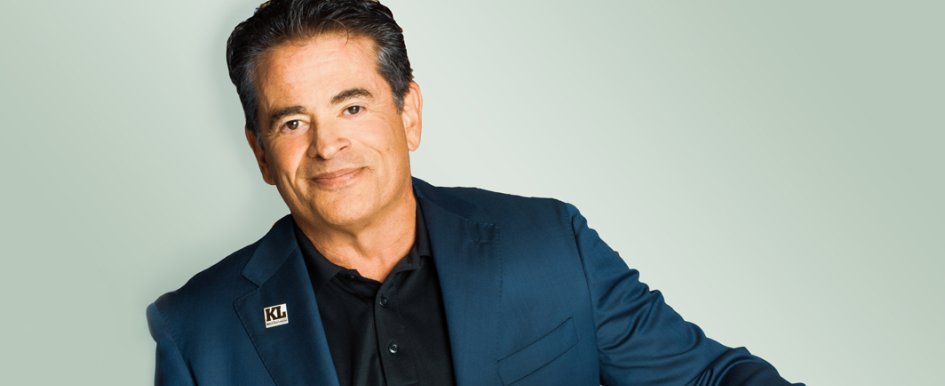
Building information modeling (BIM) is described as a unifying tool, a direct path to collaboration. In many instances, however, this is not the case for construction projects. Why? Because the owner/operator—a key player in the building life cycle—is often left out of the process until the very end. And this needs to change.
The process of using BIM should be open to the entire project team, and the leadership role necessary for making that happen lies with the general contractor. Similarly, BIM technology should not be considered a tool exclusive to architects, engineers and other trades, but rather a methodology for improving the workflow of each individual involved, from initial design ideas to actual building operations.
Altering your company’s mindset around BIM requires changing your approach to project delivery and getting teams to use foresight. Everyone involved should understand that their work carries on after the construction equipment leaves the jobsite. And, ideally, it results in the legacy all contractors want to leave: a well-built, smooth-operating, fully functional structure.
But to reach that goal, the general contractor must bring the owner into early discussions about critical building functions before the shovels hit the ground, and this involvement should continue throughout the project review stage, bringing benefits that will be visible to all.
First, however, the general contractor may need to coach the owner on BIM technology. The owner, who may be unfamiliar with the technology, may not have the same understanding as the general contractor, construction manager and subcontractors of the technology’s advantages for conflict detection and reducing rework.
For example, the owners might want a four-story, square building. If the owners do not participate in the iterative design process, waiting instead for a paper drawing, they miss the opportunity to see the three-dimensional designs and to better understand how and why changes are made.
They will then see the building rendered as a two-dimensional image, in lieu of a more realistic depiction on a computer screen through augmented reality (AR) or viewing it with virtual reality (VR) headsets. As a result, they lose the chance to experience BIM’s ability to offer a full understanding of the project.
Current Observations
Nearly every project currently being designed, coordinated, built and commissioned is leveraging BIM and virtual design and construction (VDC) techniques. In many cases, the process centers around the construction manager and the subcontractors instead of being focused on the owner/operator.
Resistance to using BIM and VDC often comes from the position of, “This is how it has been done for years.” I have been monitoring firsthand the evolution of BIM for 15 years from the different vantage points of design/engineering, subcontracting/fabrication and construction management. For the most part, in each project, the same results are delivered—the owner receives CDs, DVDs, accompanying three-ring binders and maybe a Microsoft Excel spreadsheet containing all the most important data.
Ten years ago, there was a semblance of BIM/VDC, and a large portion of content was developed and coordinated in an early BIM-based workflow. But the process lacked valuable operations, maintenance and commissioning data. Even in 2018, this disjointed process still existed for many construction projects that were specified and subsequently turned over to the owner/operator with the critical data separated from the BIM deliverable.
While some specifiers, such as architects and engineers satisfy their clients by requiring a spatially accurate model as a final deliverable, this is only part of the insight that BIM is capable of delivering.
Of course, there are exceptions. More complex projects, such as medical facilities, data centers or pharmaceutical production buildings, tend to use BIM because the end users can “walk” through the facilities and determine if the location or scale of assets is appropriate or needs to be adjusted, all before construction starts. In these cases, the needs or requirements are very specific. But even with less complicated projects, there are notable benefits. With a 3D model for commercial office buildings, owners know exactly where electrical, plumbing and fire equipment will be located.
Scheduling their installation can be better coordinated before work begins, as no guesswork is involved because the team is not relying on paper drawings. The true power of the BIM-based workflow is invaluable to owners/operators. It links critical building information for the owner/operator and enables them to audit every aspect of their facility, including where elements are located (even those concealed by walls or ceilings).
They gain the necessary access to mine critical data from these elements, which affords them intelligent operations and maintenance programs, maximizing the life of their investment.
The Final Product
Owners have the power to say, “I want a fully coordinated and functioning model with asset management data turned over at the end of the project,” and join forces with the general contractor and designer to ensure integrated project delivery. Owners pay for the work, and therefore, have the right to specify what they want in a request for proposal or request for quote.