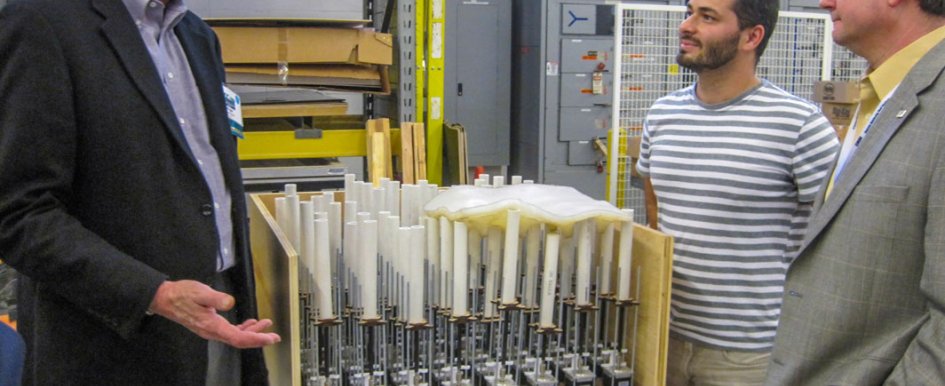
If the United States is to maintain its place in the world economy, it must increase its productivity and rate of innovation. Unfortunately, as one of the key sectors in the domestic economy, the construction industry has experienced nearly flat productivity growth for decades. The construction industry also has a significant impact on the environment. To address these issues, the industry must identify the strategic and technical barriers to productivity and adopt new technologies that both improve productivity and minimize concrete’s impact on the environment.
Some of the greatest results can be gained by focusing on the largest element of the construction sector—concrete construction—a sector comprised of multiple suppliers, producers and contractors. One of the best and most immediate ways may be through attendance of technology forums—regularly scheduled events that provide entrepreneurs with venues for showcasing solutions to construction challenges. Examples of productivity-enhancing tools considered at recent forums have included the following:
- Building information modeling (BIM) solutions have been developed by multiple software vendors. These systems allow designers and contractors to produce highly detailed datasets that provide virtual representations of a completed building. It is a logical move to coordinate the 3-D building models (developed using BIM tools) with the fourth dimension (time) to generate construction schedules. ALICE Technologies has created a parametric software solution that can generate thousands of viable scheduling options at the push of a button.
- High-precision, 3-D measurement and imaging using laser scanning has changed the way concrete is measured—and the application offerings in concrete construction are just beginning. FARO Technologies Inc. produces a 3-D measurement tool that is now used to detect high and low areas on fresh concrete floor surfaces, evaluate floor flatness after hardening and monitor structural performance in real time, under loads. These capabilities represent only a fraction of the potential functionality for the tool. For example, contractors can now document existing structures and prevent construction errors through comparison of as-built conditions with 3-D models, before adjoining elements are fabricated.
- For optimum resistance to cycles of freezing and thawing, concrete must have well-distributed, small voids that help to “vent” pressures developed as ice crystals form. For optimum efficiency, the voids should be evaluated before placement, rather than after the concrete has hardened. The Super Air Meter is a new meter that measures the air-void volume and spacing in fresh concrete—in minutes. This timely access to air-void data allows efficient adjustments to mixtures, thus increasing consistency and durability.
Sustainability Impacts
Heightened global awareness of the effects of carbon dioxide (CO2) emissions has presented a major challenge to the concrete industry. As worldwide urbanization continues, the demand for concrete is increasing and emissions from the associated production of cement rising.
Also, material supplies for concrete, including natural aggregates and manufactured byproducts, are experiencing regional shortages. Some of the related innovations discussed at industry forums have included:
Engineers have often looked to nature to assist with technology solutions. Blue Planet LLC has created a geomimetic concept to convert CO2 emissions from industrial plants, including coal and gas-fired power plants, steel mills and cement plants, into limestone aggregate with similar properties to natural limestone aggregate.
Many perceived environmental and supply chain issues related to cement and concrete can be solved by utilizing post-consumer glass waste. Building Products Ecosystem developed an initiative with the following goals:
- Reuse the recycled glass by processing it into a supplementary cementitious material (SCM), thus reducing the amount of Portland cement in concrete
- Localize the supply chain
- Fill supply shortages of fly ash and slag
This group is now evaluating pilot studies and working with industry-standard development organizations to assure performance.
Gaurav Sant, University of California Los Angeles, developed a unique approach to CO2 emission concerns by using CO2 as a resource. By capturing the CO2 gas and using it to create a new building material fabricated by 3-D printing technology, he and his research team are turning a problem into an opportunity. This highly innovative material has been produced at lab scale; researchers are seeking ways to scale up the production.
Waste CO2 from emissions can also be put to a beneficial use as an admixture in ready-mixed concrete by enhancing the reaction products that solidify the concrete. Carbon Cure Technologies has already scaled up this technology, which has been shown to improve concrete performance through several pilot projects.
Using alternative cementitious materials (ACMs) to replace Portland cement in some applications has the benefit of:
- Integrating recycled and waste materials
- Reducing energy consumption and emissions compared to Portland cement
- Improving concrete durability, sustainability and performance
ACMs, such as geopolymers, magnesium phosphate and calcium aluminate cement, are in various stages of development. While some are commercially available and have been used on many projects, others are still in development and need additional testing before implementation. The industry is supporting the development of a guide for using these materials effectively. Oceans Technology Group Inc. looks to the sea to improve on materials already used in concrete. An algae-based supplementary binder and additive for concrete works through exothermic reaction and formation of covalent bonds. It can provide advanced thermal properties, increased R-values, anti-corrosive attributes and mold and mildew control. Modified concrete mixtures bind well to other types of concrete, helping to reduce or eliminate cold joints.
Foundations for the Future
Innovation can positively affect the many challenges that face the concrete construction industry, including a decreasing workforce, sluggish productivity gains and increasing sustainability impacts. But to drive adoption, there is a need to establish confidence in any one technology. This may come from demonstrating performance in pilot studies, passing criteria of proven acceptance tests or revising long established design standard—all of which require investment of time and effort.
The typically risk-averse construction community needs a clear incentive to invest in an innovative concept. The industry can support new technologies by first evaluating and then jumpstarting integration into the concrete design and construction community. This may be through sponsoring or managing creation of new technical documents, such as guidelines, specifications and codes.
Other ways are to organize stakeholders for specific industry critical issues, to help establish a foothold in standards developing organizations, perform industry surveys, develop business cases, test models, develop courses and support research to fill that will provide confidence in the performance of the technology.