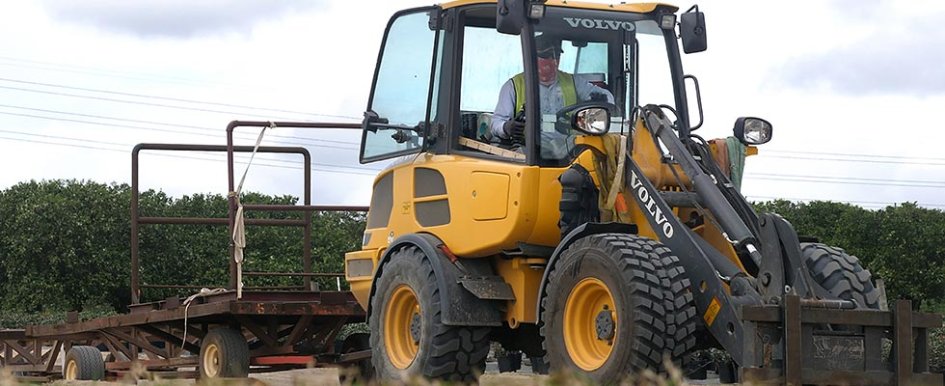
Breakdowns and major repairs cause the brunt of unexpected downtime for fleets — often due to poor preventive maintenance (PM) compliance. Fleets can minimize unexpected downtime by improving maintenance programs and compliance and creating a breakdown response strategy.
Herman VanDenBogaert, raw materials purchasing manager for Florida-based construction and landscaping company Cherrylake, manages more than 370 vehicles across four divisions.
Having seen his fair share of unexpected breakdowns and asset pileups in the shop, VanDenBogaert put a plan in place to streamline and improve maintenance processes, leading to a $150,000 reduction in repair spend. He also implemented a strategy for quickly tackling breakdown events to reduce downtime.
Consolidate Fleet Data
Many fleets using pen and paper or spreadsheets to track asset data find inefficiencies when analyzing the data collected. This is also the case for fleets using multiple fleet solutions that don’t connect. VanDenBogaert struggled with this very problem.
“There was data for our fleet in like 12 different data points, and there was no one thing that was kind of feeding them all together,” he says. “Anytime I made a change or someone else made a change in the fleet, I was having to keep up with all these databases.” When he looked at service histories and associated costs, it was a time-intensive ordeal.
Cherrylake adopted an integrated fleet management software (FMS) to consolidate the fleet’s data points for better visibility and automated reporting. This action helped Cherrylake quickly determine areas in the fleet needing improvement, such as high repair volume and spend, and provided VanDenBogaert insights to implement positive change.
Follow the Numbers
Data consolidation is so important because of the insights it provides. By analyzing reports based on collected data, fleets can pinpoint process inefficiencies and areas of inflated spend. “Our repair costs were above half a million dollars,” says VanDenBogaert. “[At the time], I had three mechanics, and I started to ask: ‘How much time are they spending doing repairs compared to preventive?’” After following the numbers, he determined the reason behind its high repair spend: “We were being reactive instead of proactive.”
“We started to [break down service spend] into what things we were buying for PM, what things were repair costs and what were our outside repair costs,” VanDenBogaert explains. “In breaking down that figure, we were also trying to determine which costs could be cut by adding another mechanic to take care of some of the outside service work.”
With better visibility into its fleet, Cherrylake used the data collected to pinpoint and correct a major pain point in its PM process, leading to fewer breakdowns, less downtime and a 30% reduction in repair spend.
Prioritize Preventive Maintenance
Identifying the time and budget your fleet spends on proactive versus reactive maintenance can provide insights around the core problem so you can formulate a strategy for improvement.
For VanDenBogaert, this meant prioritizing PM. He encourages smaller, more regular preventive actions to stave off the events that cause catastrophic breakdowns. This includes making sure equipment is well oiled and scheduling vehicles for standard maintenance on a regular basis. “We saw our teams were throwing a lot of money into repairs instead of preventive. Repairing the brakes on our larger loaders can cost anywhere from $12,000 to $20,000, so that got us more like, ‘Hey, make sure you guys are greasing, using the right fluids,’” VanDenBogaert says. Cherrylake used FMS to implement PM schedules for its assets with set reminders to avoid missing any service. VanDenBogaert says that digital inspections have also helped reduce repair instances.
According to VanDenBogaert, “With [FMS], using the inspections, getting issues made, being able to communicate that straight to my mechanics, and they repair it the next day and sign off on it. Everything gets knocked out. It’s become a routine now.”
Weigh the Value of Spare Fleet
Breakdowns are unavoidable, even with the best of processes; for that reason, some fleets keep more vehicles than needed for when those breakdowns occur. VanDenBogaert learned if you pay attention to the PM schedule, extra vehicles can turn out to be a burden in the long run. “We were having a lot of issues with guys not having a truck for a week and a half, two weeks, [so] we used to keep two to three spare trucks just for the construction and maintenance teams,” he said. “We had to keep vehicles in our fleet that were just used as spares for breakdowns. Imagine the cost: You’re depreciating two big trucks — 3500s — for a couple more years. It adds up quick.” After creating a breakdown response strategy, Cherrylake has reduced unexpected downtime enough to no longer require spare vehicles.
Monitor Recurring Asset Issues
Identify recurring asset issues to reduce downtime. Comprehensive service histories provide insights into recurring issues, including their source. VanDenBogaert found that repetitive services accounted for most of their maintenance and inventory costs.
“Tires, man. They’re on everything you’ve got, right? And if people don’t mind or take care of [them], those are the big ones that can just cause a lot more damage and problems.”
In order to lessen the impact tire costs have on the fleet, operators are paying closer attention to the details of their pre-trip inspections to catch things before they create a major repair event. By monitoring recurring issues through daily inspections, it’s less likely that an issue will slip through the cracks.
Create Response Processes
Communication is the key to efficiency. If a team in the field has no way to communicate in real time to managers about vehicle or equipment issues, those issues can become costly problems. Communication bottlenecks impede productivity in the shop, on the road and in the field.
Cherrylake’s communication used to look much different: “There would be two or three people involved before the mechanic: the operator’s manager, then whoever the fleet manager is, communicating back to the shop. And sometimes the operator would just show up and say, ‘This is broken.’ Then he’s not in the field [and] the manager doesn’t know where he’s at.” Using FMS for service reminders allowed Cherrylake to create a smoother chain of communication, which sped up service response times. VanDenBogaert found he could improve breakdown service time by standardizing the fleet. Using similar vehicle and equipment types/brands can help decrease time in the shop and reduce the cost of parts.
Downtime can affect the entire business, so proper fleet maintenance is crucial. By tracking inefficiencies across your fleet, you can create a strategic plan to improve response processes, streamline service workflows and get better control of downtime.