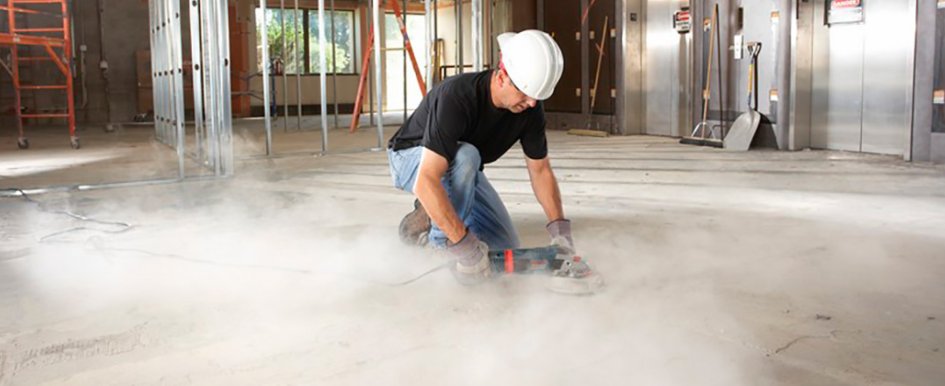
When the United States Department of Labor (DOL) issued its ruling aimed at better protecting workers from respirable silica dust, few industry veterans were surprised. The new rule is currently in effect and substantially reduces the permissible exposure limits (PEL) for workers in the construction industry. The DOL’s Occupational Safety and Health Administration (OSHA) will enforce a reduction in the amount of silica that workers can be exposed to over an 8-hour day from 250 micrograms per cubic meter of air to 50 micrograms (OSHA rule 1926.1153 Table 1, available for review at http://bit.ly/2ovGM8X). The original enforcement date was June 23, 2017, but OSHA recently announced it will delay enforcement until September 23, 2017.
What It Means
Silica, often referred to as quartz, is found in many materials that are common on construction sites. Crystalline silica is a component of concrete that becomes breathable when drilling, sawing, polishing, cutting or crushing concrete, brick, block, rock or stone. These dust particles are invisible to the naked eye, but can cause serious health hazards. Each exposure to silica can add to lung damage unless the worker is using appropriate protection to avoid the exposure.
OSHA claims that respirable crystalline silica is capable of crippling or killing workers by causing a range of lung diseases, from silicosis and lung cancer to emphysema and kidney disease. In addition, silica exposure has been linked to other illnesses, including renal disease and other cancers. According to OSHA, it is estimated that 2.3 million U.S. workers are exposed to respirable silica dust at work each year.
The new standard establishes a PEL to limit employee exposure to respirable silica. The new PEL for silica exposure is 50 micrograms per cubic meter (µg/m3) of air (8-hour weighted average). A micron is about the size of a particle of fine, milled flour, so 50 microns fused together is about the size of a grain of salt. The daily PEL is approximately the equivalent of a grain of salt.
Working Toward Compliance
There are several methods to achieving effective silica dust management. One is water flow controls, which can be employed in stone cutting and milling, brick and block cutting and stone engraving. Water spray systems are often seen on crushers, material recycling systems, conveyors, gravel operations and in some demolition work. But not every application can be addressed by adding a water component.
In most instances, jobsite dust control demands that air flow be managed. In the best-case scenario, there would be no dust present in work environments. The optimum way to control respirable crystalline silica dust is to remove it as it is created.
OSHA’s Table 1 (OSHA 1926.1153 Table 1, available for review at http://bit.ly/2ovGM8X) matches common construction tasks with effective dust-control methods for those tasks. The table has three columns; the task or equipment being used, a column describing the method for controlling dust and a third column stating whether respiratory protection is needed when performing the task.
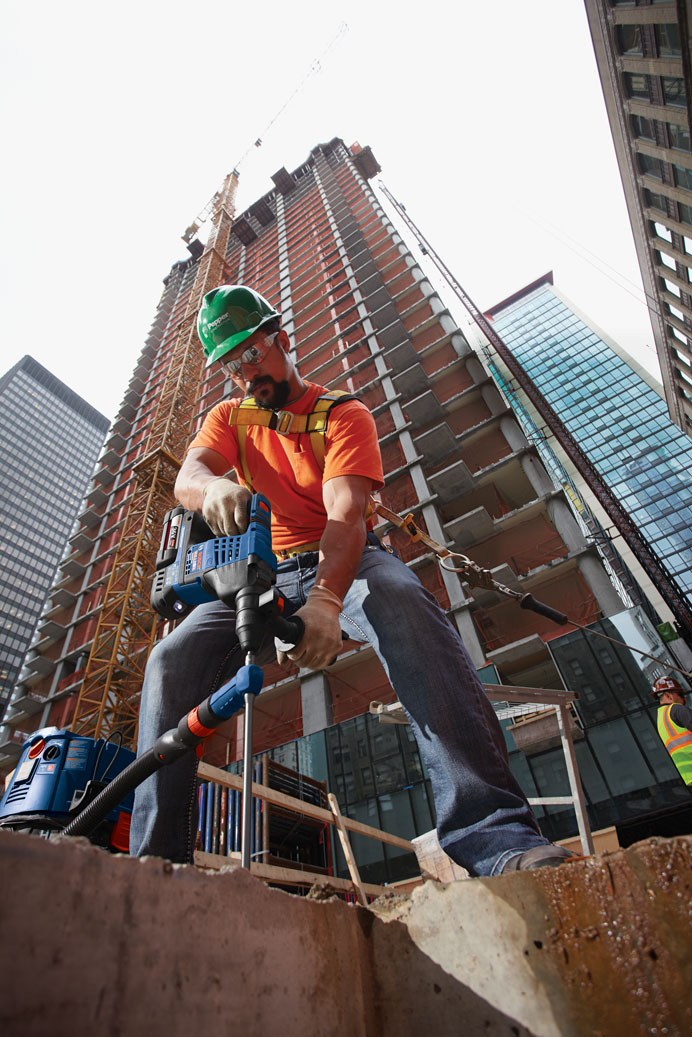
By finding the work activity on Table 1, users can quickly see what steps are required to ensure proper dust management. In order to move toward compliance and protection, it is critical that every component in a power tool system be designed to effectively remove dust. Here are some guidelines:
- Choose the tool that best fits your needs—Dust-collection systems are available for all power tools that are used with concrete, including grinders, tuck pointers, hammer drills, rotary hammers and demolition hammers.
- Identify the correct attachment that fits your tool—Look for dust-collection attachments that are engineered to provide maximum performance while preserving the full functionality of the tool.
- Choose a HEPA-rated (high efficiency particulate air) dust extractor with the highest cubic feet per minute (cfm) that meets EPA guidelines—A professional dust extractor can be rated at 150 cfm with HEPA filtration. Less powerful vacuums provide much lower airflow that is further decreased when a HEPA filter is placed in it. All dust extractors need to have automatic or semi-automatic filter cleaning.
- Determine the respirator for the application—Respirators protect workers by filtering contaminants. If needed for the application being performed, respirator options include particulate respirators that filter out airborne particles and air-purifying respirators with cartridges/canisters that filter out chemicals and gases.
A key focus is on the vacuum system (dust extractor) and specific tool attachments. These components can capture dust as the tool creates it. Look for automatic filter cleaning in the dust extractor, which does just that—every 15 seconds—to ensure maximum suction power. High-suction airflow delivers excellent dust extraction.
Additional Considerations
Another component in concrete drilling that can reduce airborne silica dust is the drill bit. For example, one power tool manufacturer’s bits are built around an internal dust channel that is milled to deliver dust reduction in a lightweight concrete bit. The manufacturer worked with an engineering consulting firm to perform industry-standard tests for airborne dust and silica exposure in concrete drilling to test the dust collection effectiveness of the bits.
The tests, performed by a certified, industrial hygienist, compare airborne dust concentrations in the personal breathing zone of a worker using the bits versus conventional solid-core bits. Four tests were conducted, and in each test, the hollow-core bit rendered undetectable amounts of silica dust. For conventional concrete drill bits, silica dust was detected in all four tests.
A well-thought-out, silica dust-management plan takes into consideration the nature of the work being done. Training is important to ensure that workers understand silica risks and how to limit exposures. It is important to establish and implement a written exposure control plan to formally identify tasks that involve exposure and the methods recommended to protect workers, including procedures to restrict access to work areas where high exposures may occur.