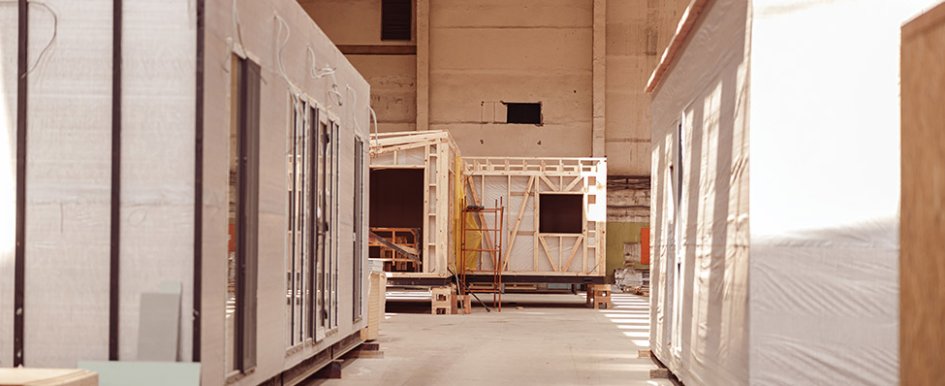
In the ever-changing landscape of the construction industry, efficiency, productivity and cost-effectiveness have become paramount. Traditional construction methods, though tried and tested, often fall short of meeting the increasingly stringent demands of owners and stakeholders. As we look to the future, these challenges, compounded by factors such as rising costs, sustainability concerns and a shortage of skilled labor, present both hurdles and opportunities for innovation.
As prefabrication emerges as a solution capable of addressing multiple challenges simultaneously, general contractors are key to its adoption.
By shifting construction activities from the jobsite to controlled factory settings, developers and contractors gain greater control over costs, project scheduling and risk mitigation. Prefabrication allows for parallel processing of multiple tasks, reducing overall building time by as much as 30% to 50%, according to Modular Building Institute. Moreover, the use of digital tools and advancements in logistics networks further enhance the quality and efficiency of prefabricated structures, aligning with the industry’s shift toward productization and supply chain integration.
The Road to Adoption
Prefabrication is not just a construction method — it’s a mindset. It requires embracing collaboration, innovation and a willingness to challenge the “but this is the way we’ve always done it” attitude.
Collaboration among multidisciplinary teams is fundamental to realizing its benefits, as it enables a safer jobsite, minimizes waste and drives efficiencies.
To fully embrace prefabrication, general contractors must take proactive steps to educate themselves and their teams before leading with a prefabricated approach.
- Designate an internal prefabrication champion or champions — Foster a culture that embraces prefabrication by understanding how it will benefit your business. Prefabrication requires a paradigm shift for project teams and developers, and integration into the project strategy from the outset. Early collaboration, design decisions and continuous iterative estimating aligned with target value design are essential for success.
- Develop a thorough understanding of available prefabrication options — Take the time to visit prefabricators and their offerings in your region. Understand product requirements and identify their best use cases. Determine when to involve manufacturers in the process, noting that prefabrication decisions are often made during the conceptual phase of a project. Ideally, off-site construction should be considered before a project is conceived. Additionally, understand the level of prefabrication your subcontractors offer that will help strengthen your prefabricated approach.
- Assess the current state of your projects — Create a past-project scorecard that compares initial project schedules and budgets to actual outcomes. Identify areas where prefabrication could have been utilized, and estimate the potential schedule and budget savings. Look for opportunities in areas with high repetition, such as facade systems, mechanical, electrical and plumbing (MEP) racks, boiler rooms, and structural and flooring systems.
- Plan for the future — Identify upcoming projects that can benefit from prefabrication using available products and systems. Evaluate whether your team is prepared to lead a prefabrication strategy for these projects. Achieving the full value of prefabrication requires early engagement and collaboration. Also, it is just as important to understand when prefabrication is not a good solution for a project — for instance, when a project is already in its conceptual design phase, lacks repeating elements or has complex architectural features.
When Prefabrication Makes Sense
Even though every project may not be suitable for prefabrication, it’s essential to adopt a systematic approach to evaluate each project and determine if prefabrication might be feasible. Equally important are the abilities to effectively communicate these reasons to developers and internal teams, and to offer suggestions that could potentially transform a project into a suitable candidate for prefabrication.
Prefabrication represents a shift for the construction industry, offering a pathway to greater efficiency, productivity and sustainability. General contractors can play a pivotal role in driving this transformation and, by embracing prefabrication, position themselves as leaders in an evolving landscape, delivering superior results and value to their clients.