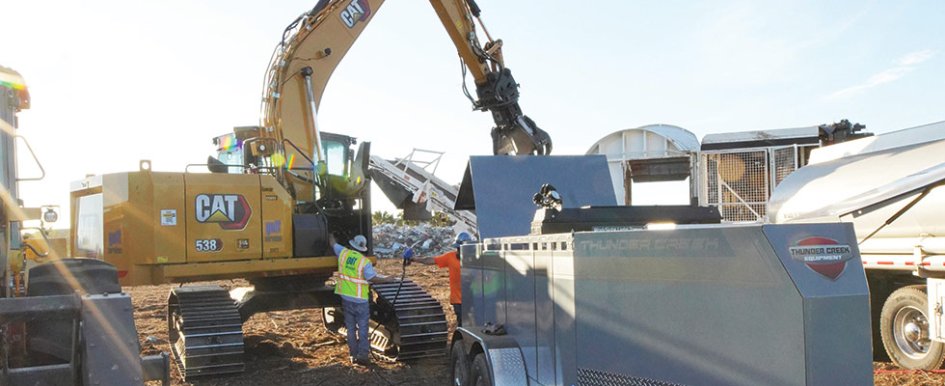
“An apple a day keeps the doctor away.” As adults, we know the old saying may not exactly be true. (Although it’s a heck of a marketing strategy for the apple industry!)
What is entirely true: That old saying’s message of preventive measures to ensure long-term health is entirely applicable to running a fleet of heavy equipment.
“Check the operator’s manual” is an easy mantra when it comes to scheduling preventive maintenance (PM) activities, but we all know it’s more complicated than that. There are working schedules, machine location, staff and resource availability to consider. The most important thing to remember is that those PM intervals are not merely suggestions — they are the manufacturer’s best recommendation for the optimal uptime and performance of your equipment.
In this article we’ll discuss the importance of PM and the merits of building a PM schedule and practice in your business around performing that work in the field. There are technologies today that simplify field PM activities, don’t require massive service trucks, and help ensure that PM can be performed cleanly, to original equipment manufacturer (OEM) standards and with consideration for fluid integrity and safe handling.
More Uptime
Another old saying that we really don’t give enough weight to is “time is money.” While fleet managers may prefer to take equipment back to a more clean and controlled shop environment to perform PM activities such as oil changes, the time and expense it takes to pull that machine from the site and transport it back to the shop include time that machine isn’t running, labor associated with the truck driver getting the machine to and from the shop, and then wear and tear on the hauling truck itself.
Bringing all the tools needed to perform PM to the field helps reduce that excess time and allows you to schedule PMs for off hours when the machine isn’t working. This ensures the optimal uptime of the machine (profitability during working hours available) while decreasing input costs into your business (labor, trucking, etc.). Between the increasing adoption of telematics and the ability to bring more of the PM activities into the field, it presents business owners the ability to establish a more mobile and decentralized fleet management strategy, which can shift focus from “How do we get equipment back to the shop?” to “How do we service it where it is and simply focus on getting it to the next job?”
Less Downtime
In addition to scheduling and performing PM work in a way that ensures it doesn’t conflict with billable hours, it should also always be remembered that faithfully performing PM work will help prevent future inefficient machine use and failures.
This could be as simple as a hydraulic system not functioning properly and slowing down performance, or as devastating as a complete engine or emissions systems failure that renders a machine useless.
Building a fleet management strategy focused on performing PM in the field removes the opportunity or willingness to say, “Oh well, that machine only needs another week on-site … We’ll let it go for PM until we can get it back to the shop.” You can instead focus on taking the PM work to the machine at the recommended timing from the manufacturer to ensure ongoing optimal performance.
And why is this all important? Committedly staying ahead of or on schedule with PM will minimize the opportunities for failures to occur — failures that have the potential of incurring much higher repair bills, much longer downtime and a significantly higher total cost of ownership of that machine over its lifetime.
Rethinking the “Service Truck”
The reality is that many small- to midsized businesses and contractors can’t afford to own a full-sized service truck decked out with all the fluid storage and tools needed to perform PM.
That may have been a deterrent in the past — the purchase price, the insurance costs, liability, finding drivers who have the appropriate certifications — but newer technologies have been introduced into the industry in recent years that make it possible to get everything needed to perform PM work to the field without those requirements.
While local laws may apply, there are multiple trailer platforms now available to consumers that allow you to transfer all fluids and materials needed to perform PM work to the field:
- In tank volumes and configurations that eliminate the need for a driver’s HAZMAT endorsement
- In gross vehicle weight rating (GVWR) combinations that do not require the driver to have a commercial driver’s license (CDL)
- That are inclusive of all critical fluids, filters and systems that encompass the most common PM activities: oil (numerous types/weights), grease, diesel, diesel exhaust fluid (DEF), and reclaim systems that help you effectively transfer and dispose of waste fluids once the PM is complete
These advantages make it easier to find suitable labor to drive the trailers and perform the PM work needed in the field. We are seeing businesses create entire jobs/positions around personnel with standard driver’s licenses who can drive the truck and trailer and perform the PM work in the field.
These trailers can also be fitted with utility boxes and compartments for critical field maintenance tools such as compressors, generators, welders, greasing systems, DEF systems and more, delivering as much value to the jobsite as a larger, more expensive service truck.
The lesson: The overall cost and labor expense of performing PM work in the field can now be less than it has ever been before, while delivering you all the advantages of PM work in the field that focuses on uptime and machine performance — helping you be more profitable throughout your entire operation.