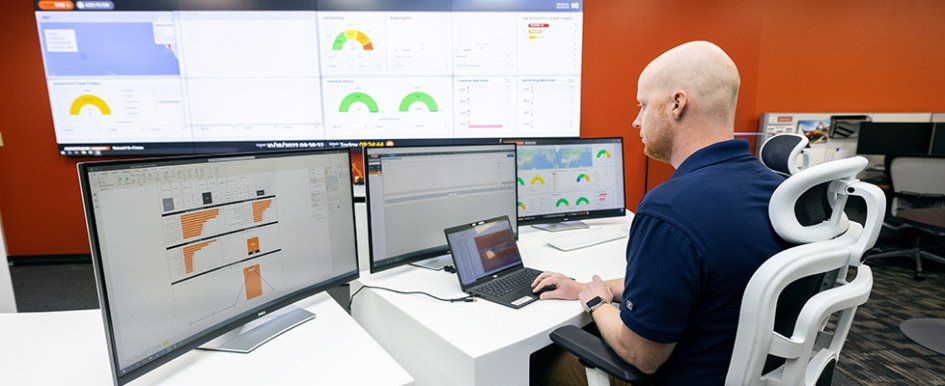
As a business owner, you do more than look after the equipment: You also purchase products and talk to vendors. Since your role is cross-functional, there is a benefit to understanding the technology at your disposal that can help relieve some of your day-to-day tasks.
In today’s equipment landscape, there’s no shortage of technologies, like telematics machine monitoring services, available to help you improve your operation, enhance safety and make your business run smoother. We’ll discuss telematics and how a fleet monitoring service can help you stay focused on the business while it works to protect your construction equipment.
What Is Telematics?
Today’s heavy construction equipment and mini excavators are likely already equipped with onboard fleet tracking technologies, called telematics, to track and report data in real time. Many industries, including the construction equipment industry, use telematics to collect data on their machines. Telematics systems can provide you with a better understanding of how, when and where construction equipment is being used. The location is provided in longitude and latitude, and the mapping software automatically changes to the closest address.
Many fleet tracking technologies use a terminal that is installed on equipment to gather and communicate data wirelessly via cellular or satellite service. The machine’s data is then sent to a website where you, your operators and your equipment dealer can monitor the machine’s performance, operating hours, fuel usage, engine idle time and work time. You can also monitor engine/hydraulic oil temperature and view fault and warning codes via a computer or cellular device.
How Do Telematics Fleet Management Systems Work?
Using a machine’s telematics data, employees of the fleet management system will monitor a subscriber’s machine remotely from a machine monitoring center for critical machine fault codes, upcoming and overdue service and warranty expirations. When a machine alert is triggered, the telematics system will send two messages via email — one to you and one to the dealer — and push notifications.
The email notification will alert you to any immediate action that needs to be taken to prevent potential machine damage. For example, your operator may need to shut down an excavator or wheel loader until a critical issue can be fixed. Some simple issues can be addressed by an operator at the jobsite, meaning the machine has little or no downtime and you can stay on schedule.
A machine utilization report will be sent for each machine subscribed to the service. Recommendations for how to improve fuel efficiency and reduce machine wear may be included. The report will also indicate upcoming machine maintenance needs.
Your dealer will also have access to the machine reports. Their service department can identify upcoming machine maintenance and contact you to schedule a convenient day and time to perform the service, minimizing any schedule disruptions.
To activate the service, you’ll likely pay a monthly fee per machine. Some manufacturers offer a special trial of the service when you buy a new machine. Check with your local dealer for more details.
How Can Telematics Monitoring Services Help You?
The information gleaned from a telematics monitoring service can be used to help you and your business in a variety of ways. Here are a few examples:
- Better allocate resources — Telematics data can show you exactly where and how often your equipment is being used. By analyzing this data, you can determine if you are underusing your assets or whether it is time to invest in adding to your equipment fleet. Adjusting your fleet size to meet your needs can also help reduce equipment costs.
- Fine-tune bids — If you want to create accurate estimates on future projects, telematics can help by providing you with data on machine hours and fuel usage to determine operating costs and labor costs for more accurate billing.
- Promote better operator behavior — Data collected through telematics systems can be used to solve business challenges and improve operator performance, such as reducing prolonged idle time or improper use of equipment on the jobsite. By monitoring this data, you can correct these issues to promote a more productive and safer jobsite. You can also identify areas where you can reduce operating costs to extend component life cycles and reduce the frequency of unplanned maintenance.
- Save on downtime — Your dealership may be able to diagnose a problem without physically being in the same location as the machine for faster response time. This will help save unnecessary machine downtime and reduce travel time for your dealership’s service department. When a technician does need to visit your jobsite, they will be better prepared to fix your issue because of telematics data shared with the dealership.
- Improve fuel efficiency — Telematics data can help you improve equipment fuel usage and efficiency. The system monitors equipment idle, helping you identify machines that are working under or over capacity. Reducing idle times can also extend engine life and reduce repair and maintenance costs. And you can monitor power mode operation and adjust the power mode to do the same work while using less fuel.
- Help prevent unauthorized operation — You can use telematics history reports to keep a close eye on your machine and see where it’s been operated. A geofence or an invisible/virtual boundary can be created through the machine’s GPS system. If your machine leaves the virtual fence, it will send a notification and can alert the authorities about possible equipment theft. A time fence or curfew on each machine can also be created. If the machine is operated outside of working hours, an email or text notification can be sent to you. This helps prevent unauthorized operation and potential vandalism to the machine and jobsite.
Since telematics monitoring systems are unique to each equipment manufacturer, schedule a demo with your local equipment dealer to have them explain in detail how to use the system. These systems have a variety of benefits to help you make smarter decisions about how to manage your fleet as well as increase efficiency on the jobsite.