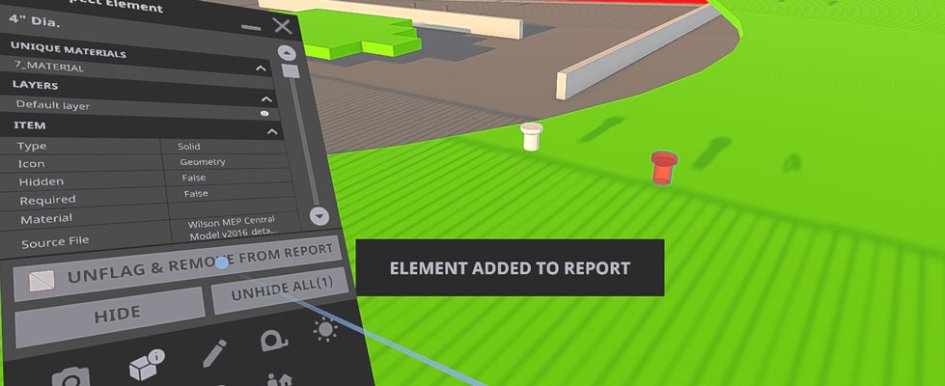
When evaluating any new technology, there are many questions one can ask. Is this something my company will benefit from? Will it help me save or make money? Will my team actually use it? With technology that is seen as new or emerging, these questions are even more important, as the implementation can be somewhat divisive. Some users may see it as too disruptive or may not understand how to use it. However, once users understand how the new tools can solve a problem or increase knowledge, they will begin to rely on it. Virtual reality (VR) adoption follows the same pattern. The process of working through the tools and seeing if the cost-to-benefit ratio is advantageous for the firm follows a few typical steps.
What Is VR?
VR involves the wearing of a headset that replaces the world around the user with a simulated, virtual one. Depending on the type of simulation, there can be interactivity, navigation, design and other activities. From an investment standpoint, VR is fairly well-developed, accessible and cost effective.
Why Do I Need It?
Most VR usage occurs in-house within a controlled environment. This brings with it several use cases and benefits. For example, companies often use VR to provide training simulations for employees, which presents opportunities for benefits and cost savings. For jobs where time is an issue, you can train an operator for a position before the jobsite or equipment is ready. This can increase a project’s safety record because it allows for costly learning mistakes to be made in a virtual world, not on the actual jobsite.
Take the Lincoln Electric VRTEX simulator, for example—a VR welding mask that provides the user with instant feedback on their progress, enabling them to understand and correct mistakes early on in the project process.
According to Lincoln Electric, data collected from training sessions with the simulator showed that construction companies who utilized VR technology in their onboarding processes certified individuals faster, reduced training costs and achieved better results than those companies who used more traditional training methods.
The second use-case can be found in the coordination and project review processes. As architecture, engineering, construction and owner (AECO) software has moved towards building information modeling (BIM), increasingly more 3D content is being used in project coordination. VR can help coordinate the installation and sequencing of trades, giving the field team a greater understanding of how all of the built pieces will work together.
With that said, looking at projects on a screen or a small model is different than being able to see or interact with it at full scale. Navigating a project in VR can lead to a better understanding of how elements in a project fit together. For instance, when someone is using VR and interacting with a small space, they may realize that there is not enough room to install components or work on equipment. Five Star Electric, for example, has said that working with 3D in this way made things “actually tangible.”
Navigating and viewing the project is just the tip of the iceberg, though, as the tools used for this kind of model review have progressed quite a bit since the early days of VR. The tools that focus on coordination enable a team to walk through and mark up spaces to address issues and track problem areas. Some solutions even allow you to dictate notes by speaking. When working with BIM or intelligent models, the data included in those elements is available in VR for review, and measurements can be taken by simply pointing at elements.
One of the more recent VR applications is multiuser coordination meetings. This allows users from multiple locations to all be present in the same model, at the same time, virtually, walking through and reviewing it together. Virtual site visits by owners, stakeholders, designers and clients lead to better team cohesion.
How Do I Choose a Solution?
When it comes to pulling the trigger on VR, it helps to first identify your team’s desired outcomes, which will drive a more accurate budget estimate and can be broken down into three parts: hardware, software and content.
Hardware includes the headset and the computer. The choice of what hardware to purchase usually comes down to how you want to experience VR. For example, if you do not want to be tethered to a computer, you may choose a headset based on its mobility. But there is a trade-off for the freedom and ease of setup—mobile technology is not as powerful as computer-based equipment. As such, large projects may need to be broken up, limiting your software choices.
The headsets that require a computer connection need a cable or an expensive add-on, as well as a computer that is powerful enough to drive the VR headset. These also come with more useful software options and features.
Each company has its own computer hardware requirements and testing routines to determine whether their system is compatible with VR. If new hardware is required, the budget will likely increase from several hundred to even thousands of dollars. In addition to hardware, purpose generally drives the decision on the software. For construction and collaboration, that purpose is to offer more hands-on review and functionality, through tools such as IrisVR, InsightVR and Revizto.
While many firms, including Gilbane Building Company, have had great success with IrisVR, each program has functionality that enables users to easily bring their models into VR, review progress and identify issues that need the attention of others. They can also work outside of VR if one partner does not yet have the hardware. Pricing on these tools is generally by subscription, with plans based on the required features.
An often-overlooked aspect of VR is the content. If your projects currently only have 2D documentation, VR will not be much help. If you are already using the BIM process for virtual design and construction (VDC) coordination, VR is the logical next step to maximize your investment in preconstruction design and coordination efforts. In some cases, when budget allows, you can translate 2D documentation into 3D to provide a better workflow for your team.
What Would My Investment Be?
Investing in VR is certainly worth it. Many companies in the construction space have benefitted and used it to help win project bids, better coordinate meetings and improve overall building operations. The advancements in VR technology and a wide range of equipment options and software pricing make it accessible today.
Years ago, when BIM was just being adopted, one company was working on a project where, as part of each day’s process, views of mechanical systems would be printed and posted on the wall for the coordination team to reference. Some of the contractors on the team would laugh at the need for 3D models, with the typical refrain being that they have always gotten the job done with 2D.
One day, however, they came in to get clarification on a system installation, looked at the wall, and saw exactly what they were trying to understand. After that, they came in every day to review the model. VR is just like that—you may not realize just how much you need it until you have tried it.
Some might say the price tag on VR tools is still too high, but it really isn’t when compared to the cost of a change order or problem on a project, which clients have said can run up to $5,000. If VR can help mitigate and catch one issue early, it goes beyond paying for itself.