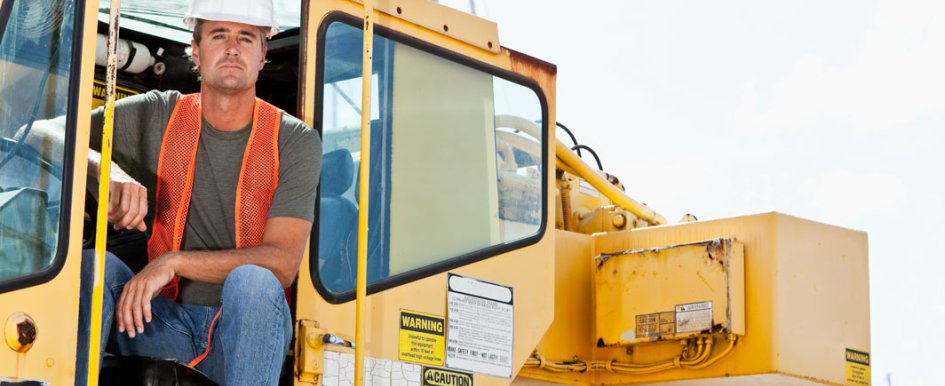
Aforecast from PwC, also known as PricewaterhouseCoopers, estimates the volume of construction output will grow by 85 percent to $15.5 trillion worldwide by 2030. Such growth presents both a challenge and an opportunity for companies. Faced with increasing pressure and razor-thin margins, businesses are making significant investments in telematics technologies to meet this demand. The data collected through telematics provides fleet managers with a direct line of sight into how much material is hauled, how long it takes to complete a haul and how much fuel is burned from point A to point B. But these vehicles and assets are not working autonomously. In addition to providing a direct line of sight into a fleet’s inner workings, telematics systems offer a variety of training benefits for employees, which will ensure greater productivity and cost savings.
Make Every Operator Your Best Operator
When visiting any jobsite around the world, you will find employees with a wide range of skill sets—from new hires learning the ropes to veterans with 30 years of practice. While the ultimate goal of training new hires is to get them to the same level as the veterans, it is nearly impossible to teach 3 decades of experience in a week-long onboarding course.
Thanks to the insights generated through telematics, construction managers can now set a knowledge baseline for an entire fleet. Managers define parameters on how to score operator behavior—whether it’s speeding, idling or harsh breaking—and use the telematics system to monitor and identify activities that deviate from the baseline. Some managers may even create a bonus structure to incentivize and reward operators for high performance.
This data creates an equal playing field for all employees to not only protect their well-being, but also the company’s bottom line. The upfront investment in telematics and the resources leveraged for employee training will be recouped as construction fleets gain a competitive advantage in three critical areas:
- Safety—Speeding, harsh cornering, heavy braking and distraction are just a few of the top safety risks on and off the road. Telematics allows fleet managers to train and course-correct behavior in real time. Audio alerts are sent directly to an operator’s phone, tablet or GPS navigation tool, which delivers instant feedback and potentially prevents an accident. Telematics further protects drivers and operators from unwanted repercussions. Some companies have enacted policies that result in job termination if too many points are accrued, but this pertains to on-road vehicles in particular.
- Maintenance—Unsafe driving or operating behavior adds to the wear and tear of equipment and costly components. Construction companies already contend with increasingly tight budgets and rising operating expenses, so telematics helps close the gap for error. Telematics further protects the company and its equipment by providing detailed reports on the state of every vehicle. The system can preemptively alert equipment managers when assets are coming due for service, notify of diagnostic issues and calculate costs associated with repairs.
- Cost—While construction vehicles may not log many miles, they can log thousands of engine hours. Fuel—second only to payroll as the largest expense for a construction fleet—is burned inefficiently based on the sheer amount of the weights being carried and the constant stop and go. Therefore, production efficiency is paramount when coordinating batch plant, quarry loading and construction site deliveries. Using telematics, managers can track every movement and realize the actual operating costs of haul cycles. When managers better understand how their machines are being operated and where there is excess use or idling, they can make adjustments to operational behavior for immediate improvements.
Make the Most of Your Telematics Investment
Construction companies will get even more out of their telematics investment by taking a closer look at the vehicle operators—not just the equipment, haul times or site conditions alone. And by developing a baseline of knowledge, fleets build a more sustainable business strategy, which is supported by their highly trained employees.