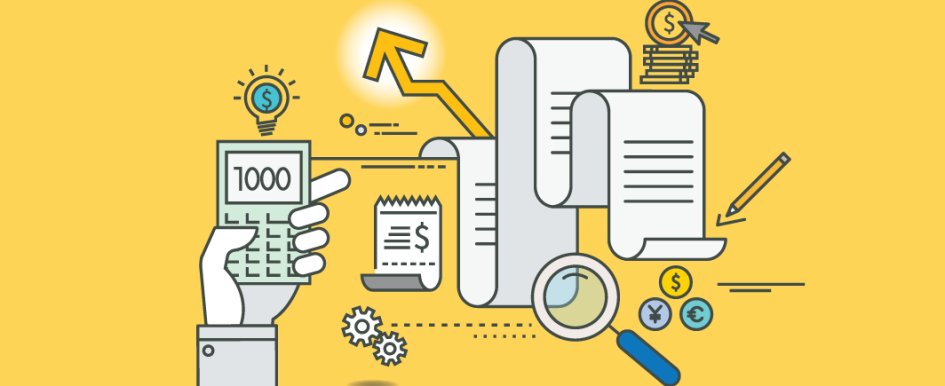
What if you could predict equipment breakdowns before your machine showed any signs of distress? What if you could extend the life of your assets, increase their utilization and reduce machine downtime? Good news: By using a cloud-connected telematics platform, you can.
Telematics hardware installed on equipment engines monitors your machines’ vital signs and alerts you to any performance abnormalities. With telematics, you can access a comprehensive view of the health of every machine.
What’s more, you can use that data to inform maintenance processes and to predict—even prevent—problems. Telematics-enabled maintenance keeps your machines in top condition, allowing them to run more hours on the jobsite with less unexpected downtime.
Getting Started With Data Collection
For the most informed and educated picture of each of your machines, you should collect data the moment you get your equipment. The sooner you begin collecting machine data, the more you’ll know about that machine over the course of its life. Plus, with digital data collection, it’s simple to begin.
Digitally collected data is easier to gather, organize and interpret. Many construction firms are using computerized maintenance management systems (CMMS), which are usually built into the company’s telematics solution for exactly this reason.
The data your CMMS collects creates a comprehensive history of your machines that you can access at any time. And telematics keeps your maintenance schedule on track. If you’re using telematics to its full potential, you’ll be alerted when it’s time for regular maintenance and if engine irregularities are detected.
However, data is nothing if it’s not used to make informed decisions. Telematics capabilities don’t only make it easy to collect and interpret machine data, but also make that information immediately available to your field employees in real time. Access to granular equipment data helps everyone on your team understand and contribute to the overall health of your fleet.
Additionally, telematics solutions allow you to generate comprehensive reports that dig even deeper into each machine’s operating health so that you and your team can make better decisions about servicing equipment, optimizing jobsite utilization and productivity, increasing equipment return on investment, and more.
Predictive Maintenance Means Maximum Uptime
When it comes to servicing construction equipment, many fleets rely on reactive maintenance. Without telematics, construction fleets can only know to work on machines once they have already broken down or when they come back from a jobsite in less-than-stellar condition. Reactive maintenance causes problems like:
- Increased, unpredictable downtime—When your equipment goes down, work stops, a service technician has to identify the issue, and only then—assuming you don’t have to order any parts—can it finally be fixed. Downed machines cost money and waste time (which, in the end, also contributes to revenue loss).
- Ragged machines—Repeatedly running machines until they break down puts unnecessary stress on equipment and leads to shorter life cycles.
- Lack of insight—You cannot learn much from a disconnected fleet. Without telematics, you simply do not have access to concrete equipment data that allows invaluable insight into machine efficiency and productivity.
The most effective maintenance program utilizes both preventative and predictive maintenance. Your CMMS tracks all machine maintenance to keep machines on their ideal service schedules. But preventive maintenance alone doesn’t eliminate the unpredictability of breakdowns or help spot early signs of a problem. Proactive, tech-enabled predictive maintenance is the most effective way to extend the life cycles of your machines. Why?
- Fewer breakdowns—When you can see how your machines run on a granular level, you can spot the signs of a breakdown and prevent it.
- Complete, accurate records—Data gathered through telematics is collected straight from the controller area network (CAN) bus and creates digital records to ensure quality and accuracy.
- Peak machine performance—Only the machines operating in top condition can ensure maximum utilization.
Constantly monitoring your assets with telematics helps you learn each machine’s ideal operating conditions. Over time, telematics solutions also memorize the engine conditions that are likely to lead to a breakdown, and as it learns, it improves the accuracy of the asset diagnostic alerts you receive. The longer you collect machine data, the clearer the picture of individual asset and overall fleet health you can assemble.
Think of it like going to the doctor. If you get regular checkups, it’s more likely your doctor will spot something out of the ordinary. But if you only go when you’re sick, it’s too late for the doctor to help prevent the illness. A telematics platform acts as a full-time engine doctor by running tests and issuing diagnoses in real-time.
Better Data Means Better Decisions
Complete, accurate data is essential for compiling a clear picture of fleet health and business operations. There is a seemingly endless list of data that informs your telematics solution’s interpretation of engine behaviors.
You can program your own conditional alerts in addition to basic warnings like low fuel, but the advantage of a telematics solution’s predictive capabilities is the ability to learn how each machine operates. As information is collected, your alerts become tailored to each asset, based off of the machine’s previous operating and maintenance data.
Telematics solutions store equipment data and establish digital machine history records, so you can create comprehensive fleet health reports. And, when all of your data is stored and available on one platform, your team gains a holistic view of your entire fleet. In turn, everyone from service technicians to machine operators to equipment buyers can access valuable information that helps them make better decisions on the job.
This holistic view of your assets is essential to creating clear communication across your workforce and productive workflows. You and your team can pinpoint machines that idle too long, waste fuel or cost the company money (instead of earning it) in a multitude of other ways. When it’s easy to see those problems, it’s easier to fix them quickly.
With a cloud-connected telematics platform, the insights you gain go far beyond asset health. Aggregating data from every facet of your business, from the jobsite to the back office, telematics offer a holistic view of your entire operation and a better understanding of how your jobsites operate. With thorough, accurate data to help you understand how each part of your business runs, you can confidently make impactful decisions that improve workflows across departments.
There’s a reason for the phrase “runs like a well-oiled machine.” Equipment operating in its best condition helps projects run smoothly, helps employees stay on schedule and keeps your projects on budget. With telematics, you’ll have a fleet of well-oiled machines running like the day they arrived on the lot.