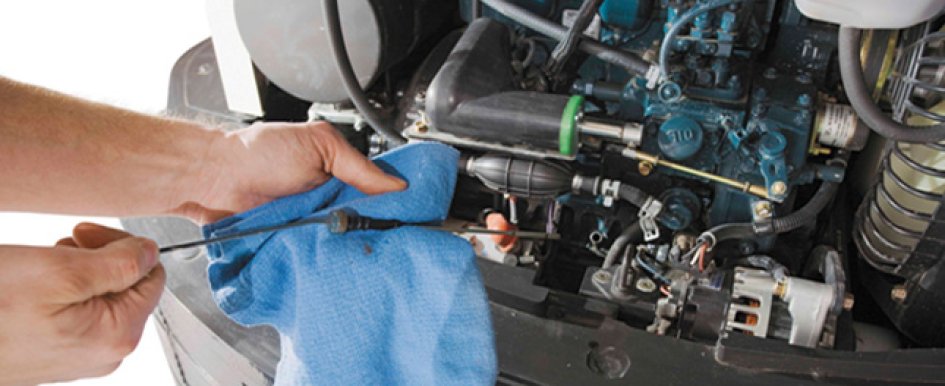
As a business owner, you know the revenue needle stops moving during unexpected downtime. In fact, troubleshooting poor equipment performance or outright system and component failure can be one of your greatest frustrations. To make matters worse, you may not have adequate service training or access to an on-site mechanic for the repairs that will get your loader or excavator up and running again.
That’s why preventive maintenance is so critical to your operation. Although wear issues will develop with any equipment over time, your answer to a simple question will largely determine your outcomes: Do you want to be proactive and productive or reactive and face asset downtime?
Your ability to protect your assets and prolong their useful lives is largely dependent on your commitment to develop a consistent maintenance plan that covers three key areas: properly analyzing business needs with machine capabilities, following recommended intervals and anticipating wear, and expanding one’s knowledge about maintenance trends. Owners and operators who focus on these items will have the best chance of maintaining a well-conditioned fleet.
Assess Capabilities
Industry experts agree that the first step toward developing a proactive approach to maintenance is analyzing how you will use a compact excavator or a loader and assessing specific capacity ranges. As an example, for excavators, how deep will you dig and in what ground conditions? When looking at loaders, you need to know how much weight will routinely be lifted, whether you will be loading into tall-sided hoppers or trucks and what size restrictions will be on the jobsite.
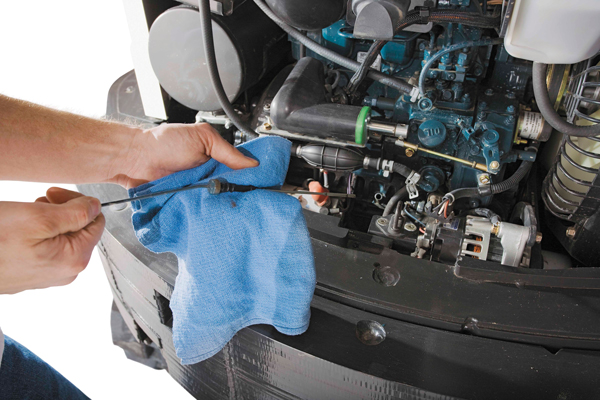
If your equipment is allocated to jobs it is not designed to handle, you are more likely to face an underperforming machine that may need frequent repairs. For example, some construction applications—such as excavating in hard ground or loading, pushing and leveling heavy aggregate—can be especially hard on equipment, so you must follow manufacturers’ rated capacity guidelines to acquire the correct size machine.
Anticipate Wear
Familiarize yourself with the maintenance section of a machine’s operation and maintenance manual. If you don’t have one, most manufacturers have created electronic versions that can be ordered. You’ll find that maintenance intervals commonly start with basic procedures at 8 to 10 hours, followed by most other procedures at 50, 100, 250, 500 and 1,000 hours.
You should diligently follow routine daily service intervals for fluids, lubricants and filters during normal working conditions and temperatures. As temperatures drop, machine service requirements can change. In cold weather, items that you should adjust and monitor to meet winter weather include fuel, tire pressure, block heaters, battery and cold-climate comfort features such as heating and defrosting systems. Equally important is an engine oil viscosity that matches the outside operating temperatures and a low- temperature grease for proper lubrication on pivot points. Hydraulic oil filters should be changed as they may have collected water and debris during warmer months.
No matter how faithful you are with your preventive maintenance, you still need to prepare for wear. As you accumulate hours on any compact equipment, you’re going to wear out tires, tracks, cutting edges and pins. It’s not a question of whether those items will wear, but rather when it’s going to happen. Your ability to anticipate and minimize your downtime depends entirely on how proactive you’ve been with taking care of your machine.
Wear typically occurs on ground- engaging parts, which should be replaced when productivity starts to diminish. Tires on skid-steer loaders will last approximately 600 to 800 hours if working mostly on dirt at proper inflation levels. Tire life may be reduced if frequently operating on asphalt or concrete surfaces.
Mini excavators and compact track loaders have rubber tracks that wear and need to be maintained. Some owner- operators can reach 1,200 to 1,600 hours on loader and excavator tracks if the machines are operated properly, kept clean and tensioned when required. General contracting, heavy excavating and rental applications routinely experience fewer hours of wear on tires and tracks than owner-operators.
Visual checks of attachment components such as cutting edges, bucket teeth and hoses can help determine if wear is developing or damage has occurred.
Upgrade Knowledge
In many ways, compact equipment designs are beginning to parallel the automotive industry with emissions controls and diagnostic capabilities. Owners should become more knowledgeable about emissions regulations and the associated maintenance requirements.
Today’s machines are equipped with various levels of emissions-compliant engines that require a general understanding of interim Tier 4 and Tier 4 technologies and their needs. New machines have different lubricant requirements and other components such as high- pressure common-rail fuel injection systems, diesel oxidation catalysts and diesel particulate filters that affect maintenance specifications.
More sophisticated diagnostics systems have been developed to provide faster analysis of service-related items. Not unlike the automotive industry, many compact machines also have on-board diagnostic storage of critical information. Service codes displayed in the machine can indicate issues, such as battery voltages, oil pressure and temperature, engine speed and engine coolant, which can be helpful to communicate to a mechanic back at the shop.
It’s been said that an ounce of prevention is worth a pound of cure. The more effort you put into evaluating machine capabilities, following recommended maintenance intervals, anticipating wear rates and grasping new trends up front, the more uptime you’ll experience.
Preventive Maintenance Checklist
To reduce troubleshooting in the field and avoid excessive wear and early failures, maintenance work should be performed at regular intervals. Your best resource for proper procedures and intervals is the operation and maintenance manual that is supplied with your machines. For a quick refresher on typical recommended intervals in the industry for compact excavators and loaders, keep this checklist handy.
Daily maintenance
- Check fluid levels and air filter condition.
- Grease pivot pins.
- Check tire air pressure, or inspect and adjust track tension.
Weekly maintenance
- Check battery cables, connections and electrolyte levels.
- Examine hydraulic hoses and tube lines.
- Assess the condition of belts.
- Inspect parking brake, wheel nuts, foot pedals, hand controls and steering levers or joysticks.
- Check final drive transmission oil levels (chaincase/motors).
- Grease swing circle and pinion (mini excavators).
As scheduled per maintenance manual
- Replace fuel filter, engine oil and filter.
- Clean reservoir and reservoir breather, and replace hydraulic oil and case drain filters.
- Replace the lubricant in chaincase/final drive motors.
- Adjust the engine valve clearance.
- Drain and flush cooling system, and replace coolant.