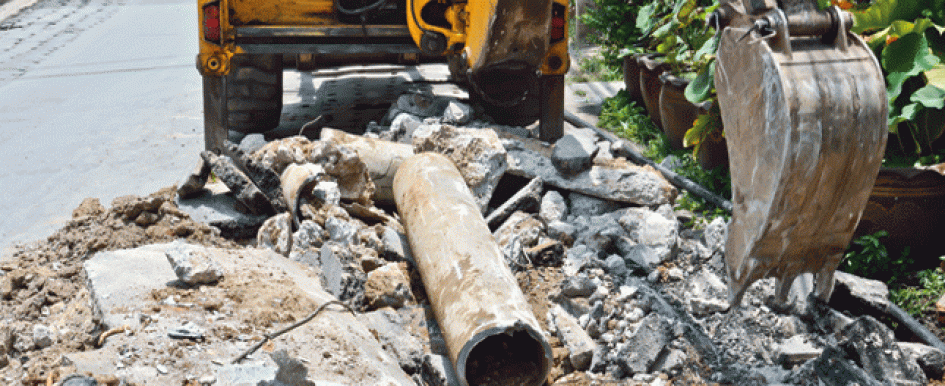
Editor’s Note: In the August issue of CBO, Wagner described the possible pollution problems that can derail a project. To view the article, “Are You Vulnerable to Pollution Claims?” click here.
Some may view pollution incidents in construction as low-frequency events; however, they are typically severe and can eliminate project profit. The first and perhaps most important step in managing environmental exposures is identification: You can’t solve a problem if you don’t know it exists. A straightforward way of thinking about environmental exposures in construction is to think in terms of indoor and outdoor exposures.
Indoor Environmental Exposures
Buildings constructed before 1980 have the potential to contain hazardous building materials. Once used for their “beneficial” properties (heat-resistant asbestos, corrosion-inhibiting lead-based paint, electrical-conducting mercury), many building materials have since been determined to be hazardous and sometimes cancer-causing. As a result, once widely used building materials now cause potential environmental liability to the contractor.
Asbestos is often found in insulation, surfacing material, wallboard, floor and ceiling tiles, gaskets and brake linings. (It was even used as snow in the movie The Wizard of Oz.) Lead can be found in paint, solder, tank linings, roof flashings and the soil around painted structures such as water tanks. Polychlorinated biphenyl (PCBs) can be found in old transformers, hydraulic systems, light ballasts and caulk. Many of us remember mercury thermometers but don’t realize this substance is also present in thermostats, barometers and fluorescent lamps.
To prevent claims associated with disturbance, removal and improper disposal of contaminated building materials, you must first identify the potential pollution risks at the building site. Contractors should determine the age of the building or structure where they are working by reviewing Phase I Environmental Site Assessment reports or other historical information sources like aerial photographs or interviews with former site personnel. Ask the site owner for this information. If the owner bought or sold the property, the bank likely required a Phase I Environmental report, and the owner should have a copy readily available. Once the building’s age is determined, you must identify the potentially problematic building materials. You can take samples of the materials or assume contamination based on their age.
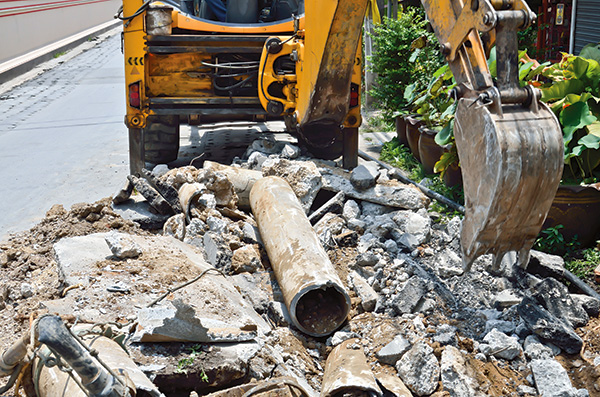
You should also assess the condition of the building materials in question. Asbestos becomes dangerous when friable, so an intact, glued-down, asbestos-containing floor tile is harmless until prying, scraping and sanding operations are used to remove them. Decide whether the contaminated building materials will remain in place or be removed. Then, adjust work practices to minimize worker exposure (i.e. wet methods to minimize dust, containment, personal protective equipment or subcontracting to a professional environmental firm to handle the contaminated materials).
Other indoor exposures include mold and indoor air quality issues. Mold has also led to some large insurance claims in the past decade. Mold claims are complex and arise from what can be referred to as a perfect storm that leads to mold growth—cellulose building materials (food source), warm and damp environments, airtight construction and a lack of ventilation. Contractors need to minimize water intrusion and moisture in areas containing cellulose building materials such as insulation and drywall. Indoor air quality issues have made the news with legionella outbreaks spanning from Australia to Argentina, Pittsburgh to Chicago. Many large buildings contain colonies of legionella, a bacteria that thrives in warm water and can grow in standing water associated with cooling towers, potable water systems, decorative fountains and hot water distribution systems. For this reason, contractors must be aware of water system design configurations.
Outdoor Environmental Exposures
Other sources of environmental liability that contractors must identify occur outside the building site in the form of pre-existing contamination. The difference between developing a greenfield site that has never been used and building on a previously used site that was a former gasoline station, for example, is like night and day for a construction company’s potential liabilities. The past material-handling practices of former gas stations, dry cleaners, printers and manufacturing sites can pose problems for the contractor. Knowing that a site was a dry cleaner in the 1950s should be a red flag to the contractor performing excavation. Insurance company claim payments for environmental contamination at old dry cleaning sites are vivid proof of this risk. The cost of sampling may seem high, but there are alternatives. Knowing the red flag exists, a contractor can negotiate contractual responsibilities differently, pushing responsibility back to the owner. The contractor can also assume contaminated soil is present and handle the situation accordingly, never paying for a sample. What is certain is this: Ignoring the potential for liability is a tremendous gamble, and as with all gamblers, there seem to be more losers than winners.
Exposure identification puts the contractor in a proactive position rather than a reactive one. Contractors can follow these steps to manage liability issues when they have identified environmental exposures at a project site:
- Avoid the project completely if the potential environmental liability seems too high or appears to be unmanageable.
- Price the project appropriately. As in the insurance industry, higher risks lead to higher premiums. If you can’t get paid appropriately for the risk you are taking, avoid the project altogether.
- Manage the exposure with written programs and employee training. Ensure that a qualified project manager, superintendent or foreman is present, aware of the controls and empowered to stop work if necessary.
- Change the work method. For example, switch from abrasive sanding to manually removing materials or from a dry method to a wet method.
- Redesign or reconfigure the project footprint to avoid areas of contamination, or take more drastic measures and pick a different site.
- Remove contamination completely, or leave contamination in place and cap it with a parking lot.
- Proactive solutions are far more appealing than reacting to a Department of Environmental Protection or Department of Health visit, paying a fine or penalty and rescheduling a project that got off track because of an unknown environmental issue. Proactive solutions require that you first identify the issue and plan how you will manage it.
Sounds reasonable, right? Then why do construction companies face these exposures and insurance companies pay these claims every day? Not all environmental exposures can be identified and managed up front. There are surprises, such as the unknown (and illegal) dredge disposal site that is completely contaminated with heavy metals and PCBs but looks like a young forest.
Consider these other examples of unexpected contamination:
- An empty field that was a former fruit orchard with pesticide-contaminated soil
- A leaking underground tank that no one identified
- The site of an old machine shop where a former employee dumped solvents and degreasers out the back door for years
Companies purchase insurance for these unexpected events. However, nothing is worse than paying for coverage, having a problem and realizing that either you did not purchase the right coverage or you negated coverage by not following the coverage rules.
While there are pollution givebacks in some general liability (GL) policies, remember that an entire environmental insurance industry was created to fill the GL pollution gap. No matter how broad the giveback, GLs likely do not cover the cost of cleanup—the most significant cost in a pollution claim. Relying on your GL policy to protect you from pollution incidents is a potentially costly gamble. If you do purchase a contractor’s pollution liability (CPL) policy, your most important action in the event of a pollution incident is to notify your carrier. The worst mistake you can make is to assume you can handle the problem within your self-insured retention, only to find out that you can’t. Despite popular opinion, insurance carriers do not penalize or look at companies differently based on claim notices that go nowhere. The opposite is actually true: They view companies that put them on notice of potential problems as being proactive, well-managed and savvy. Late notice can negate coverage—don’t jeopardize your protection.
Once you understand the risks you may face on your jobsite, you must implement the correct procedures, controls and tools (including insurance) to help mitigate those risks.
The complexity of today’s construction projects is ever-increasing. When it comes to being prepared for the environmental hazards that could negatively affect your project, knowledge is power.