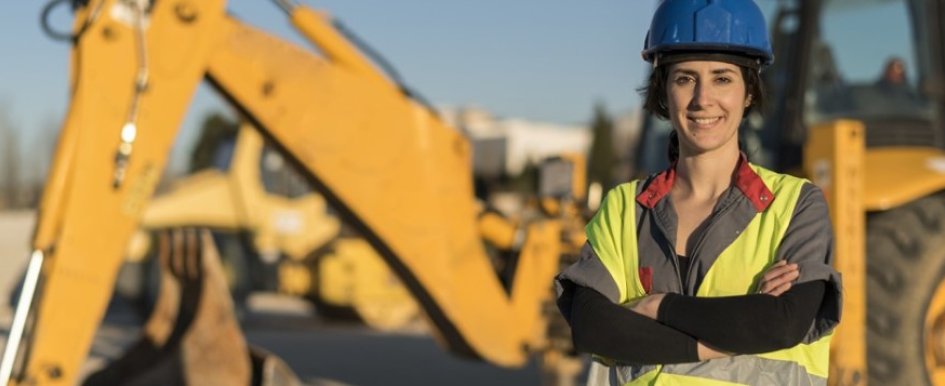
In the construction business, time is money, and productivity a priority. As such, vehicles and equipment used to support key operations must be available when and where required. A professional and experienced fleet management team can meet a plethora of challenges head on by acquiring the right assets, tracking those assets, reducing equipment downtime and promoting safety and sustainability.
This is pretty true of fleets across many industries, right? So what’s unique about the construction industry? Consider the following:
- Fleet composition normally ranges greatly from light-duty pickup trucks, to bulldozers, to excavators and more.
- Each piece of equipment serves a special purpose and is usually built specifically for or acquired for that purpose.
- Acquisition of specialty equipment, such as excavators and cranes, is time consuming, as fleet managers have to develop specifications and participate in the competitive bidding process.
- Construction vehicles take a beating and, thus, require upkeep, as well as preventative maintenance.
Perhaps the most important characteristic, however, is the link between equipment and personnel resources. West Valley Construction Company’s (WVCC) Vice President of Corporate Assets Jimm Vosburgh agrees that the labor costs associated with a piece of equipment are a unique characteristic of construction fleets.
He notes, “If the equipment fails, there could be 10 people standing around. When an excavator breaks down, not just the digging crew is impacted; all the other crews coming behind the digging crew come to a halt as well.” Ultimately, construction companies rely on two main assets to get the job done—people and equipment. If either component is missing, operations suffer.
As a utility contractor, Vosburgh operates a fleet of approximately 400 on-road vehicles, Class 6 and below. His flagship pieces are crew trucks, of which approximately 50 are on the road daily, with crews of five to 10. WVCC has eight maintenance facilities; two large shops (four bays with five to six mechanics); three medium shops (two to three bays and people); and three single mechanic shops. Along with the specialized fleet and personnel needs that come with owning a construction business, like Vosburgh’s, also come specific challenges.
1. Sustainability: Stop Idling When You are Idle
Running equipment requires fuel, and that fuel is costly in terms of both money and negative environmental impact. Improving mileage by only one mile-per-gallon for a vehicle that travels 30,000 miles per year would result in more than $200 in savings (assuming the fuel is priced at $3.65 per gallon).
Even more costly for construction fleets is the practice of idling equipment when it is not being used. Idling can burn 2 gallons of fuel over a 10-hour shift, releasing many pollutants into the atmosphere. Even knowing this, it can still be tough for a fleet manager to sell crew members and company leaders on sustainable initiatives, as they involve changing long-established behaviors and practices.
Vosburgh has been a leader in this area, introducing many sustainability initiatives to WVCC. He has attended the North American Green Fleet Forum for the past 6 years. His initial reaction to the suggestions heard there, was “We’re a construction fleet, so we can’t introduce sustainable initiatives.”
Over the years, however, he has been able to create a convincing case in his own business model with the introduction of renewable diesel, select use of electric vehicles, solar charging of the fuel island and reduced idling. The idling reduction initiative alone resulted in a $2,000-per-month savings almost immediately, just through the education of drivers and tracking of driver compliance.
With these accomplishments in hand, Vosburgh set his sights on being recognized as a sustainable fleet by the NAFA Fleet Management Association and its Sustainable Fleet Accreditation Program. “It was a bit of a tough sell initially,” says Vosburgh of his proposal to get his fleet accredited. “I had to justify that there would be cost savings in doing the right thing. Most people understand water conservation, so I used that as a model to explain why we might want to conserve fuel.”
For those seeking the same (or similar) accreditation, Vosburgh recommends working as a partner with customers in your sustainable efforts and linking those efforts to emergency planning. In his case, partial justification for the extra expense of using solar panels as the means of powering the fuel island was that they are also a potential power source in the event of the grid going down during an emergency.
2. Asset Tracking: Don’t Play Hide & Seek
Knowing where all of your assets are at a given time is essential for the efficient management of a construction fleet. Whether you are trying to find out how far along a route a grader is, which jobsite is using a certain excavator or where a backhoe is located on a specific jobsite, asset tracking in real time is essential. Asset tracking can also assist in the recovery of stolen equipment, which amounts to over $600 million annually in the United States.
As such, WVCC has recently adopted Geotab Inc.’s platform for their asset tracking needs. The challenge now is to sift through the vast amounts of information the software is capable of providing and prioritize the data, deciding which pieces are needed live, hourly, daily, monthly, etc. To overcome any operator resistance to telematics use, the company introduced a recognition program, in which the top (and lowest) performing units are recognized for meeting, or failing to meet, specific productivity and fuel targets.
3. Preventive Maintenance: Fix it Before it Breaks
Adherence to the manufacturer’s preventive maintenance guidelines has many advantages. In general, it helps you reduce downtime, avoid costly repairs, ensure warranties remain valid and increase overall productivity. Some important tips for preventive maintenance success are as follows:
- Keep construction equipment clean to reduce rust and extend the life span.
- Tailor your maintenance schedules to account for manufacturers’ guidelines, vehicle age and primary task or function.
- Harness telematics-generated data to assist in regular and preventive maintenance scheduling.
- Have a central coordinating authority to manage maintenance appointments and the resulting paperwork and repairs.
- Bolster your maintenance program with daily vehicle inspections, both before and after use.
To help ensure daily equipment inspections are done, WVCC generates a daily report of what has moved in the yard in the previous 24 hours. This log is compared to the daily vehicle inspection reports (DVIR) to determine which pieces of equipment have outstanding maintenance needs. Vosburgh also suggests holding training on DVIR completion, including examples of poor DVIRs.
Implementing programs and processes like these can seem like daunting challenges, but there are resources available to assist fleet managers in educating themselves. Fleet managers should also look to professional organizations that offer professional designations in fleet management, asset management, maintenance management, sustainability and other areas for corporate and government fleets with all types of vehicles and equipment.