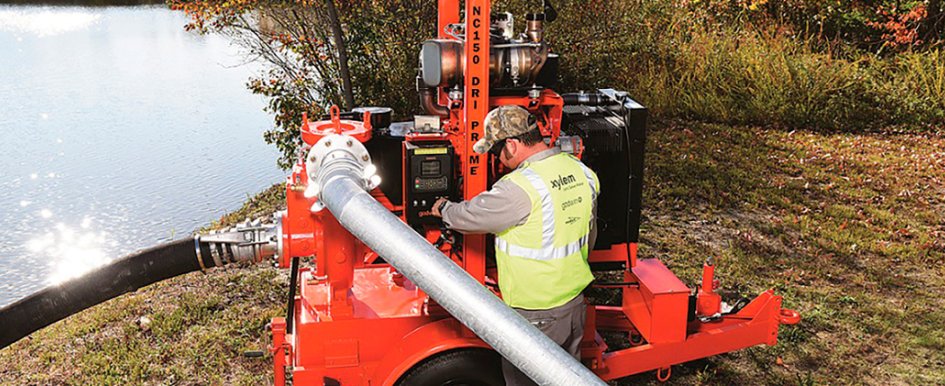
Off-road, diesel-driven equipment covers multiple groups, including construction equipment, generators and diesel-driven pumps. The biggest effect of the Clean Air Act on off-road diesel engines has been the reduction of nitrogen oxides (NOx) and particulate matter (PM). Since 1990, the EPA has required manufacturers to reduce emissions levels in tiers. These tiers have become progressively more stringent, with the most recent tier standard, Tier 4, aiming to reduce diesel engines emissions from the previous Tier 3 standard by 90 percent for PM and 50 percent for NOx.
A 90-percent reduction in emissions requires a significant change in the engine. For this reason, the new Tier 4 Final engines are generally larger and more costly than their Tier 3 precursors. Tier 4 Final engine models that were mechanical for previous tiers are now electronic and have more components, including valves, sensors, wires, a higher functioning engine control unit (ECU) (for engines that were already electronic), diesel particulate filters (DPF), selective catalytic reduction (SCR) and diesel oxidative catalyst (DOC)—all of which increase the cost of the diesel engine and the cost of a diesel-driven pump.
With higher capital costs, a more narrow operating range for equipment and potentially higher operating costs, Tier 4 Final emissions requirements for diesel pumps can appear complicated to navigate. However, a little planning and an understanding of the impact that Tier 4 can have on engine performance can ensure that construction businesses comply with legislation without compromising pump performance or unduly impacting their bottom lines.
Emission Treatment Strategies
There are two different strategies for treating engine emissions: in-cylinder treatment and aftertreatment. In-cylinder treatment works by preventing PM or NOx from forming by changing combustion parameters, such as the fuel injection rate and timing, cylinder temperature and pressure and the oxygen concentration. Aftertreatment works by treating the exhaust coming out of the cylinders to remove NOx or PM before the exhaust is vented into the atmosphere.
Field and application testing have shown that for most pumping jobs, engine models that utilize in-cylinder methods to meet emissions requirements have fewer maintenance problems and less downtime. In-cylinder methods also tend to be less expensive, which results in a less costly diesel-driven pump.
Tier 4 Engine Performance Expectations
Pump performance, a factor of the mechanical design of the pump-end, does not change. Engine performance is definitely affected by Tier 4 regulations, though. Tier 4 Final engines can be used in all pumping applications, as long as the pump is sized and maintained properly. The parameters for selecting a pump do not change for Tier 4 Final units—what has been constricted is the operating range for the pump. The following are some items to consider when sizing applications with interim and Tier 4 Final engines.
Sufficient Loads
Wet stacking occurs when an engine has unburnt fuel exiting the cylinders. Generally, this happens when the engine is not under sufficient load. While wet stacking was a problem with previous tier engines, operating a Tier 4 engine under a low load can cause significant damage and maintenance issues. By maintaining a higher load on the engine, this problem can be alleviated.
Pumping applications with large variations of flow through the course of the day, or the duration of the project, may require creative pumping solutions. These solutions will ensure the requirements of the job are met while still maintaining the correct load on the engines. Your local pumping solution provider can support your pumping needs with a comprehensive design that takes into account the requirements of Tier 4 engine operation.
Avoid Short Cycling
Short cycling diesel engines can create problems for engines using aftertreatment. If the engine is using a diesel particulate filter (DPF) to meet PM emissions requirements, the engine will need to operate long enough to ensure it has a chance to clean the filter in order to prevent clogging. This cleaning process is known as regeneration. Manual or automatic operation can interrupt the regeneration cycle and allow buildup to occur in the filter. If the cycle is interrupted too many times, the filter will soot up to a level where an automatic shutdown will occur.
Watch the Ambient Temperature
Low ambient temperature can cause operational problems for engines with aftertreatment. Engines that include DPF need to meet a certain temperature to be able to regenerate and burn off accumulated soot. If the ambient temperature is too low, the engine may have trouble reaching this temperature. High levels of accumulated soot will eventually shut down the engine and require manual intervention.
With Tier 4 Final engines coming to market, more pumps will have selective catalytic reduction (SCR), which requires the use of diesel exhaust fluid (DEF). DEF fluid for diesel pumps is stored in a tank located on the skid base. If the DEF in the tank freezes, the engine can only run for a short period of time while the tank thaws out. If the DEF does not thaw before the given time period, the engine will shut down and require a manual restart to resume the thawing process.
Similarly, high ambient temperature can cause some operational challenges. DEF begins to decompose at 84 degrees. If the DEF decomposes too much, the engine will not meet the required NOx levels and will shut down on an emissions non-compliance error.
Alternative Strategies
When purchasing a new diesel-driven pump this year, there is the option of using an engine with aftertreatment or an engine that uses in-cylinder methods to meet emission requirements. However, there are some additional considerations that can help reduce the cost of new equipment.
Rental Options
As new Tier 4 Final engines have led to an increase in the cost of diesel-driven pumps, renting equipment is an attractive option. Renting pumps allows work to be done without expensive capital costs, and it gives project managers more flexibility to change equipment during the course of the project. An additional benefit of renting equipment is direct access to expert advice, service and maintenance throughout the course of the project.
Electric Options
Not only are electric pumps less expensive initially, but if electric power is available at the jobsite, both equipment and operating expenses can sometimes be reduced by using electric pumps. Variable frequency drives (VFDs) can also be utilized to make electric options more economical by reducing amperage draw during low-flow conditions.
Meeting Tier 4 Final requirements may seem difficult, but it just requires a re-evaluation of priorities. Before, it may have made sense to purchase a diesel-driven pump for a temporary project, but with the increase in the capital and maintenance of these pumps, the better option may be rental.