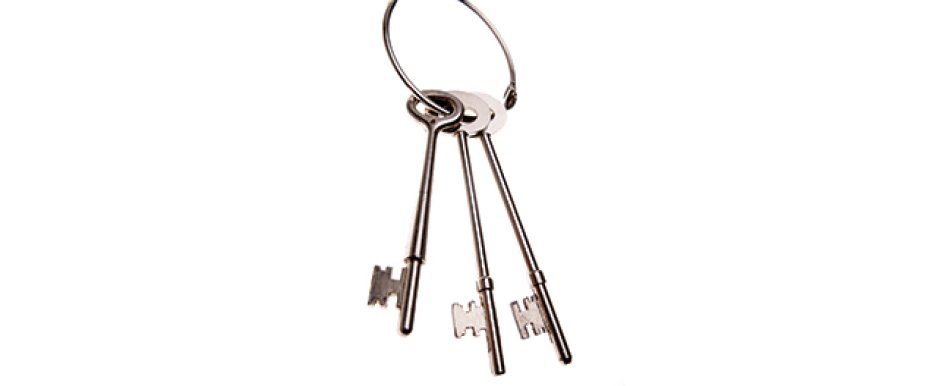
Your phone rings, and it’s a call you were not anticipating. About five years ago, you were the general contractor for a new multi-tenanted building, and now the building owner has called to inform you that the facility is facing issues with water intrusion. You have officially been put on notice, and your company is being sued for damages and repairs.
Construction defect involves the premature failure of any building component or system, which is usually the result of improper installation, improper design, product failure or improper material selection, use and subsequent failure. One of the more frequent types of construction defect claims is water intrusion, which can occur from roof leaks, windows, exterior siding/cladding systems and balconies. Other claims can come from soil issues or deterioration of pipes, plumbing or other building materials.
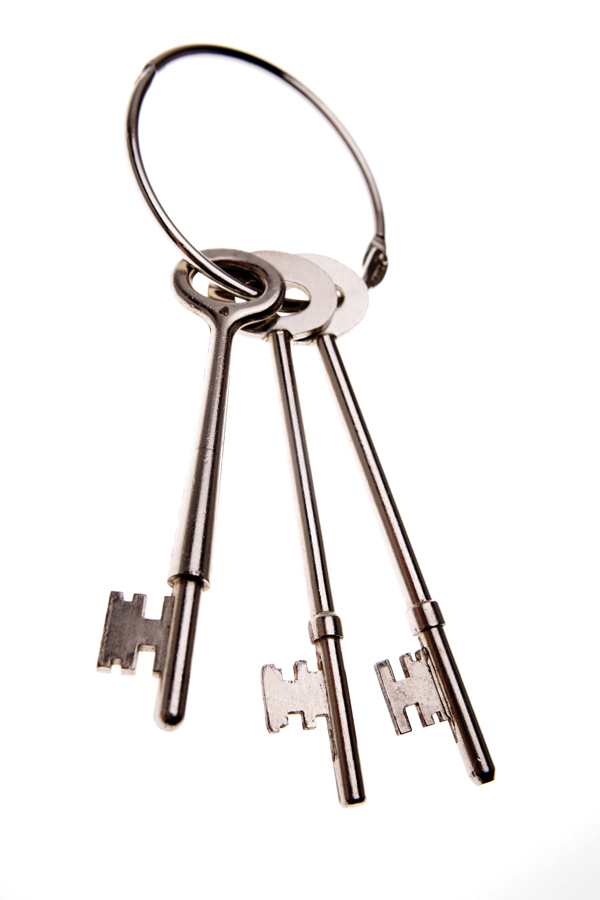
Construction defect allegations are different from other insurance claims because, in most cases, they take years to materialize and often longer to defend. Three key steps can help you protect yourself from this situation, including developing and implementing a quality assurance/quality control program (QA/QC), creating a strict document retention plan and quickly reporting claims.
A QA/QC program is a systematic approach to help ensure that a project is built correctly and performs as designed. The complexity of the program is related to the complexity of the job, and contractors should have a plan for each unique project. The core of the program may contain, at a minimum, the following elements.
- Management responsibility—Management should fully support the program for it to be truly effective. Leadership should internally assign responsibilities, including verifying construction drawings and specifications to ensure they are current, and provide adequate training.
- Material selection—Contractors must make sure material, equipment and services comply with design specifications, building code requirements and compatibility of products. Inspect material on delivery, and store it properly. As an example, several years after a contractor installed mechanical hangers in a corrosive environment, the hangers failed, causing the mechanical system it supported to collapse. The design called for a specific grade of steel due to the corrosive environment. It was determined that the contractor supplied and installed the wrong grade of steel, which lead to the failure.
- Subcontractor management—Always prequalify your subcontractors to ensure they are qualified to do the work. Develop qualification requirements, and verify subs are financially stable. Request a copy of their QA/QC program, and make sure it aligns with your own. Lastly, never hire a subcontractor without having a contract in place that includes applicable state-specific indemnification language and insurance requirements. Review your contract after receipt, making sure that no language has been crossed out and that it has been signed and dated.
- Workmanship—Follow the manufacturer’s installation instructions. Review any plans, specifications or material prior to installation or use. If you know something is wrong, do not proceed. Create a written notice to the architect, planner and owner, and keep a copy. Provide any necessary training to employees, and seek certifications for installation when possible. When construction drawings lack detail, contractors should seek clarification or direction from the designer and document this correspondence.
- Inspection—Anything that is installed should be inspected. Empower all employees to bring questionable installations or work that covers up defects to the attention of their supervisor, so that work can be stopped immediately if necessary. Use customized forms to address all the tasks of your installation. Perform a QA/QC inspection before starting the task, during installation, after any changes, upon completion and when warranties expire. Using this information as a base for your QA/QC program can assist you in developing an effective, easy-to-use system, which may help verify quality construction.
- Documentation—In the course of building construction, many types of documents are created, such as superintendent log books, inspection forms, material purchase orders, training documents, drawings and specifications, etc. All of this information could be critical in the event of a construction defect claim. When allegations of construction defect are made, these documents may help investigators understand what happened and why. You never know what document could be the one that exonerates your company from allegations, whether a change order or a submittal. Not having all the necessary documentation can pose a serious risk to the construction company and increase the cost to defend against the loss. Change orders, requests for information and documented maintenance requirements for owners should all be saved in a job file. Another common mistake is not fully documenting verbal changes made in the field. Always document changes to the design, and ensure appropriate owner representatives sign off before starting work. Photo documentation has become widely used for capturing as-built conditions and, in general, is an effective way to help defend against construction defect allegations.
- Retention of documents— Because construction defect claims are most often made well after a project is completed—sometimes as much as 10 years later—contractors must have access to pertinent construction documents. Each state has varying retention requirements, so appropriate legal counsel should be sought for your particular state and situation. Documentation retention should be part of your QA/QC program, and following both the document retention and QA/QC programs are equally important.
So, what happens when allegations of construction defect are made against you years later? When allegations of construction defect are received, whether by legal action or otherwise, a contractor may respond immediately to remediate the conditions. While a rapid response sometimes fixes the issues, all too often, the remediation or repair alters the as-built conditions and may remove evidence of what really happened and why. Therefore, an investigation must consider every contractor and ancillary company that could have a right to observe these as-built conditions. Both the as-built conditions and all of the physical evidence should be preserved for inspection in place and/or off site by all parties that have a right to review the evidence. For example, in some construction defect losses, where materials such as plastic and steel piping, concrete cores, plumbing fittings, etc., were preserved for analysis years later, the product analysis that was conducted exonerated the contractors in initial allegations.
Insurance carriers that specialize in construction, where disciplines such as claim, risk control and legal counsel have spent years investigating a variety of construction defect allegations, can offer guidance that can help explain what happened and why, which often results in mitigating resultant costs. A fair comparison is car repair: Do you take your car that needs a new transmission to a brake repair shop? No, you want a repair shop that specializes in transmission repair.
While no construction company wants to face a construction defect claim, no firm is immune. Developing and implementing a QA/QC program with a strict documentation retention policy and quickly reporting claims can help you protect your business against construction defect allegations and maintain the reputation you have worked so hard to establish.