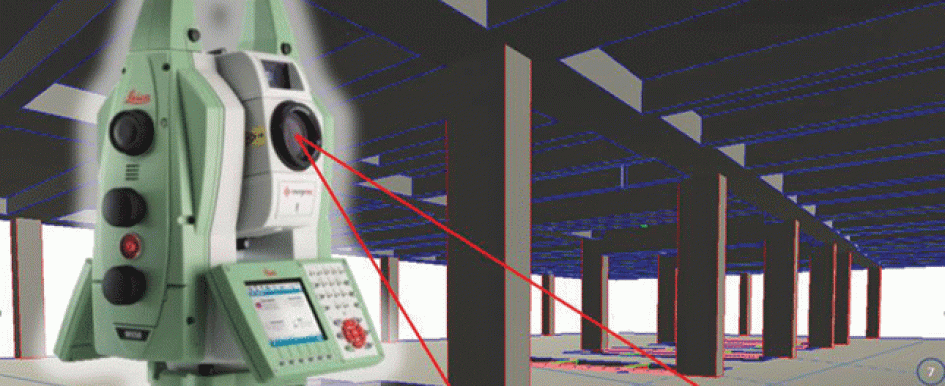
Many construction firms are aware of the benefits of using building information modeling (BIM) to provide conflict resolution by identifying problems before they happen and to better facilitate building systems integration. BIM has a proven return on investment in construction: A study by the Stanford University Center for Integrated Facilities Engineering (CIFE) on 32 major projects using BIM indicates that BIM eliminates up to 40 percent of unbudgeted changes, provides savings of up to 10 percent of the contract value through clash detections and provides up to a 7 percent reduction in project time. According to a McGraw-Hill Construction SmartMarket Report released in 2012, 74 percent of North American construction firms in the $4 trillion global building industry have adopted BIM in some capacity.
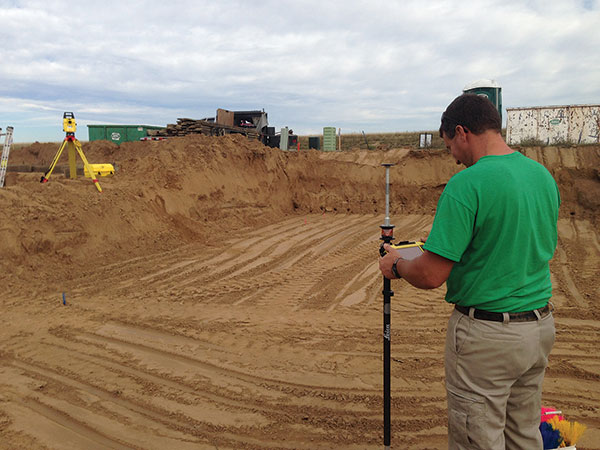
However, for many project teams, the benefits of BIM stop in the office. Rich digital models are often converted to 2D paper drawings for use in the field, where guesswork and manual layout processes can cause errors that might not become evident until later. Additionally, on renovation or retrofit projects, the models themselves might contain errors, because many models are developed from outdated and inaccurate as-built paper drawings. These inaccuracies lead to problems in the field during construction, which drive up project costs, increase risks can even derail an entire project.
Closing the Gaps in BIM
At the core of BIM is an intelligent 3D model that an entire project team can use to achieve higher quality design and construction. In its most basic form, BIM begins when designers create these 3D models using modeling software in an office environment. The longer the information stays in 3D form, the longer project teams can maintain the integrity of the highly coordinated 3D model. Additionally, knowing how accurate that model is and where the data originated is an important part of the BIM process. For this reason, BIM should be a complete process that begins before design, continues through construction and is enriched with real-world information at every stage.
The challenge occurs when trying to transfer digital information to a jobsite and then from the jobsite back to the digital world. Many construction teams simply are not equipped to handle digital information in the field. The tools themselves have been a limiting factor, with traditional hardware and software products unable to manage the information necessary to complete the digital-to-field and field-to-digital connections. As a result, while many construction firms and general contractors aspire to be “full-BIM” service providers, most find themselves only at the beginning stages of BIM implementation or, at best, using a hybrid BIM approach that relies on a combination of 3D and 2D information.
Fortunately, recent advances in technology are helping close the gaps. In fact, according to the McGraw-Hill construction study, the top two emerging BIM trends in construction are digital as-built capture (point clouds), which are made possible through advances in laser scanning technology, and construction layout with total stations (also called digital layout), which is made simpler with the latest generation of robotic total stations and easy-to-use field software and controllers. Through these and other developments, the benefits of BIM can be extended to the field, and field data can be brought back to the office to complete the BIM cycle.
Connecting BIM to Reality
In an ideal BIM work flow, the project team captures reality and informs the 3D model with highly accurate, as-built point clouds. New design models are then created around the as-built point clouds, and construction layout points are added to the model. These points are then replicated on the jobsite using tools such as total stations and multistations (a new type of total station that has the added ability to capture laser scan data) to bring BIM to reality.
During construction, as-built information is captured with high-definition scanners and multistations. The point clouds and discrete measurement points are compared to the as-designed model to immediately identify deviations and prevent expensive downstream coordination issues in the field.
Consider a typical renovation or retrofit project that relies on existing as-built drawings, which are often outdated and incorrect. Unfortunately, these inaccuracies might not be found until the construction phase of a project, where unexpected changes have the potential to ruin both the budget and the schedule. However, when accurate as-built data in the form of cloud points or discrete points is captured and used as a basis for planning construction in a computer-aided drawing (CAD) or BIM environment, builders have assurance that the model is correct as designed.
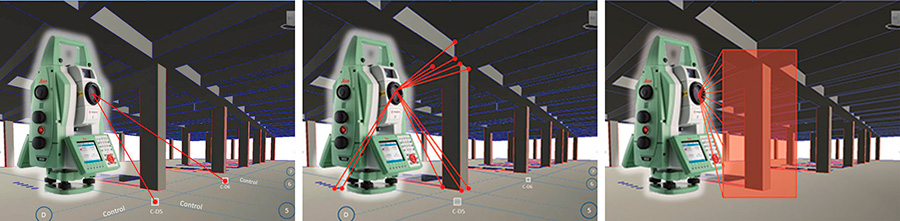
On new construction layout, the accuracy of the coordinated model can be replicated on the jobsite by adding BIM layout points to the model and handing it off to the field for use with total stations, multistations and 3D laser measuring devices. This process creates a “paint-by-numbers” installation in the field, which results in fewer errors and changes in the field and a higher level of predictability of project outcomes. Similar tools can be applied in mechanical, electrical and plumbing (MEP) layout, where speed and accuracy are essential.
Quality assurance is another area where connecting BIM to reality can bring measurable benefits. For general contractors, keeping projects on time and on budget requires closely monitoring the quality and accuracy of the work that subcontractors perform. By measuring the quality of construction throughout the project with total stations, multistations or laser distance meters and by bringing this information back into the model, owners can predict conflicts or problems before they occur, preventing rework and waste.
Tailoring BIM for Maximum Value
A “full-BIM” process can seem like a lofty goal for a company that is just beginning to use BIM. The first step is understanding the “lay of the land”—the hardware and software needed for BIM work flow and how they fit into the business. From there, a company must strategically choose a starting point that will yield the best return on investment. The good news is that solutions are available for contractors in any stage of BIM adoption. For a concrete construction company that is primarily using a 2D paper process, robotic total station layout might be the best place to begin. Conversely, a firm that has completely migrated to multidisciplinary coordination with BIM can take advantage of improved work flows to extend BIM benefits to the field and back to the office.
Even companies that might not consider themselves BIM adopters can now take small steps to improve the efficiency of the layout process and position themselves to expand their BIM process in the future. For example, Craig Poortinga, managing partner of the Loveland, Colo.-based concrete construction company Walrite LLC Colorado Foundation Contractors, saw a substantial reduction in labor, waste and rework when his company moved from tape measures and string to digital layout with a robotic total station. In fact, the savings were so substantial that Walrite achieved a return on investment within two months of using the robotic total station.
“It’s a daily savings for me,” Poortinga says. “I’m not only saving on those parts of the job (the crew doesn’t) need to do anymore, but I can have them focus on other parts of the job that make it better. Instead of having three guys together to do a layout, one guy can do that while the other guys focus on the other details of the job.”
The company saves approximately $300 to $400 per job on time spent by employees, with an average of a job per day, for a total savings of roughly $1,500 to $2,000 per week, or more than $100,000 in savings per year. Although the company has not yet been involved in any projects with a BIM requirement, Poortinga sees the value of moving to a BIM work flow.
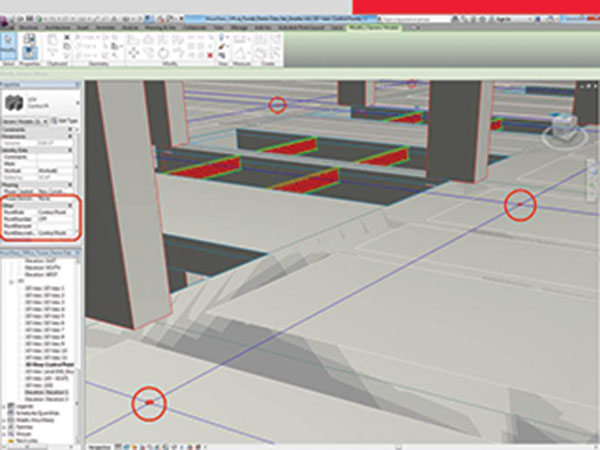
On the other end of the spectrum, companies that view BIM as an integral part of their business can make the process even more interconnected by leveraging technology to enrich their models and enhance their capabilities.
“BIM is an evolving process that continues to improve through experience, the development of standards and the continued advancement of technology,” says Jason Waddell, director of virtual building services for the Beck Group, an award-winning development, design, construction and technology firm and a leader in BIM and virtual design and construction (VDC). “Through BIM, projects are becoming more transparent and more intelligent, with less rework and fewer mistakes. By harnessing tools such as laser scanning, service providers on the leading edge are building intelligent structures faster, cheaper and better.”
The considerable rate of adoption signifies that BIM not only has value but also is becoming a priority for all players in the construction industry. The return on investment is clear. BIM users have identified some of the biggest values of BIM as a way to reduce errors (which reduce rework and, ultimately, costs), increase profits, maintain repeat business and market new business to new clients.
Patrick McLearny, CEO of architectural firm HOK and chairman of buildingSMART International, predicts that during the next 10 years, building owners will demand BIM as a precondition, which he says “will usher in a new era of accuracy, quality and sophistication,” according to the SmartMarket report.
To remain competitive, construction business owners must go beyond the current applications of BIM and fully connect the digital world to the jobsite.