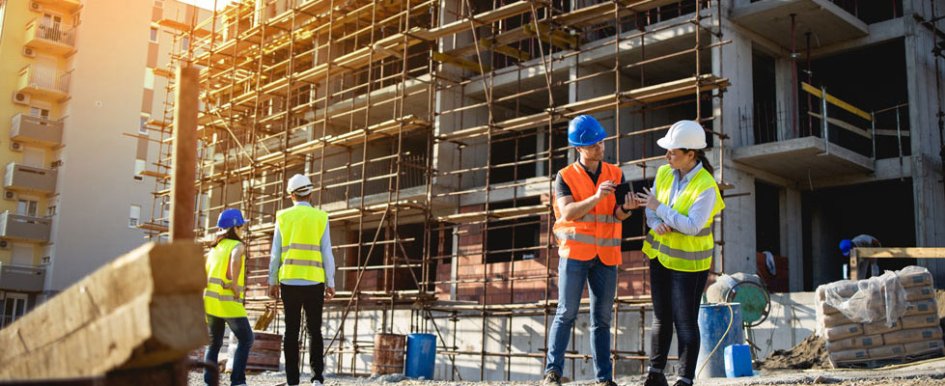
Construction teams face countless risks every day due to high-risk project environments, fluid workforces and a communication disconnect between the organization and its jobsite workers. All of these risks combined can create the real possibility of serious injury or even death.
Consistent, unified communication and high-quality training protocol are critical. Technology has proven to increase production and reduce costs in industries across the board, but it has only recently started to gain traction in construction.
JBKnowledge’s 2018 Construction Technology Report showed that builders are increasingly seeing mobile devices and technology as important tools for safety, yet many companies are not convinced of the value of emerging technology to reduce these risks.
Construction managers can incorporate training through new digital platforms to increase their crews’ awareness of exposures and safety best practices, empowering them to feel prepared, informed and engaged. The following are three ways that implementing new tech on the jobsite is a game changer.
1. Identify & Address Problems Quickly
Technology can help improve project management, training and communication, creating a more seamless work environment for employees and, in turn, helping managers better identify, define and understand the areas that could be problematic or dangerous.
Technology allows companies to apply lean construction to education and training, which, in turn, allows construction leaders to effectively determine where education is needed and deliver training on a timely basis. This, coupled with hazard awareness and other predictive features, can help reduce serious injuries and fatalities. Additionally, the availability of handheld and wearable tech has had a positive impact on safety, general planning and overall jobsite quality.
2. Improve Retention & Accessibility
Each construction project and its timeline is unique, so a one-size-fits-all approach just doesn’t cut it. Exposure-based training through handheld mobile devices is highly customizable and easily accessible for all parties involved—from the home office to the frontline workforce.
Traditional training methods, such as tedious slideshows or daylong, off-site training sessions cost contractors valuable time, money and resources, and they may not result in effective education for workers. Safety huddles and job-hazard analysis are also common practices to convey the necessary information for the construction site that day. However, many participants may not remember or even hear what was discussed in the first place.
Exposure-based training via mobile devices can mitigate the risks and downfalls of each of these techniques by providing critical information concisely and quickly, improving worker retention and saving time. This not only provides workers with the critical training they need, but the information is now more accessible than ever with it sitting right in their pockets.
Increased accessibility is also proving to increase the overall completion rate of training among the workforce. One organization in particular, Pankow, recently deployed exposure-based training through MindForge and is seeing a 98% training completion rate in its workforce—the highest it has ever been. Pankow now has the ability to more easily track the progress of training for each of its workers on any given jobsite. The company has saved more than $12,000 in training time on one jobsite alone.
Mobile training platforms are allowing for a “hands-on” experience, providing frontline workers the opportunity to encounter and be exposed to different situations through 3D simulators, all while in a safe environment. In order to optimize training and jobsite safety, it is critical for each worker to be aware of their own initial actions, attitudes and motivations while in a risky situation to better prepare their response. Ultimately, new exposure-based training is educating people on how to identify scenarios that could put them in harm’s way and to be aware of the potential risks of a specific task or jobsite.
3. Facilitate Communication Among a Fluid Workforce
One of the industry’s biggest risks is that the workforce is constantly in motion, with workers often moving quickly between tasks and jobsites. Many times, foremen and superintendents may have little to no record of their previous experience or training, leaving contractors and subcontractors to take on the risk of ensuring each employee is appropriately trained and aware of the specific risks of the jobsite.
Digital training platforms can help contractors and subcontractors track exactly what each worker has been trained to do and can store the important information, records and reference material digitally in an archive, which can then be accessed at any time from a mobile device.
On many jobsites, communication from management down to the frontline is done through word of mouth, resulting in a huge possibility of information loss. It’s a game of telephone, often leaving the frontline workers in the dark and not empowered to do their best work. Through digital, communication-based training platforms, safety and operations teams can send messages, emergency alerts and even specific training videos to individuals or entire crews in an instant. This type of technology allows for seamless and transparent communication, mitigating uncertainties on the jobsite and possibilities of risk.
Many workforces also have a need for multilingual course offerings. Mobile-based training and communication is helping contractors overcome any language barriers by delivering and enforcing a consistent message and safety culture to ensure everyone who walks on the jobsite receives the same information. Early adoption and implementation of timesaving and lifesaving technology is one way to reduce the common risks that exist on jobsites.
New training technologies aren’t taking workers off-site for a full day and are proving to be more engaging, resulting in fewer possibilities for injury and less insurance and financial risk for the larger organization. This helps bridge the disconnect that exists between top management, middle management and jobsite workers and enforces a unified, safe and productive culture.