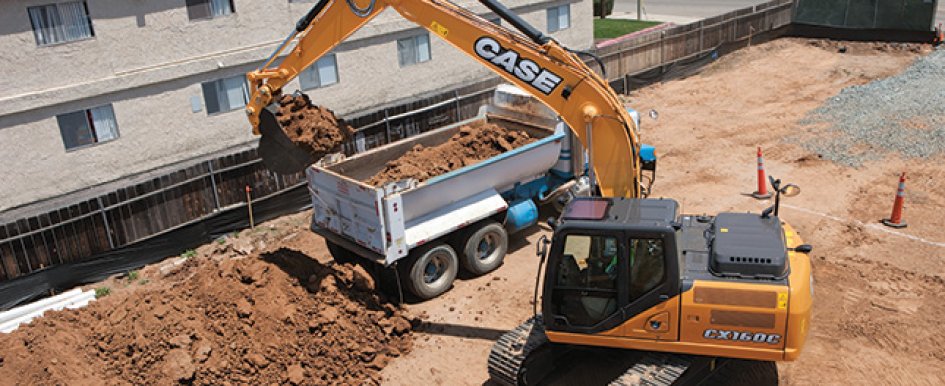
The entire conversation about Tier 4 regulations is often lumped into two technological buckets: selective catalytic reduction (SCR) and cooled exhaust gas recirculation (CEGR). These are the two technologies—with some variation—that are helping equipment manufacturers achieve mandated emissions standards. While the treatment technologies get most of the press, manufacturers have achieved additional machine innovations that benefit equipment owners and operators in ways beyond merely meeting emissions requirements. Many of these innovations derive from electronics systems that not only help meet Tier 4 standards but also achieve new levels of fuel efficiency, productivity and control. Other advances are the result of pure engineering. Manufacturers are improving the overall profitability of their customers by considering how available technology solutions fit into each machine and general application.
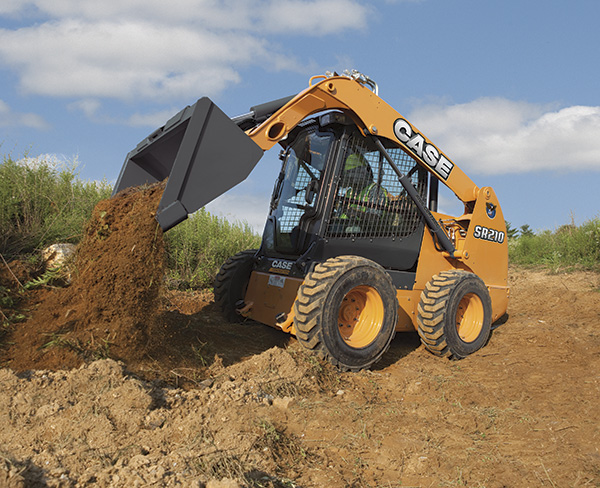
Better Fuel Efficiency
Tier 4 interim and Tier 4 final solutions have forced engine manufacturers to focus more on efficiency—one way has been through the marriage of advanced electronics and fuel injection methods/designs. At their most basic level, emissions consist of leftovers from the combustion process. Advanced electronics paired with high-pressure common rail (HPCR) systems have allowed for more exact fuel injection to take place, putting just as much pressurized fuel into the combustion chamber as needed. This creates better and more efficient use of that fuel to get more power from the engine. Advancements in piston designs also promote a better mixture of air and fuel, leading to more thorough combustion.
Older systems would inject a greater amount of fuel into the chamber, where a less efficient burn would occur and result in wasted fuel and less power. Today’s Tier 4 engines create comparable or greater horsepower with less fuel, providing the machine owner with more production for the same or reduced cost.
Manufacturers are also achieving fuel efficiency relative to pre-Tier 4 machines by incorporating more efficient systems around the engine. Wheel loaders, for instance, have migrated to a five-speed transmission with a lock-up torque converter. The lock-up torque converter offers more gear selections to keep the engine operating in its best power range, increasing fuel savings at roading speeds by as much as 40 percent.
Hydraulics have similarly helped improve performance and fuel efficiency. Manufacturers have designed larger return lines in excavators to minimize backpressure buildup (eliminating the need to overcome that back pressure, which saves energy). Variable displacement pumps have been built into wheel loaders and backhoes. These pumps do not pump oil when a load is sensed as compared to a fixed pump that pumps oil at all times, which creates wasted energy and fuel loss. Backhoes have achieved 7 to 8 percent fuel savings by using this technology.
More Consistent and Reliable Turbo Power
Another example of the marriage of electronics and engine technology is the improvement of turbocharger performance through the implementation of a boost pressure modulator valve, commonly found on small- to medium-size Tier 4 engines. Turbochargers are driven by an engine’s exhaust gas. That gas spins a turbine that powers the turbocharger’s compressor. This is subject to variance based on machine output and can lead to inconsistent compressed air in the intake system.
A boost pressure modulator valve, made possible through advanced electronics, helps eliminate those variances and provides more consistent compressed air into the intake. The valve holds that pressure more effectively and allows for better overall turbo power.
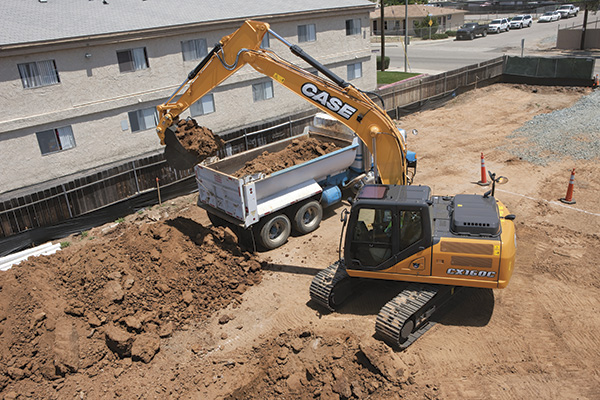
A boost pressure modulator valve wears the turbo less and allows for longer turbo life. A turbo is designed to continually push air. If the turbo ramps up and slows down, the bearings and other components are probably subject to rapid waves of inconsistent heating and cooling, which leads to wear. This system modulates how the turbo holds pressure in the intake, maintains a level atmosphere and eliminates the inconsistent nature of performance.
Greater Operator Control
Advanced electronics also give operators more control over the power a machine uses to get the job done. These electronics have made available across many equipment categories a wider selection of work modes that match the work of the engine and related components to the task at hand. These work modes conserve fuel by allowing the machine to provide maximum productivity and deliver only as much power as needed.
Advanced electronics have also made it possible for new electronic modules to control functions throughout the machine. Controller Area Network (or CAN-bus) technology connects these modules and facilitates communication. This technology allows, for instance, the engine and the transmission to work in sync at all times, versus working as independent systems. The transmission, related drivetrain components and engine work together to match the demands of a selected mode or application.
Electronics are also responsible for other improved functions and cost savings associated with construction equipment, including the ability to adjust idle speed to match conditions and the advent of systems that automatically protect the machine when the system recognizes critical problems with hydraulics, the engine or the transmission.
Improved Throttle Response and Torque
Evolutions in Tier 4 treatment have also lead to significant advancements in productivity. Wheel loaders, for instance, have seen a shift from CEGR technologies to SCR. Because SCR is an after-treatment system and works separately from the engine, it lets the machine maximize horsepower while using less fuel than CEGR systems and doesn’t sacrifice breakout force. It can improve overall performance because the engine breathes more freely than a machine that uses CEGR technology. (In a CEGR system, exhaust gases are cooled, blended with fresh air and then returned to the engine, effectively using less of its available air volume because exhaust gas won’t burn.) This SCR technology leads to noticeable improvements in throttle response and increased torque.
Taking Skid Steers to the Next Level
In the past, cost, size and simplicity made going to an electronic engine control on a skid steer impractical. As Tier 4 pushed engineers to find new ways to meet standards, electronic engine control became a viable option for skid steers and has allowed for significant advances, including the addition of HPCR and better control over the speed and power output of the engine. It has also allowed for more sensor inputs within the machine, which provides better machine management, more informed operation and better troubleshooting of machine issues. Electronic engine control has also helped incorporate comfort and control features for the operator that were traditionally held for larger and more expensive production-type machines.
Engineering a Better Machine
While Tier 4 mandates represent a line in the sand, “reduced emissions” is not a productivity or performance factor that improves your bottom line. As the industry transitions from Tier 4 interim to Tier 4 final, manufacturers will continue to build equipment that meets federal requirements and provides you with operational benefits for your business. As new machines continue to roll out, stay tuned for more ways these Tier 4 technologies are supplemented with other advances to improve your equipment capabilities.