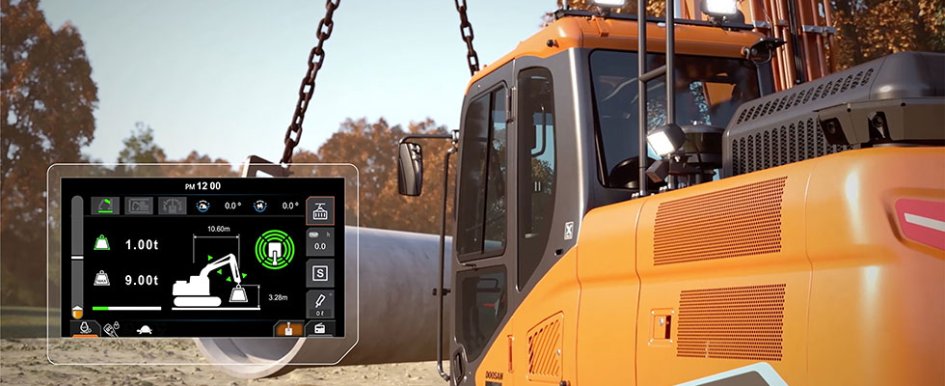
Today’s next-generation crawler excavators use a variety of smart technologies, such as electrohydraulic control systems, to help operators achieve better levels of productivity, safety, accuracy and jobsite efficiency.
Fully electronically controlled excavators combine electronic intelligence with the flexibility of highly efficient hydraulic components. Unlike standard excavators, which have pilot hoses sending the signal for a specific function to control the machine’s bucket, boom or arm, the electrohydraulic system is fully electrical. A computer tells the pilot system and the main control valve what to do the moment the operator starts using the joystick.
Let’s take a closer look at these machine-assisted technologies found on electrohydraulic excavators.
How Smart Excavator Tech Assist Offers More Precision
You’ve likely heard of grade control systems, which prevent excavators from digging too deeply and enable precise measurements by using satellite systems, GPS and laser technology. However, some of today’s electrohydraulic excavators are equipped with a grade-assist mode for accurate grading and quicker cycles.
An electrohydraulic control system can include the following features:
- Programmable joystick switches for ease of operation
- Fully electronic joystick
- Swinging sensor
- Equipment sensors on the boom, arm, bucket and upper body, including a laser catcher
Grade Assist: Dig Smarter, Not Deeper
When excavator operators activate the grading system, a touch-screen setting enables them to set the assist mode, allowing the computer to help the operator through audio and visual displays. All the operator has to do is pull the arm function, and the machine controls the bucket and boom automatically to maintain the desired grade or slope. The touch-screen monitor can give operators better control over the intended direction of travel as well as more precision when setting the bucket-tooth depth, height and slope in earthmoving and grading applications.
It also enables advanced machine guidance and machine control systems, including 2D and 3D grading systems. The 2D systems let operators work off a single plane, such as straight-line trenches, point A to point B.
The 3D systems allow variable distances, like a curved trench or line, for more complex projects. For instance, if operators are trenching to install a sewer system with the 3D system, they can set the slope and maintain the slope by looking at the touch screen. As operators get close to the determined depth, the system will change colors and an alert will go off to notify them on how close they are getting to slope and depth.
In addition, many excavators are equipped with laser receivers, so operators don’t need to reset the depth each time the machine is moved to another location. The receiver will display an icon on the touch screen so the operators know they can continue to dig at the same parameters.
At the end of the day, grade assist results in game-changing improvements in productivity and efficiency for even the most novice operators.
Fine Swing Function: Precise & Safe Lifting
Most excavator operators have experienced shaking at the beginning or end of the swing movement when lifting an object. Activating the fine swing function gives operators greater control when lifting an object and better accuracy when placing it. It also increases the safety of operators in certain lifting applications, like pipe laying, and can prevent damage from the object falling from the excavator. Fine swing can be engaged and disengaged manually, giving operators more control. When the function activates, the overrun disappears, allowing the excavator to smoothly reach maximum swing speed while removing the shock from the turn. Operators can turn off the rotation, or slew, and brake to prevent material loss from the bucket.
Virtual Wall Settings: Safer Operation in Tight Spaces
New precision technology features, such as a virtual wall setting, help operators improve their safety and productivity when working in confined spaces. For instance, if there is an obstacle on one or both sides of the machine, the operator can set limits, so the machine won’t swing past that. They can also control the settings for arm out as well as set ceiling and floor limits. The function can be overridden at any time.
Onboard Weighing System: Load With Confidence
Instead of guessing how much material they are loading into a truck, an operator can work more confidently with an onboard weighing system.
This technology accurately measures and displays the material in the excavator bucket via a touch-screen display, which provides important notifications for operator performance.
Lift-Assist Mode: Prevent Overloading
Excavators regularly lift or crane objects on jobsites, so using lift assist allows operators to remove the guesswork when lifting objects. This function measures and displays the current weight of the bucket as materials are being loaded, as well as the tipping load, and alerts the operator when the total loading weight is exceeded.
The sensors are accurate to within 3%. This function can reduce concerns about tipping the machine if the object is too heavy.
What's Next for Excavator Automation?
Many equipment manufacturers are introducing next-generation excavators with advanced electronic technologies to deliver smart performance, and the trend isn’t slowing down anytime soon. These technologies are designed to help make operators work smarter — not harder — on the jobsite.