
While “Back to the Future” presented a world filled with flying cars, hoverboards and countless technological advancements, Oct. 21, 2015, came and went with no daily commute in a flying automobile.
That’s not to say technology has not progressed, but advancements have just been in other avenues. In the construction industry, we’ve seen advancements in manufacturing and design capabilities as well as machine applications across jobsites.
Across the industry, many innovations have been siloed to create an advantage for a specific brand, but some innovations have been a response to challenges that we each face — seeking a solution that helps contractors and manufacturers alike. Today, the challenge at the forefront of all industries is curbing emissions — the “road to zero.” With governments implementing stricter standards on emissions, legislation ensuring the progression of sustainability, as well as increasing environmental, social and governance (ESG) and shareholder commitments, many manufacturers are committed to making machines that produce less emissions for the same completed work while also reducing operating costs for customers.
From Steam to Electrification
Since the steam engine was developed by Thomas Newcomen in 1712, there have been many evolutions. From internal combustion engines (ICE) to powering engines with gasoline, diesel or biofuel, strides have been made in technology. Today’s electric-powered machines are a great alternative to fossil fuels, as they allow for zero emissions at point of use. For compact equipment that is operated for a few hours a day and uses little fuel, electric is a viable solution.
But lithium-ion batteries do have limitations. One issue with recharging machines on remote sites is that recharging locations are usually diesel-powered generators that still contribute to emissions, and machines must be brought to the charging point. For larger machines, batteries become impractical. This is due to their weight, cost and the loss in hours worked, which is a consequence of the time required to recharge the machine. Simply put, larger equipment requires more batteries, which increases the overall weight of the machine and the amount of time it takes to recharge all the batteries. Due to the extended time to recharge the batteries, your machine is now unable to complete what operations consider to be a full day. This means that our emission reductions through battery-powered machines are confined to compact equipment, which does provide emission reductions but not in the volume necessary. The road to zero requires a mix of technologies to achieve and deliver a cleaner future. Electric is absolutely part of the solution, but what other innovations are needed to reach the road to zero?
A Better Way
Never content with doing business as usual, Lord Bamford, chairman of JCB, challenged designers to “find a better way” of powering heavy equipment. The charge put to the designers required that the solution allowed machines to do the work expected by customers. The company’s design team had already been researching alternative fuel solutions for some time due to concerns over the emissions being produced around the world on jobsites, transportation and in producing consumer goods. Oil has been used for decades, and in recent years it has been used to create gasoline, diesel and kerosene to fuel vehicles, machinery and aircrafts. JCB’s efforts to find another way to fuel machines had already resulted in evaluating numerous fuel types prior to the challenge. Fuel types evaluated include hydrotreated vegetable oil (HVO), biogas, e-fuel, ammonia and hydrogen.
- HVO — It is a biofuel that is a purer form of diesel and produces the same type of tailpipe emissions as diesel-powered machines. It is also defined by a cleaner production process but produces the same emissions as diesel at the tailpipe.
- Biogas — Biogas utilizes food and crop waste to create methane by creating a circular carbon dioxide (CO2) system, not one that removes CO2 emissions from the tailpipe. One notable downside to this type is that it requires waste.
- E-fuel — E-fuel creates hydrogen that will pair with carbon dioxide to form hydrocarbon. It produces high power outputs and is lightweight, making it especially interesting to the aviation industries. One major issue with e-fuel is that your cost of fuel would be 10 times higher due to scalability of production.
- Ammonia — Available around the world due to the shipping industry, ammonia utilizes zero carbon, but requires more ammonia in volume to have the same performance as diesel. As ships have long lives, ammonia is a solution for the maritime industry due to the ease of converting their engines to run off ammonia in place of diesel. However, ammonia is highly toxic and can cause negative reactions to your eyes, nose and lungs.
- Hydrogen — It is a naturally available element and thus a clean fuel. Hydrogen is a safer alternative as it dissipates into the environment naturally — no concerns of a hydrogen spill like with diesel. It creates only water as a byproduct. It is transportable as either a gas or liquid, allowing for pipeline or tank transport. One notable concern is that green hydrogen production is not produced at volume, which means green hydrogen producers are needed to break the seller’s market.
After reviewing potential solutions and hypothesizing, it was time to prototype. The first prototype was a fuel cell-powered machine that utilized electricity and hydrogen to fuel the excavator. For the second fuel cell prototype, the designers adapted JCB’s excavator technology and added electric motors to deliver the power. Their work resulted in the construction industry’s first excavator powered by a hydrogen fuel cell, which was completed in 2020.
However, realizing 1) the complex nature of the fuel cell, 2) the cost barrier that would limit implementation for customers, and 3) an understanding that the fuel cell was not robust enough for our industry, Lord Bamford knew there still was an even better way to power heavy equipment with hydrogen.
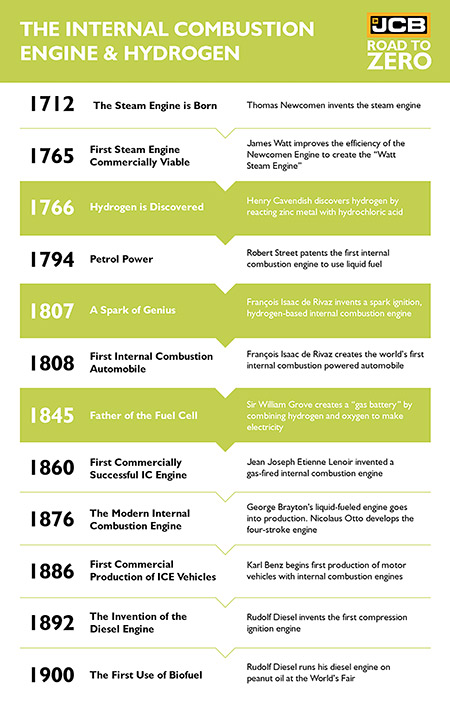
Introducing Hydrogen Combustion Technology
The engineers continued their research into hydrogen and the various types of hydrogen production to see how they could be more efficient without sacrificing machine performance. Choosing to focus on hydrogen combustion, engineers at JCB Power Systems built hydrogen combustion engine technology from the ground, while utilizing existing componentry like what is found in diesel engines, to ignite hydrogen and deliver power similarly to how power is generated and delivered in diesel engines. In 2021, the industry’s first hydrogen combustion engine was born. It was time to see if it stood up to the challenge of doing the work expected of its diesel counterpart. After putting the JCB backhoe loader fitted with the hydrogen engine through its paces, the data showed it could do everything its diesel-powered equivalent could do while only emitting steam from the tailpipe — zero CO2 from the tailpipe.
Seeing success and the possibility of zero emissions, JCB has invested 100 million pounds into the project and has two prototype hydrogen-fueled machines in testing: a backhoe loader and a Loadall telescopic handler. After installing a hydrogen combustion engine and replacing their diesel fuel tanks with hydrogen tanks, the backhoe loader and telehandler are operating with the same speed, loading and digging abilities as their diesel counterparts.
The Future of Hydrogen Combustion
Like many contractors, you may be questioning how hydrogen combustion-powered machines will be able to be implemented on jobsites. Mainly, how do we fuel the machines? First, hydrogen is easily transportable in either a liquid or gas state through channels like pipelines, freight or maritime. As a gas, hydrogen can be transported under pressure in tanks made of steel, aluminum, carbon or glass fiber. As liquid, it is transported via insulated steel tanks. The ease of transport makes hydrogen a fuel that is efficient to maximize customer uptime. A hydrogen refueller allows hydrogen to be taken from on-site trailers to each machine needing fuel. It’s the same process used today for diesel fuel, just distributing hydrogen fuel instead.
While significant strides have been taken to produce machinery that utilizes hydrogen, there are still many questions on how hydrogen can be made as accessible as diesel for operations around the country. One example of a solution to the transportation and production of hydrogen can be seen in Corpus Christi, Texas, where the phased build-in of Hydrogen City has been announced. This project has identified numerous applications for hydrogen fuel and is developing an infrastructure for full-cycle production, storage and distribution of hydrogen fuel within the state and exporting fuel potentially around the world for its customers.
This type of infrastructure can serve as a catalyst for additional facilities in North America to normalize hydrogen fuel distribution in the way that diesel is approached today. The timeline for these types of facilities could be expedited based on technology advancements in hydrogen-powered automobiles. For example, manufacturers like Toyota, Hyundai and Volvo are researching hydrogen-powered semis.
Needless to say, many industries are seeing the opportunity and effectiveness of hydrogen as a fuel type to support our collective road to zero.
None of us have all the answers or ability to unilaterally implement a plan to curb our collective emissions. However, based on our firsthand experience, we believe that a mix of technologies will allow us to achieve the road to zero — with a key driver in that mix to achieve cleaner air being hydrogen. Though, it will take each of us, our collective knowledge and abilities to implement a truly sustainable solution at scale. Together, we can write a future that looks after the planet we help to shape.