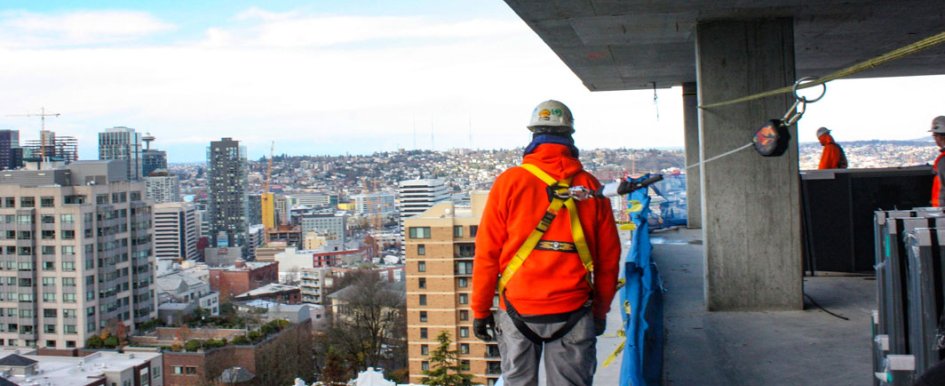
One of the most challenging aspects of building a robust fall-protection solution is installing enough anchorage tie-off points to provide sufficient access to all required work areas. Further complicating matters is the fact that, as work progresses, available structural members are covered or can otherwise become unavailable. Horizontal lifeline (HLL) systems can offer safety professionals the necessary flexibility to create a fall-protection solution during tricky periods of transition on the jobsite.
Horizontal Lifelines
HLL systems are composed of two endpoint anchors connected by a varying length of rope or cable to which workers attach a fixed-length or self-retracting lanyard, allowing a high degree of mobility across the jobsite. Compared to a single-point tie-off anchor, HLLs permit workers to access a large area without the need to detach or reattach their lanyard, which helps maintain compliance with the all-important 100% tie-off requirement when working at height.
The most practical way to think about an HLL is as an extended anchor point. Although technically the HLL’s endpoint anchors remain in a fixed location, connecting those anchor points with a compatible rope or cable HLL system, in essence, distributes the anchor’s strength along the rope or cable.
This provides a safe tie-off point along its length. All HLLs have energy absorption capabilities to shed forces generated in the event of a fall; however, the actual method of absorbing fall energy may differ. The three main types of energy absorption are deforming post/stanchion, external energy absorber and deflection of the line itself.
Deforming post/stanchion systems utilize a steel cable connected between end posts, often with intermediate posts between the end posts, creating “bays” of cable to which workers connect. In the event of a fall, the forces generated by the falling worker travel through the cable lifeline and into the end posts. These posts deform as the forces increase, thereby shedding fall energy and reducing the forces felt by the worker. These types of systems are often found on structural beams or in poured bridgework applications.
External energy absorber systems may be of low-stretch rope or steel cable and include one or more energy absorbers made of steel or rip-stitch nylon. In the event of a fall, the HLL’s attachment points do not deform. Rather, the metal or nylon energy absorber tears, shedding energy that would otherwise be transmitted to the worker.
HLL systems that rely on the deflection of the lifeline itself have neither deforming posts nor external energy absorbers. Like an external energy absorber HLL, these systems utilize nondeforming anchor points. But in in the event of a fall, the rope itself stretches, absorbing fall energy, as opposed to depleting force via an external energy absorber. The rope used in these systems is typically suppler than that used in external energy absorber systems.
Anchor Independence
Excepting the deforming post/stanchion HLL systems, a major advantage of an HLL is the fact that it is largely anchor independent making it flexible enough for nearly any jobsite at any stage of work. For example, it is perfectly acceptable to connect an HLL to an anchor bolted to a concrete wall on one end, and a beam clamp or cinch-style anchor on the other.
Although the likelihood is that both anchors will be of the same type, the point is they do not have to be. And, given the variable lengths of HLL systems, this flexibility can permit an HLL to reach an anchor that may otherwise be out of consideration—an angled I-beam or rebar stack at the edge of the work area, for example. But remember: Always adhere to manufacturer’s guidelines.
Increased Worker Capacity
HLLs can vary in total worker capacity, which is the number of workers that can be connected to the system, depending on whether the application is a fall arrest (where the potential exists for the worker from accessing an edge) or fall restraint (no potential exists for the worker to access an edge). HLL capacities vary by manufacturer, but a common HLL capacity is two workers in fall arrest and four workers in fall restraint.
For the two workers in fall arrest scenario, it might not seem like a worker/anchor advantage since there is still technically one worker for every installed anchor, but the fact is that the workers could potentially access up to 100 linear feet along the HLL, as well as the additional area allowed by their connector stretching perpendicular from the HLL, all without having to transition between anchors. In fall restraint, on approved HLL systems, the number of workers increases to four, doubling worker capacity on the same two-anchor system.
Quick & Easy Deployment
For all their flexibility and effectiveness in preventing falls and keeping workers safe at height, it might seem HLLs are complex systems with lots of moving parts, complicated installation procedures or the need for special engineering—not so.
While there are certain applications that may require special engineering (generally due to substrate restrictions), the vast majority of HLL systems are easily installed by the user because they are pre-engineered, taking much of the work out of designing a system.
Select an HLL-compatible anchor for your substrate; choose the cable or rope HLL system that best suits your application; and install per the supplied instructions—no engineer required. Most cable HLL systems require some simple assembly using familiar components like wire thimbles, fist-grips, shackles and turnbuckles; whereas, most rope systems come fully assembled and include a built-in, self-adjusting tensioner and carabiners for connecting to the anchors.
Permanent Solutions
HLLs are also an excellent solution for providing a safe tie-off point to workers who need access to potentially dangerous areas after the job is done. Just because the building is complete doesn’t mean the work stops. For the entire life of the building, maintenance staff, inspectors and other contractors will need to tread where the last workers did when they topped it off.
How do you help keep them safe? An effective solution is to install a permanent HLL designed to give 100% tie-off protection from the point the worker accesses the roof to wherever their work may take them. Common designs not only have HLLs around the perimeter of a roof, they also include single-leg spurs that allow ready access to heating, ventilation and air-conditioning (HVAC) units, load decks, elevator equipment, and any other system that may need routine maintenance.
Whether it’s a work in progress or a finished architectural masterpiece, when designing a fall-protection system, safety professionals should always consider HLLs a serious contender. In both temporary and permanent applications, they punch well above their weight.