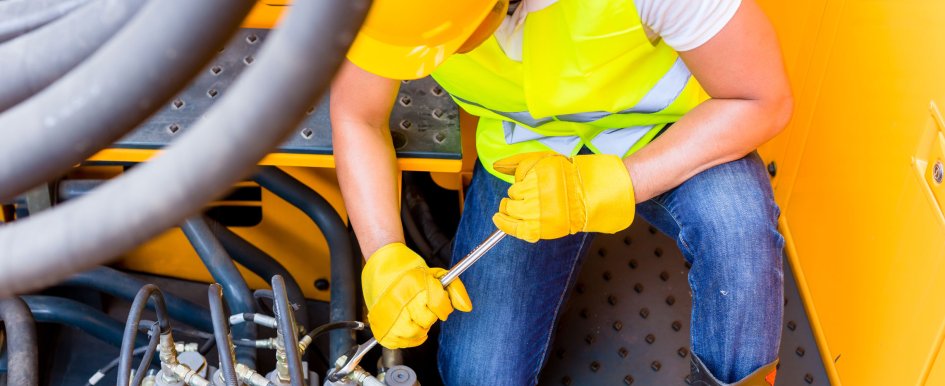
Construction equipment fleets require diligent preventive maintenance to keep them in top condition, comply with warranty contracts, lengthen lifespan and increase resale value. Fleet managers have used various time-consuming methods throughout the years to keep track of utilization, from handwritten logs to spreadsheets. The purpose of tracking is to be able to schedule routine service before a problem arises. Some managers default to performing it on a timed basis, regardless of the actual usage. Both ways have inherent drawbacks that cost time and money. Implementing real utilization data pulled from the asset itself helps you reduce downtime and ensures you are executing a maintenance schedule that keeps your fleet at peak operating performance.
The just-in-time (JIT) concept has been around since the 1970s and is generally discussed in reference to inventory. It is a strategy that companies employ to improve efficiency and decrease waste by receiving goods only as needed during the production process. This method requires producers to forecast demand accurately. It’s another way of considering predictive maintenance. Predictive is defined as predicting an event or result. It is also used in reference to computing. According to The Oxford English Dictionary definition, related to technology, predictive denotes or relates to a system for using data already stored in a computer to complete an action, such as finishing a word when texting.
Both concepts can be applied to maintenance. Your goal is to optimize the repair of assets at the time that they need. Performing repairs too soon or too late can incur added expenses and/or an idle crew. A key component is being able to forecast demand accurately. This is where vehicle and equipment telematics can help. This theory is now evolving even further with predictive intelligence through the use of telematics. Data is optimized in mastering timely scheduling, but it is also maximized to predict that an issue is likely to occur. This gives managers an edge on safety measures and the foresight to avoid costly equipment repairs.
The Costs of Inefficient Maintenance
Not performing regular maintenance leaves you open for unexpected breakdowns. Emergency repairs cost more for technician time and parts. Plus, there is no guarantee your equipment will get on the appointment book as early as you would like. The potential ripple effects are an idling crew and a delayed project. If moving assets around is not an option, there is the added expense of renting.
More severe damage could mean a full replacement, which may not be covered by warranty or insurance. And, depending on the failure, crew could be injured during the process from hot liquids, flying parts and more. You are savvy enough to know that skipping the required upkeep might save money in the short term, but that inefficient maintenance will most likely catch up with you.
Overservicing your construction equipment is as expensive for your budget as underservicing it. Bringing in assets once a month for maintenance is inefficient. Going by calendar days versus actual utilization typically results in a greater expense and waste of parts and technician hours, all of which may not be needed.
Traditional Maintenance
Let’s consider two contractors. Contractor A is more traditional, preferring spreadsheets, and the other, Contractor B, has decided to implement telematics to manage its mixed fleets. Both firms are midsized companies, with a few jobsites spread across a regional area around headquarters. Contractor A has each site project manager update their equipment utilization logs manually. A crewmember or two is sent to retrieve the information, such as engine hours. Visual inspections are also conducted to uncover any issues with treads, tires or leaks. Sometimes, one or two assets are missed if they are tucked away, the crew person is rushed or if there is a distraction. The contractor schedules maintenance based on this data with his/her in-house technician or outside repair shop. It’s a good system. However, there are more unexpected breakdowns than the firm would like. The technician also notes that an air filter, hydraulic fluid or the oil is only partially used, and the equipment doesn’t really need to be serviced yet. The total cost of ownership has increased for Contractor A due to emergency repairs, wasted resources and investment in excess inventory.
JIT or Predictive Maintenance
Contractor B installed telematics devices in his vehicles and equipment, which transmit data to the software. Project managers are now able to locate all of their assets on an Environmental Systems Research Institute (Esri) map and view the utilization data. The information is easy to access remotely or in the office. Through intelligent reporting and a variety of alerts, this contractor is working smart off intelligence and insight that historically was not applied to this industry.
The contractor has started developing a just-in-time, predictive maintenance program based on their project managers’, crews’ and telematics solution’s inputs. It allows any upkeep or repairs to be forecasted and scheduled. Engine hour utilization and mileage are tracked depending on the asset type.
When the recommended threshold is reached, an alert is sent to the assigned person or team. The project manager coordinates with the other jobsites to move underutilized inventory around in order to keep the project on track. The technician schedules time with the in-house or outside shop. It is a seamless process that doesn’t waste time or resources.
With access to the Controller Area Network (CAN) bus, additional data can be retrieved. These measurements are available at the equipment level and across the entire fleet. Contractor B is able to see actual activity levels and verify expected performance. Most asset management software provides dashboard monitor tools to give a real-time display of these and many other performance metrics. Notifications are sent when a diagnostic indicator occurs. This information lets you get ahead of a potential problem. Again, the contractor is able to rebalance inventory to manage the repair.
Contractor B has seen reduced equipment costs, as the number of unexpected breakdowns has decreased. The company is also able to order parts and supplies economically and keep less inventory on hand. The telematics data has let the company right-size their inventory and improve job costing.
There are hard cost and crew benefits from a just-in-time system. Access to real-time utilization from a telematics solution allows contractors and rental equipment owners to manage their vehicles and equipment maintenance more efficiently. Predictive and preventive maintenance is generally cheaper than emergency fixes. Technicians, whether in-house or off-site, are less rushed, which can reduce errors. Improved mixed fleet visibility saves crew time from manually locating and recording usage.