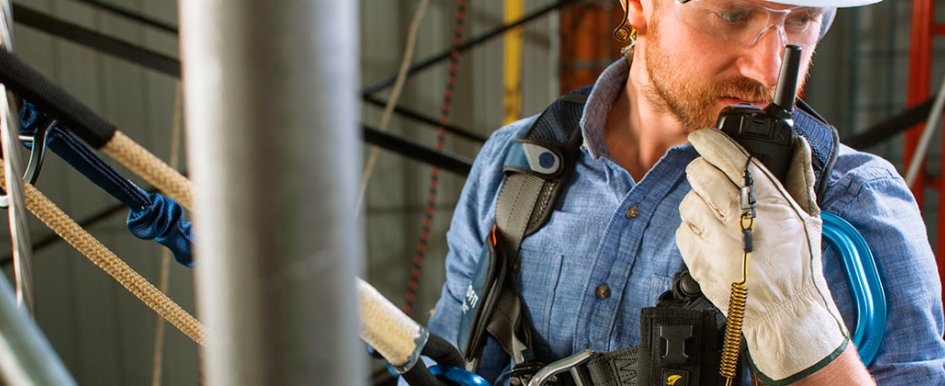
According to the Bureau of Labor Statistics, there are more than 50,000 "struck by falling object" OSHA recordables every year in the United States. That is one injury caused by a dropped object every 10 minutes. But how many dropped object accidents go unrecorded? With the number of objects dropped, it's amazing how few people are getting hurt. Although awareness of the dropped object threat has existed for as long as objects and tools have been used at height, reports of near misses and injuries have recently become even more prevalent.
Despite these statistics—and the fact that many of these accidents could have been prevented with the proper safety gear—many contractors do not take the necessary precautions to prevent fall-related injuries by providing workers with personal fall protection systems for both themselves and for their tools.
This discussion should not be about catching the object that falls from a height or limiting the damage a falling object can do by wearing a hardhat or other personal protective equipment (PPE). It is about preventing the object from ever falling in the first place. Why? Because most people have no idea how much force something like a falling hammer generates, even when dropped from a moderate height. Most people don't have a cursory understanding of forces caused by an object hitting and deflecting off something during the drop. Simply put, most workers underestimate the dangers of dropped objects.
The Consequences of Dropped Objects
It's easy for anyone to comprehend the dangers of people falling from height, but the consequences of dropped objects are less straightforward. As a result, additional education at all levels is necessary to keep your jobsite free from incident.
For example, a 3-pound tool falling from 200 feet strikes the earth with 1,062 pounds per square inch of force. But what does that mean? It means that hardhats and drop zones are of little consequence when an object carrying this kind of energy makes a direct impact or deflects off of another object before it hits the ground.
Apply this physics lesson to a real-world application. There is a video online in which workers in Rio de Janeiro are doing repair work on the 125-foot-high Christ the Redeemer statue after it was struck by lightning. In the video, the workers are tied off above a crowd of people, but are using a hammer and chisel that are not secured. One of the workers answers a call from his son on his cellphone, which is also not secured. What if that hammer, chisel or cellphone had fallen from the top of the statue into the crowd of people below? To determine what kind of force an object falling from heights can generate, calculations can be done around the physics of gravity.
For example, an 8-pound wrench dropped from 200 feet would hit with a force of 2,833 pounds per square inch. That is the equivalent of a small car hitting a 1-square-inch area. So, if that worker had dropped an object and it had hit a visitor below, it would have likely caused a severe injury, if not a fatality.
In another example, in New Jersey, a man delivering sheet rock was killed by a dropped tape measure on a construction site. The victim, an independent contractor for a trucking company, was leaning into a car window to speak with someone and when he pulled his head out, he was struck by a tape measure that was dropped by a worker from 50 stories above. The 1-pound tape measure ricocheted off construction equipment about 10 feet above the ground and hit the trucker on the side of the head. Although he was not wearing a hardhat, it is not clear whether that would have saved him, given that the object deflected off a piece of equipment near the ground before striking him.
Raising Awareness of Dropped Object Prevention
Dropped object prevention hasn't yet attained the status of fall protection because there is a lack of awareness of how important it is and how to prevent dropped objects. Twenty-five years ago, the thought of wearing a seat belt was absurd to many people. Now most people buckle up as a matter of course. This change in behavior didn't happen overnight, though. Implementing a drop prevention program for tools is a significant paradigm shift, challenged by a lack of awareness, resistance to change and a drive toward increased productivity.
At this moment in time, there is simply an expectation that objects will fall. It is expected of workers at height to wear a fall protection harness and be tied off, but it is not expected that tools be secured. This needs to change.
Too frequently, workers rely on debris nets, toe boards and PPE to catch falling objects or to limit the damage they do. But they need to prevent them from falling in the first place. According to OSHA, there are more than 52,260 recorded incidents of people being struck by falling objects in the last recording period. The actual number of incidents is likely much higher. But this would mean that, on average, there are at least 143 "struck by falling object" OSHA recordables every day in the U.S. alone.
"But it's hard to tie off tools because they aren't designed for that," some might say. People are not designed to work at height either. They don"t have a natural \'93connection point\'94 from which to secure themselves. That's why they wear a fall protection harness: to provide that connection point. Tools also need a fall protection device or a connection point, so they can be tied off.
Another point to make is that a fall protection harness on a person acts as the body support component of a primary, personal fall protection system to keep workers at height safe. However, if that fall protection system fails, there usually isn't a secondary backup system, such as a net. By contrast, we typically rely on the secondary systems, such as debris nets, toe boards or PPE, when it comes to fall protection for tools and equipment. However, we rarely deploy a primary system.
This underscores a problem the industry currently faces when it comes to fall protection for both people and tools. There are primary systems in place for people, but not tools, and secondary systems in place for tools, but not people. So essentially, there are no backup systems in place for personal fall arrest systems that fail and no active systems in place for tools that fall. Similarly, most organizations have deployed a fall protection program for workers, but have not deployed a drop prevention program for tools and equipment.
Incorporating Tools & Equipment into a Fall Protection Program
Expanding their fall protection program to include tools and equipment is far easier for companies and employees to ingest than creating a new program for drop prevention. The difference between a fall protection program for humans and a fall protection program for tools is only a matter of perspective. One is designed to save you; the other is designed to save others. No worker wants to fall to his death. Similarly, no one wants to be the worker in New Jersey who dropped the tape measure that hit and killed a man working below (and no crew or company wants to be associated with an incident like that).
While the most obvious person at risk when objects are dropped is the one underneath the falling object, the person using the tool can also be at risk, as his knee-jerk reaction may be to reach for and try to catch the falling object, which could cause him to lose his balance and end up falling.
Implementing Drop Protection for Tools
When a company designs a climbing harness, the human body and its variations are thoroughly considered. However, most people have essentially the same body structure. On the other hand, tools have so many different shapes, features and functions that there cannot be a \'93one size fits all\'94 drop prevention attachment point for tools (like a standard d-ring for a harness).
A robust drop protection program for tools should include significant considerations for tool design, form, fit and function, along with rigorous drop testing of attachment points prior to use in the field. Also, many drop-prevention devices inhibit tool function and therefore affect job performance. If attachment points are obstructive and impact productivity, workers may discard them. This is why it is imperative to choose safe, productive, user-friendly systems.
Turnkey toolkits, in which each tool has a lanyard attachment point, provide a solid foundation for any program. But custom solutions can also be developed for specific job functions. As companies explore opportunities, tooling professionals can be a significant source of knowledge through sharing methods and successful systems developed for other markets.
Who is Responsible for Solving the Problem?
Dropped objects are a real safety and productivity concern in the construction industry. In fact, according to the U.S. Department of Labor\'92s Bureau of Labor Statistics, the third cause of death in the workplace, behind transportation incidents and workplace violence, is "contact with objects and equipment."
The majority of those incidents appear to belong to the line item "struck by a falling object." The fourth leading cause of death in the workplace is falls. Falls actually used to be the third largest cause of death. However, with increased use of fall protection equipment by workers, the death rate for humans falling from heights is dropping.
Recognizing the danger as an issue requiring serious consideration is a great first step. Serious consideration of the concept of a complete and reliable solution for fall protection that encompasses both humans and objects will go a long way toward establishing a sustainable safety program. Too often, companies only invest in worker safety after a tragic event occurs.
Although most companies now recognize the hazards of working at height, the next step is to realize that fall protection—for both people and jobsite tools and equipment—must be addressed before an incident instead of after in order to improve the personal safety of workers while working at height and wherever they may be on the jobsite.