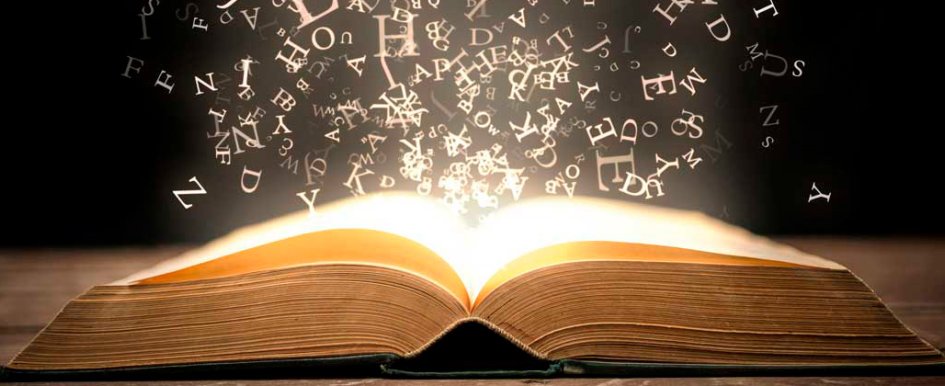
For centuries, construction firms of all makes and models have struggled with productivity. While other industries have benefitted from robotics, automation and other technological advancements, many studies indicate that the construction sector has suffered with no sizeable gain over the last 50 years.
Whether it is total quality management or lean, there are countless tools and avenues that enable firms to reduce waste and inefficiency. The greatest example of transformation and adoption of best practices comes in the form of safety management. Regardless of the situation, something provides a catalyst for firms to make a strategic decision to implement a safety-minded culture.
Firms must recognize that even if they appear to excel in labor management techniques, the real power begins with developing a culture of innovation and continuous improvement. The enemy of productivity and any companywide initiative is complacency. By maintaining a strategic plan that is always focused on improvement, a firm has the ability to eliminate the smallest imperfection or even tackle productivity. One of the main tenets of lean is the use of DMAIC:
- Define
- Measure
- Analyze
- Implement
- Control
Too often, firms jump to the implementation step, but fail to understand the root causes of their own inefficiencies first.
DMAIC is a system that helps thoroughly evaluate a firm’s deficiencies and create a solution that modifies the behavior.
The most important thing to consider for any firm is who will be the champion or change agent. The individual must have a mindset that balances the big picture vision of the firm and a thorough understanding of the ground level tactics.
One of the biggest mistakes of any initiative is creating tools and processes in a vacuum, without the buy-in of people who will use the tool. With the complete support of the organization’s leadership in place, the change can begin.
1. Define
Within this step, the team must develop a problem statement. There are many types of definitions that can be used:
- The firm’s labor productivity has continued to decline over the last 2 years.
- Material expenditures have overrun the budget on the last 25 projects.
- There is a communication breakdown between the office and the field.
It is important to ground the definition statement in fact. The statement must remain neutral. Be careful to avoid any false information or bias.
2. Measure
First, it is important to completely understand the true baseline. What is the magnitude of the problem? Several items to measure might include:
- Labor variance on completed jobs (estimated vs. actual) using the following parameters:
- Superintendents
- Managers
- Region
- Customer
- Contract delivery type
- Material variance on completed jobs
- Custom order
- Items routinely stocked
- Subcontractor variance on completed jobs
- Type of trade contractor
- Contract size
- Critical path vs. noncritical
The intent of this first measure is to gauge not only the magnitude, but to also identify potential smoking guns. It is also important to measure the processes as they exist in the firm. Some of the following processes would be ideal areas to examine to determine the efficacy:
- Material procurement processes
- Accounts receivable processes
- Any planning processes
- Project closeout processes
- Change order processes
Creating the “as-is” process is sometimes difficult because teams try to solve for areas too quickly. This is not to say areas shouldn’t be flagged, but dialing in too quickly on one, specific inefficiency may mask the larger, more complicated problem.
3. Analyze
It is also important to note that firms often put their best people on the most challenging projects. Furthermore, it is also important to reference back to the aforementioned processes. Ask the following important questions in the analysis:
- Is there redundancy in the processes?
- Where is there little connectivity between critical departments?
- What steps would provide the most value to the field?
- What key steps should be measured in the future?
- What is the frequency of the missteps?
4. Implement
Improve is often the preferred terminology, but implement invokes some sort of change that is required in the new order of things. Three important items to recall are:
- Process—There must be a flow chart or value-stream map for each process. Simply put, you cannot measure something if no standard process exists.
- Standard tools—Whether it is a log, agenda, spreadsheet, purchase order or a planning device, there must be consistency in the tools.
- Accountability—Success lies in a firm’s ability to measure and provide true process adherence accountability.
Implementation takes time and patience. With the as-is process from the measure step, the firm can now create a standard toolset. However, implementation is best achieved through the use of beta subjects and pilot projects. Put another way, the firm should avoid a mass rollout on something that may not be ready. The key is to work out bugs early in the process, as well as gain some additional buy-in on how the process was successful.
5. Control
With the new system in place and the organization trained, it is now important to turn on the scoreboard. The firm should measure the behaviors it expects its team to utilize. For instance, if a firm begins 10 projects in the first month of rollout, there should be 10 preconstruction strategy meetings. More importantly, the scoreboard should be present to illustrate this example of upstream behavior. The firm should determine several metrics that will most influence the overarching initiative.
At the end of the day, firms must understand that it takes a strategic mindset to become more efficient. DMAIC is a model that helps firms not only identify the true source of the inefficiencies, but also create a sustainable system to drive long-term change. Firms that are lean are focused not only on productivity, but also continuous improvement.