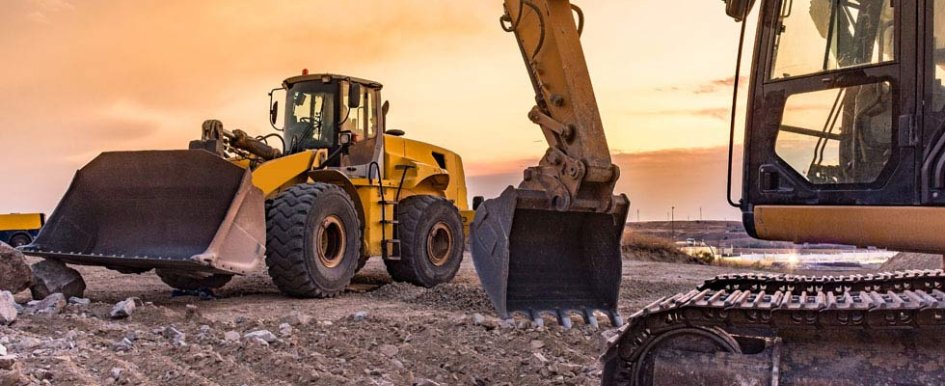
The winter months present an outstanding time for construction business owners and their teams to optimize their fleet maintenance programs. For many in northern states, cold and snow can bring construction work to a halt, but even in warmer climates, where work continues, it’s important to take some time to intentionally review and analyze how you might be able to optimize uptime and efficiency. With just a few tweaks to your preventive maintenance program, your equipment can deliver meaningful results.
Diesel Exhaust Fluid Management
Let’s be honest, the implementation of selective catalytic reduction (SCR) systems and diesel exhaust fluid (DEF) across all new heavy equipment has created another layer of heavy equipment maintenance for contractors to manage. While some view it as a headache, it’s also an opportunity to protect your high-horsepower equipment by making sure your DEF is being properly managed to keep it from contamination and freezing.
While contamination isn’t a winter-specific issue, maintaining DEF purity is essential throughout the year. A best practice that should be considered regarding DEF management is the utilization of an International Organization for Standardization (ISO)-compliant, closed-loop DEF pumping system that minimizes the risk of contamination that is often a risk on jobsites and off-road environments.
DEF freezes at 12 degrees, so if you aren’t running your equipment in the winter, you should drain your DEF tanks before storage. Simply empty the tank into your poly bulk DEF tote. It is important to remember that freezing won’t impact the integrity of your DEF since it’s made up of 66% distilled water, but you should ensure the freezing happens in an environment where it’s not also freezing amongst critical parts and components within the SCR system.
Take Your Maintenance Program Mobile
Implementing a mobile preventive maintenance program is a concept that brings value, no matter your geography. It is recommended to develop a plan to go mobile now because making significant change to your operation is always better done outside of peak season than right in the heat of battle. Bringing your maintenance team and service and lube solution to the equipment in the field — rather than returning to a home plant or headquarters — can save construction companies multiple hours per day on each maintenance service, not including the additional time savings from no longer transporting equipment back-and-forth to your home base.
Implementing a mobile preventive maintenance program saves time in other ways too. For example, going mobile lets companies schedule and conduct preventive maintenance during times that best fit their schedule. Especially in the face of strained staffing and skilled labor shortages, among other challenges, being able to conduct maintenance at times that best meet the needs of your team is a huge benefit.
Additionally, keeping equipment on a constant preventive maintenance schedule without having to remove it from the field helps to maximize uptime and profitability, both of which are paramount to success on the jobsite. There’s nothing worse than a piece of premium equipment being out of operation during a high-volume period. Construction companies across the country that have implemented a rock-solid mobile preventive maintenance schedule are protecting themselves against that very issue.
Design a System That Works for You
All operations are different but depending on the type and size of equipment you’re running, a robust 2,000-hour preventive maintenance service for a single machine could include up to 500 gallons of fluid — when considering engine oil, differentials and hydraulic fluid — and 25 filters or more. These types of services take hours to complete, so depending on your operation, it might be more palatable to put your equipment on a 500-hour, 1,000-hour and 2,000-hour maintenance rotation.
In terms of equipment to help you get the job done, there are a lot of different solutions. There are large, all-in-one lube trucks, medium-duty truck upfits or lower cost, equally capable trailer solutions. Some truck upfits and most trailer solutions would eliminate the need for your operator to carry a commercial driver’s license (CDL) or a HAZMAT endorsement, potentially reducing insurance costs and streamlining the process of identifying and recruiting qualified workers. No matter the solution that’s right for your operation, mobile fleet maintenance programs are a great way to reduce downtime and protect your investments.
There is a lot to consider when it comes to implementing mobile fleet maintenance into your operation but recognize that now is the time to take those steps. While winter is lingering, signs of spring are right around the corner Before you know it, you’ll be getting ramped back up for the time of year you love the most: peak construction season.