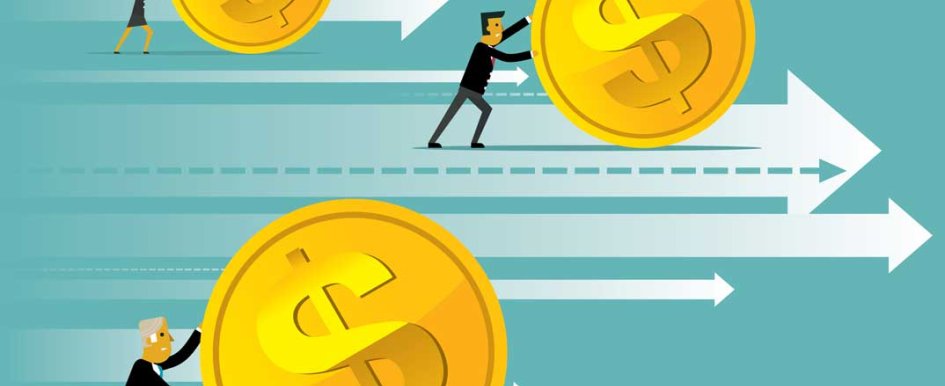
The No. 1 challenge many contractors face is profit shrinkage or profit margin fade. This recurring problem appears when final construction job cost comes in higher than the bid or contract project budget. As a business coach, I see numerous contractor income statements every year. I often hear company owners say that they bid using a 15-percent markup for overhead and 10 percent for profit.
But, after studying their year-end, profit-and-loss statement, many business owners only end up with 20-percent gross profit. I ask them what happened to the other 5 percent. They generally don’t understand why they experienced profit shrinkage.
Causes of Profit Margin Fade
Estimators bids jobs using their standard production crew rates for labor and equipment. Completed jobs often cost more than the bid budgets. Profit margin shrinkage can occur for many reasons, including:
- The estimator uses the “blind-man method” of bidding. This occurs when he/she closes his eyes and guesses how many hours the crew will take to complete a task.
- The estimator uses the “mystery method” of bidding. This occurs when he/she uses a standard square foot price to bid work. For example, to build and pour concrete sidewalks, he/she estimates $5.75 per square foot for total labor and material versus calculating the exact production labor, equipment and material required.
- The estimator uses a percentage adder factor to cover required supervision, general conditions, cleanup and mobilization on bids. For example, on a $100,000 job, he/she might add 5 percent to pay for these costs, which may or may not be the right amount to cover all these expenses.
- The estimator misses several items or project components required to complete the scope of work.
- The estimator underestimates the schedule or time required, and the overall project takes longer to build than estimated. In another scenario, the field crews work slower than the time estimated to complete the work, causing job costs to increase.
- Field crews were not very efficient, which can be caused by many factors, including poor supervision, little or no pre-project planning, unanticipated, additional move-ins, lack of proper scheduling and bad weather.
- The crew leaves the job before it is complete to get to another project. They have to come back several times to finish their work and the punch list.
- The estimator uses out-of-date, too low or too optimistic production rates to calculate the total labor or equipment required to complete the work.
- The field foreman was never given the project labor production budget or goals for crew hours. He/she also wasn’t given any updated status reports throughout the project. The foreman wasn’t held accountable to meet the job goals for labor and equipment hours either.
- The estimator didn’t go back after projects were completed to verify that the labor and equipment production bid rates used were accurate versus the final job costs. The bid rates were not adjusted properly to make sure they were right to use for future bids.
In order to eliminate profit margin fade and ensure that all projects hit the estimated job budgets for labor and equipment, contractors have to invest time and money to implement the systems required to keep the wheel of profit spinning.
1. Estimate the right number of crew hours
Prepare your construction estimates using unit prices for labor and equipment production based on actual cost history of the quantity of items installed per hour. For example, it generally takes an average of one man-hour to install and grout 10 masonry blocks, install three downlights in a ceiling or dig 100 feet of sewer trench. After the estimator completes the quantity takeoff and estimates the number of man-hours to complete the project based on accurate cost history production rates, he/she should then meet with a field superintendent or foreman to verify that the estimate seems right. Together, they should agree on the total hours required to do all the work before the bid is finished.
2. Preplan to hit the budget
After bids are submitted and your company is awarded a contract, the project team meets to plan the job. Get the estimator together with the project manager, superintendent and foreman to review the estimated budget in a preconstruction turnover meeting. Review the scope of work, draft a detailed field work plan, determine the right crew size, discuss any omissions in the bid and make the necessary adjustments to the project budget. Now, combine or adjust cost codes to allow the field to track their time in a simpler version of the budget. Make sure time cards match the actual job budget and are set up to allow for easy time-card coding and tracking and a weekly job-cost update. Also, break down the budget by job phases for longer duration projects. This process will allow your team to know their production goals for the tasks required to complete the job.
3. Build the job on budget
With clear labor hour and equipment goals for the crew, the field can now keep track of their progress against the budget. Have your field crew complete their time cards coded properly against the right cost codes and turn them in daily. At the end of the week, have the foreman also turn in the quantity of work completed for every task cost code. By Monday morning, have your job-cost engineer calculate the budget versus actual time spent against each cost code on every job. Then, on Monday, the project manager must review the weekly progress versus the budget and communicate the actual results with the superintendent and foreman. This process allows the field crew to be aware of their progress versus the budget and make any adjustments necessary.
4. Adjust your estimating cost history
The final step to keep the wheel of profit spinning is to review the final job cost after projects are completed to determine if the estimate and budget was accurate. Have the estimator meet with the project manager and field foreman or superintendent to review the final job costs versus the bid estimate. Look for reasons the final job costs were different from the budget and determine adjustments required to bid future projects accurately. Have the estimator make notes to keep track of why the job cost more or less than the original bid. Then, update the companywide estimating cost history library for future bids.
Keeping the profit wheel spinning takes a commitment to hold meetings, calculate your job costs every week and keep your field foreman informed. When you do what you need to do to develop accurate cost estimates, your profit margin will stop fading and you will start making more money.