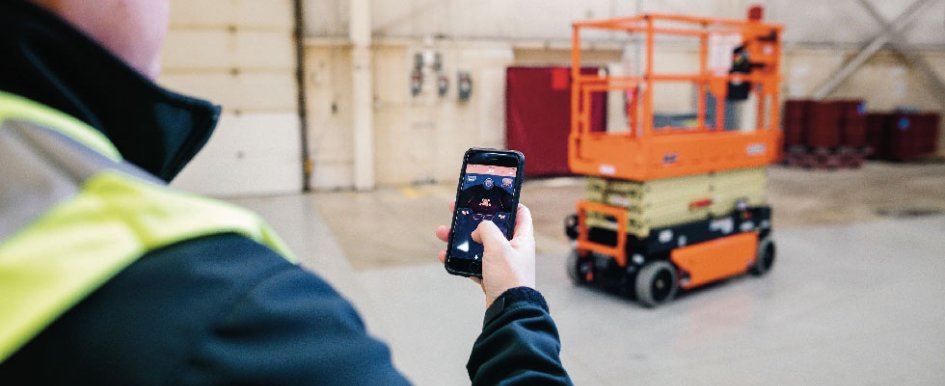
Your biggest access rental equipment problems are about to be solved, according to JLG President Frank Nerenhausen. Nerenhausen says that scissor lifts, boom lifts and telehandlers are all set to go through a dramatic transformation.
By listening to the industry’s unmet needs — and then combining innovation with technology — the answers to users’ most considerable challenges are now within reach.
Because of this, the next life cycle of access equipment is going to look and operate differently — more than just the usual spec updates.
“We see that there is a need for innovation that goes beyond the incremental,” said Nerenhausen. “We need to make workers more productive and safer on their jobsites.”
Here are five trends that Nerenhausen says will reinvent how you work at-height and move materials in the future, along with specific examples about how those changes can impact you today.
1. Going Beyond Compliance
Scissor and boom lifts, now known as mobile elevated work platforms (MEWP), were already getting a makeover due to the updated design requirements of the new ANSI A92 suite of standards.
To achieve compliance, MEWPs produced after June 1, 2020, must include features intended to improve safety, such as platform load sensing, tilt sensing, higher railings and more.
According to Nerehsusen, this provided the opportunity to reexamine MEWP designs from the operator’s point of view and introduce additional features to help users more easily navigate the required changes to the machines. If you’re not familiar with the ANSI A92 standards, you may not know that the operation of new MEWPs may be prevented if the platforms are overloaded, or tilt levels are exceeded.
But how are you going to know if that’s the reason your MEWP isn’t working right? New advances in technology provide live feedback for operators.
According to Rafael Nunez, senior product manager for scissor and vertical lifts at JLG, there are equipment displays on the market today that provide important information about the machine like side-to-side tilt, front-to-back tilt, how much weight is on the platform, the current height of the platform and the maximum height you can raise your MEWP by taking those factors into account.
“With this type of display on the machine, you’ll be able to see if you should take a little bit less material with you, or if you need to get to a spot that’s a little bit more level on the jobsite, so that you can get the full height,” said Nunez.
2. Crossover of Safety Technologies
Outside industries, including the defense, public safety and on-highway vehicle markets are influencing the next set of safety features for access equipment. “What happens is you get spin-off technologies that we can apply in the access industry,” said Rob Messina, senior vice president of global product development at JLG.
Messina says technologies in those industries, such as object detection sensors, back-up cameras and seat belt/lanyard attachment verification systems, all have the potential to be adopted and become standard for MEWPs and telehandlers in the near term. “These are technologies that progressively improve the machine’s ability to provide safe solutions,” said Messina.
For example, the enhanced object detection systems will produce an
alarm that will increase in frequency and reduce the speed of the machine as
you get closer to an object, eventually stopping the machine once you’re
too close.
At that point, the operator must manually override the system to continue maneuvering the platform.
“You’re now inching toward that object instead of coming in fast,” said Nunez. It’s important to note that the sensors only look in the direction of travel and the warning zones are scalable based on joystick input.
3. More Steps Toward Connected Jobsites
Hearing about the autonomous work sites of the future where machines communicate to each other and the people that manage them can sound like some far-off concept that’s still years off.
Is your electric scissor lift ready for a full shift’s work? It’s often hard to tell before the machine quits. But with advanced battery monitoring system technologies for scissor lifts, now you can view important battery status information including current state of charge, charging cycle history and when maintenance needs to be performed via an app on your smartphone.
“This allows users to make fleet-level decisions without the need to touch individual machines to collect data on a one-to-one basis,” said Stefan Eschelman, JLG’s senior product engineer.
Mobile control apps can tell you if your scissor lifts are ready to operate or if there are problems that need to be addressed. And in some cases, these apps will also allow operators to drive scissor lifts remotely. “This is a simple step toward changing expectations of how users can interact with our machines without overburdening them with the obscure promise of ‘connectivity,’” said Eschelman.
Remote diagnosis of problems is also possible for CAN bus-equipped MEWPs and telehandlers. For example, when you call your rental company or dealer about an equipment failure, the service tech can check the machine’s performance and review fault codes using a remote analyzer reader through the machine’s telematics system. This enables the service tech to make sure they have the right parts and tools to get the machine up and running quickly when they come out to your site.
4. Driving Designs Through User Feedback
In the past, new MEWPs and telehandlers were primarily designed with an emphasis on developing best-in-class specs. That’s all changing, says Shashank Bhatia, JLG’s senior director of global product development. “We have now shifted and put a lot of emphasis on getting customer-based input,” said Bhatia. “We call this customer-inspired innovation.”
According to Bhatia, new access equipment designs will give more attention to the needs of the user and not just the rental company or dealer.
Typically, if you needed to move materials higher than six stories, you had no choice but to invest in a crane. But crane rentals are expensive, costly to transport and assemble and they require a certified crane operator.
John Boehme, senior product manager for telehandlers, says that users have been requesting a telehandler that could extend higher and reach farther to serve as a crane alternative. With that in mind, OEMs now offer telehandlers that can lift materials eight stories or higher.
And unlike a crane, these higher-reaching telehandlers can lift up-and-in to place materials exactly where they’re needed without requiring the use of a forklift to reposition the pallet. “With a high-reach telehandler, you can reach 60 feet inside a structure,” said Boehme, “and, you’re able to have better precision placement.” If materials or an HVAC system need to be placed on top of a building, operators can control the boom remotely from the roof.
Also, no specialized trucks or trailers are needed to get these types of telehandlers to the jobsite — they can be transported on a common step-deck trailer, which can get around a busy site with ease.
5. Providing the Total Package
In the end, the defining moment of the access equipment industry will be about more than just offering the product. It will be about developing comprehensive resources for access equipment owners, operators and service providers that fix problems before they occur.
“Life-cycle management really is what we’re driving toward,” said Nerenhausen. “Where you’re going to see this evolve is through key sensors that provide additional pieces of feedback and information that can be used to more quickly diagnose a symptom,” said Messina.
The goal is to continue to make it easier and safer for access equipment users to get their jobs done.
According to Messiance, “Through
the next fleet cycle, you’re going to see a lot of change across the industry in the next five years.”
For example, you’re on a large site, ready to work, trying to figure out which MEWP you could fit through a narrow entryway and still give you the access you need you could go locate one of the machines on rent and try it out. But this will take time and perhaps even multiple machines until you find the appropriate one for the task. Alternatively, you could hold up your smartphone and quickly see which machine you need for yourself with augmented reality (AR) apps.
“AR gives you the power to visualize equipment information, when and where they need it,” said Ara Eckel, JLG’s senior product marketing manager for connected solutions. For example, with an AR app users can place a scaled 3D machine in the actual work environment captured in the app. They can raise and lower the machines and move them through doorways and around obstacles. These apps can also provide inspection assistance.
“You hold the app on your phone up over your machine, and it’s going to put pins over all the spots where you need to perform your annual inspection,” said Eckel. “As you click on those pins, you can now take a look at the information in the pin drops and actually perform the inspection in a step-by-step way.”
Looking Ahead
Technological advancements are expected to transform the access industry to maximize productivity and enhance safety. As demand for new technology increases, MEWP OEMs must be ready to respond with innovative ways for equipment owners and operators to interact with and operate these machines.