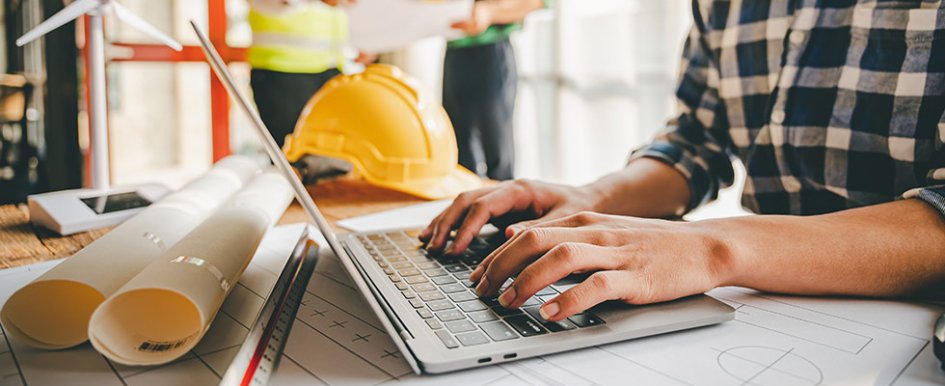
As the world emerges from the COVID-19 crisis, we can clearly see three global trends that will dominate and overwhelm the global capacity to develop and execute capital projects. They are infrastructure, digitalization and decarbonization — the driving forces behind the energy transition.
In the construction industry, the opportunities for growth are enormous, and our capacity to complete projects must keep up with the global demand for buildings, facilities and infrastructure. One recent study revealed that between now and 2060 global building floor area will double, and just the amount of building floor space required will be equivalent to building an entire New York City every month for the next 40 years.
Let that soak in for a minute.
The pandemic has accelerated change in the digital landscape, forcing companies to adapt or go out of business. 5G is changing the way digital networks are being used, and from what I understand, 6G is around the corner. The new gold is data — which requires storage and transmission.
Now layer on top of this the move toward electrification as the primary energy source, displacing hydrocarbons while meeting the infrastructure demands of the digital economy. Behind every energy technology are the raw materials that power it, support it or help build it.
The energy transition is moving to technologies far more mineral intensive than current fossil fuel counterparts. “A typical electric car requires six times the mineral inputs of a conventional car, and an onshore wind plant requires nine times more mineral resources than a gas-fired power plant,” the International Energy Agency (IEA) stated.
According to IEA, an estimated $100 trillion plus will be required over the next three decades to reach net-zero carbon emissions by 2050.
These three big trends compound on each other. Consider the demand they place on basic materials such as copper, steel, concrete, glass, fibers, plastics and the skilled labor that will be required to do the work.
By any estimate, the available supply of building block materials such as lithium, copper, iron ore and rare earths cannot meet the projected demands. So new mines and refining facilities will also be required.
For example, the recent World Bank’s Climate Action report forecasts the 2050 demand for 15 minerals from energy technologies as a percentage of 2018 production. At the top of the chart are graphite and lithium each with about a 500% increase, cobalt with 460% and indium with 225%.
It’s important to note that these big trends are all interrelated. For example, about 50% of carbon attributed to infrastructure is generated in the construction phase. So, in order to meet decarbonization goals, infrastructure must take aggressive action. Digitalization requires infrastructure — cell towers and data centers. Electrification increases demand for both digital and infrastructure — solar, wind, nuclear, transmission lines, charging stations and battery storage.
If that didn’t shock your brain enough, let’s layer on the dearth of people who want to work in the construction industry. By any forecast, if we don’t change our methods to execute projects, we won’t have sufficient numbers of craft workers in the U.S. today, let alone what is going to be needed globally over the next 30 years.
It’s easy to see these trends will create unparalleled challenges and strains on the construction industry and material and equipment suppliers, along with those who mine and refine basic raw materials. These trends will be paced by our capacity to develop and execute projects.
To have any chance of meeting these challenges, real change is required. Improved productivity of the construction industry is no longer optional — it’s imperative.
The time for business as usual is rapidly closing. The pain of the status quo in construction is going to increase exponentially as our capacity to develop and execute projects falls short of expectations.
So, what can we do about it?
Until we recognize projects as production systems and use the science that drives project results, we have zero chance of making significant improvement.
However, even that won’t be enough. We need to free ourselves from the limitations of prior eras of project management and instead focus on a new era of project delivery.
Eras one and two — Current project management thinking has a conventional view of trading off scope/quality, schedule and resources to meet targets on cost and schedule. Variability and inventory are not explicitly recognized in conventional project management thinking, and therefore expose construction business owners to hidden risks.
In the new era three of profitability, construction owners have found they can compress time to market and improve project outcomes in profitability and schedule with an operations science approach to projects, in which the project production management (PPM) framework is used to optimize project delivery. For more information, see “A Gap In Current Project Outcomes” by T. R. Zabelle, H. J. Choo, M. L. Spearman, and E. S. Pound.
In this new era, projects will be highly efficient production systems that are automated with robots doing much of the work, embedded sensors will be tracking materials and signaling for the subsequent work to be done, and drones will be measuring progress.
Artificial intelligence (AI) enabled systems will be ordering materials directly from suppliers without human hands. Facilities will be configured to order. Components will be 3D printed on demand at site. Workers with exoskeletons will be used to assemble components designed in completely different ways from today’s methods. This is not just a fantasy.
Imagine the first Ford factory. It was an amazing leap forward in auto production, making cars affordable for the average family. Fast forward to today and visit any vehicle factory: Robots silently working down the line doing things unimagined just a few years ago. Millions of parts showing up at just the right place at the right time. Consider how the auto worker job today is quite different than in the first Ford factory.
Construction today is still very much like that early Ford factory. We do some amazing things, but not nearly as amazing as what we could and must be doing in the project of the future.
I challenge us, the construction industry, to shake off the status quo and lean into using PPM to start the transformation of how we develop and execute projects.
Real change is not something “they” are going to make — it starts with us. Ultimately, owners who embrace and
lead the change in the approach to projects will be rewarded, and those who do not will be left behind.