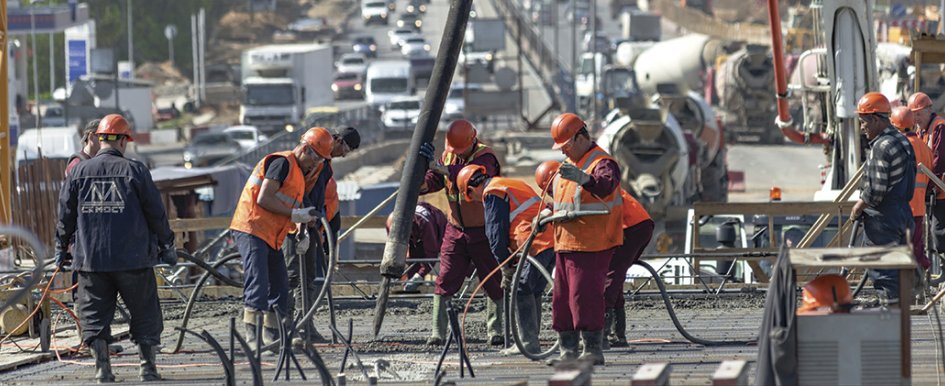
It was 1 a.m. on a night several years ago when a client called with horrific news. The contractor said, "There's been an accident; two of our workers are dead." He explained that a motorist had driven into the work zone, striking and killing two employees. The practical steps necessary for the investigation were reviewed, as were the steps to notify the victims' families and OSHA. Finally, his insurance broker would mobilize its claims, safety and risk management personnel to assist after these men prematurely lost their lives.
While work zone fatalities declined 47 percent between 2003 and 2013, it's still no secret that highway and road contractors have risky jobs. Anyone with highway construction experience has stories of near-misses and tragedies in work zones that they have either heard about or witnessed themselves. While highway and road workers face multiple hazards, they are not the only parties exposed to work zone hazards. Motorists, bicyclists and pedestrians are often victims of work zone accidents, regardless of who is at fault.
According to the Fatality Analysis Reporting System (FARS), which is maintained by the National Highway Traffic Safety Administration (NHTSA), 579 fatal motor vehicle crashes occurred in U.S. work zones in 2013—or one work zone fatality every 15 hours. Texas, California and Florida were the three most fatal states—comprising 39 percent of the country's total work zone fatalities in 2013. An additional 105 fatal occupational work zone injuries occurred at road jobsites in 2013.
Beware of Motorists
When it comes to work zone accidents caused by or involving motorists, investigations have shown a set of common contributing factors:
- The motorist didn't notice a work zone
- The motorist didn't know what to do
- The motorist didn't know where to go
- The motorist didn't have time to react
- There was a worker or equipment in the traffic lane
Adhering to a set of standard best practices can reduce risk, minimize hazards and afford greater control over contractors' wellbeing—and the wellbeing of everyone on the road.
Remember F.A.D.S.
Flow: Affect the flow of traffic as little as is practicable
Attention: Get the attention of the motorists quickly and effectively
Direction: Provide clear direction to the motorists to guide them through and around the work zone
Separation: Whenever possible, separate hard (vehicles and equipment) from soft (personnel) using barriers or road way closures
Also consider the following rules:
- Make work zone safety central to every project.Regardless of project scope and scale, all workers must be highly visible at all times while in work zones. High-visibility garments should meet the most current American National Standards Institute (ANSI) and International Safety Equipment Association (ISEA) standards. Work zone lighting should be staged to illuminate the work area without blinding approaching traffic or motorists adjacent to the work area. Equipment and vehicles should be equipped with strobe lighting that makes them instantly visible to other workers, operators and motorists.
- Plan work zones with drivers in mind.Plan work zones with the understanding that drivers will only reduce speeds if they clearly see a need to do so immediately. When work zone signage is left uncovered during inactive work periods, motorists may be inclined to ignore cautionary signage.
- Use traffic control methods that are clear, predictable and consistent.Work zones with an overabundance of signage or odd layouts that cannot be navigated without difficulty will only add to the inherent risks of work zones.
- Avoid frequent and sudden changes in work zone layout.Traffic that is flowing smoothly is generally considered to pose less of a risk than traffic that is forced into sudden lane changes.
- Use only clean and well-maintained channelizing devices.Plaintiff attorneys maintain that they can gain a significant advantage against a defendant simply by showing the channelizing devices used in the work zone at the time of an incident. Devices that are poorly maintained are less visible to motorists and hamper the ability to establish authority in a work zone, and they diminish company image.
- Use concrete barriers or road closures to separate workers and motorists.Using concrete barriers to separate workers and traffic can significantly reduce risk and allow workers to focus on activities.
Protect Workers
While the above rules serve to reduce the risks of an unfavorable motorist and road worker interaction, what about the hazards to road workers from construction equipment, vehicles and activities within the work zone? In this case, planning should include ensuring that work zone personnel are familiar with and in compliance with applicable safety requirements. Additional best practices include:
- Ensure all vehicles and mobile equipment operating within work zones are equipped with back-up/travel alarms that are distinguishable above the surrounding noise.
- Ensure cab glass on all vehicles and mobile equipment is well-maintained and free from damage.
- Ensure that occupants of vehicles and mobile equipment (equipped with Roll Over Protection Structures) wear seatbelts, regardless of terrain.
- Train workers on-foot to recognize vehicle and mobile equipment blind spots and to make eye contact and communicate with operators before entering such areas.
- Equip equipment with cameras that cover critical blind spots.
- Use work zone intrusion alarms to give workers immediate warning.
- Position crash trucks and vehicles to optimize worker protection.
- Use traffic control devices that meet National Cooperative Highway Research Program (NCHRP) Report 350 criteria.
Mind the Mod Factor
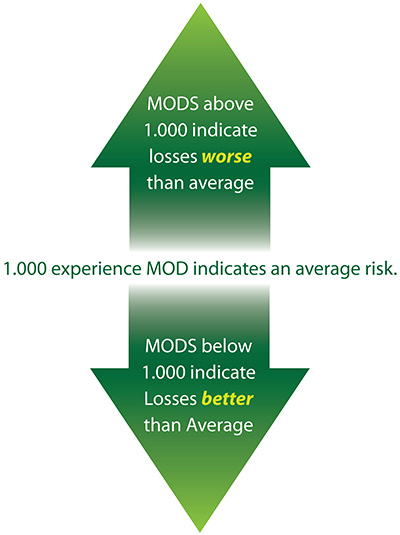
Without a reliable and steady workforce, production can slow, causing increased project costs. A potentially greater cost can be the long-term increase to insurance premiums. Employee injuries impact a company's experience modification factor for three years and will stay in the insurance company's loss experience used to underwrite the account for a minimum of five years. This has a direct impact on workers' compensation costs, but also a rising experience modification factor could limit the ability to bid work if it is above a 1.0. Such claims involve significant costs and impact the company's general liability and possibly umbrella liability for at least five years.
Another insurance matter to consider is an effective contractual risk transfer strategy requiring additional insured coverage and indemnification from subcontractors to shift liability away from a company in the event that something happens in a work zone. Also, partner with insurance and risk management professionals who are qualified to respond 24/7 to emergency accident situations.
The power of safety is in prevention, not repair. Take action now to reduce risks, save lives and preserve the financial wellbeing of contractors.