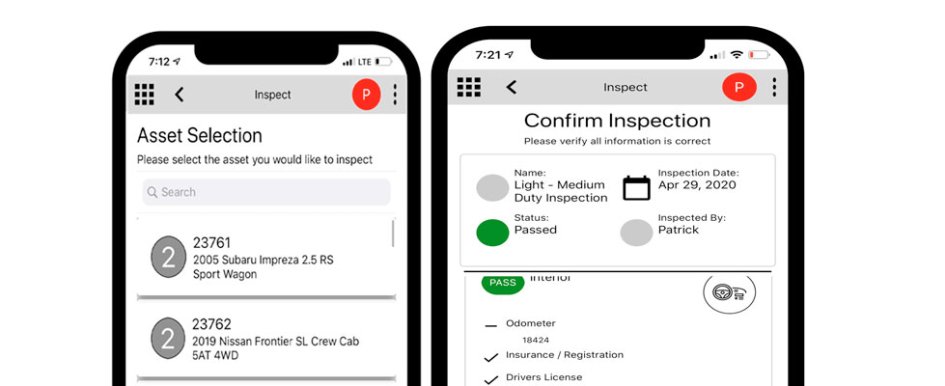
When it comes to construction fleet management, drivers, technicians, maintenance supervisors and managers each have an integral role to play to ensure their vehicles, equipment and assets are up to code by conducting frequent inspections, or they risk being shut down by regulatory government bodies. In addition to asset management and life cycle, safety is an integral purpose behind any inspection—leaders know that if their company isn’t operating safely, it not only puts their fleet drivers and operators at risk, but it also risks public safety, the health of their vehicles, equipment and assets, business productivity, and ultimately, the bottom line.
To put it in perspective: Having a comprehensive fleet roadside inspection program in place can prevent an estimated 14,000 accidents and 9,000 injuries in a year. And this doesn’t even take into account the safety benefits of using a digital inspections tool for your equipment.
Today, safety inspections should look a little different than normal—they no longer need to just account for safety when behind the wheel, but safety as it applies to the health of drivers and operators as COVID-19 cases continue to surge. It’s important that frequent health checks are made a part of the larger inspection process for construction fleets, as companies have a due diligence to ensure they’re operating in the safest way possible.
The Evolution of Inspections
Luckily, inspections today are not what they were a few decades ago, having come a long way with advanced technologies and efficient, streamlined processes. With connected operations technologies, site managers can now use configurable, digital solutions to ensure compliance with inspection protocols of their vehicle, equipment and assets as well as COVID-19 protocols for each individual employee, parting ways with the pen and paper method that many still use today.
Conducting routine inspections allows managers to spot issues before they snowball into bigger problems and not only prevents unnecessary maintenance spend, but also allows construction and fleet leaders to better manage vehicle, asset, equipment and worker availability by preventing unexpected downtime and lost productivity. With the added complication of COVID-19 this past year, incorporating health checks into larger digital inspections processes ensures individual drivers are healthy before they begin a job and potentially violate government compliance protocols.
Ensure 360-Degree Safety for Your firm’s Assets & Your Workforce
When it comes to safety, fleet and construction site managers have plenty to be worried about. But, with the help of modern, digital inspection solutions, managers can ensure their operators are complying with their inspection processes, and that the data from every inspection report is getting back to managers and the maintenance team in real time.
It’s easy to think safety is only a concern when drivers or equipment operators are behind the wheel of dangerous machinery, but managers should include a pre- and post-operations health protocol checklist in their process to account for all COVID-19 safety risks. With the help of configurable, automated technology solutions, managers can account for every single factor that poses a safety risk and check off each box on their inspection checklist:
Before driving or operating machinery, the driver’s inspection checklist should include adhering to COVID-19 protocols, such as entering their temperature, and attesting to the fact that they are wearing a mask when mandated and have had no contact with an infected person. This also includes inspections of every facet of the vehicle. Drivers should be required to include photo evidence at certain checkpoints and signature sign-off of the overall inspection report. This should kick off a notification to the manager if any issues were reported—whether a violation of a COVID-19 protocol or maintenance issue.
After the drive, drivers should incorporate a COVID-19 sanitation checklist, including wiping down the interior of the vehicle, retaking a temperature (especially on longer trips) and confirming a mask was worn when required. They should also plan to conduct a post-use inspection and, as mentioned earlier, no post-trip inspection should be able to be marked as completed without photo evidence and driver signature. As with the pre-trip inspection, managers and maintenance will be alerted in real time to any issues.
Proactive Safety Means Compliance to Regulatory Laws & COVID-19 Protocols
With the help of advanced, data-driven connected operations solutions, managers can easily perform inspections and health checks to ensure their assets and workforce comply completely with government regulations, such as Department of Transportation (DOT), Occupational Safety and Health Administration (OSHA) laws, which can mean hefty fines for those found in violation.
For example, OSHA serves fines of up to $132,598 if a flagrant violation occurs and violating COVID-19 safety procedures would certainly fall in this bucket. This is a steep price to pay, when it could be easily avoided through routine health checks and an inspection checklist.
When it comes to health checks and COVID-19 protocols, much can be done by companies to ensure compliance and government regulations are being followed. These protocols can include—but aren’t limited to—ensuring clean driver hygiene, abiding by the maximum number of people allowed per vehicle (limiting it to only one or two when possible), wearing disposable gloves, frequent sanitations with disinfectant cleaners and frequent communication with the full team. Though seemingly small things, all are necessary for compliance and business continuity.
Asset Longevity & Cost Savings
Cost savings, while always top of mind, has become increasingly important during the ongoing pandemic—as many companies have to be extra cognizant of every single dollar spent, eliminating unnecessary costs when possible. By integrating frequent health checks into larger inspection programs, companies can optimize their assets, productivity and maximize return on investment.
A modern inspection solution is one that is integrated into an overall connected vehicle and asset operations solution, providing further capabilities to reduce overall spend and extend the life cycle of a construction firm’s vehicles, equipment and assets, while maximizing productivity of the workforce.
New digitized inspection solutions include predictive analytics to help managers make informed recommendations for when a routine maintenance function should be performed, on a specific area before an issue goes undetected and the vehicle or asset is out of commission altogether. They also can alert managers right away if an employee is sick, or a health protocol unaccounted for, saving the company from the possibility of large fines later on for violation.
Double & Triple Check
Frequent health checks and inspections through advanced digital solutions enable faster equipment defect reporting, proof of due diligence and the ability to uphold compliance regulations, ensuring all employees are as safe as possible. With connected operations technologies and automated, real-time alerts, managers can initiate service requests and detect potential protocol breaches the moment an issue is spotted during an inspection or health check, allowing them to run both a responsive and truly preventative maintenance process, while keeping employees’ safety as their No. 1 priority.