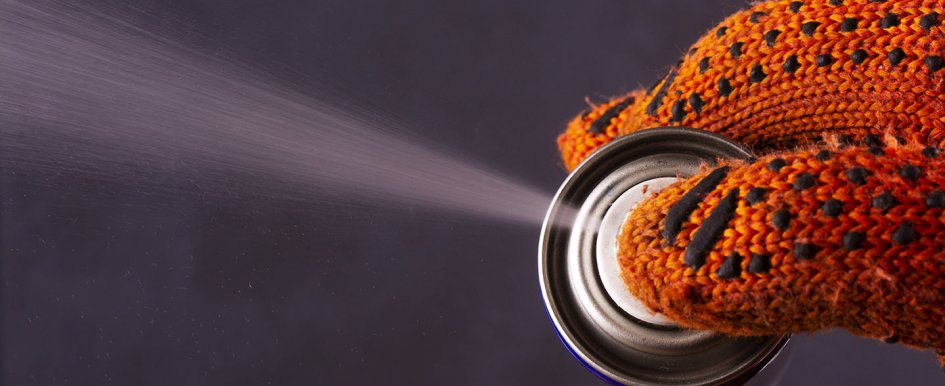
On a daily basis, construction professionals face wet, dirty, dusty and muddy environments. These conditions add to the challenge of maintenance or repair jobs. Tools and equipment are necessary for these jobs, but they are much less useful when rusted, stuck or simply not operating at peak performance. Being proactive and using the appropriate lubricant or maintenance product can save your business time and money in the long run.
A lubricant’s main purpose is to reduce friction, heat and wear when used as a film between solid surfaces like metals, plastics, wood and rubber. Lubricants are seldom pure oils and usually contain additives that will assist lubrication, improve wear and heat resistance, displace moisture and protect against corrosion. Lubricants vary in viscosity — their thickness and resistance to flow. Thinner oils or liquids tend to move and disappear more quickly than thicker oils, but they also are able to carry away particles and contaminants. Heavy oils or greases are usually built to stay in place longer and withstand a heavier workload.
In most instances, you will want a lubricant that’s long lasting, because it will help reduce maintenance time, allowing you more time to complete jobs. If you’re working with metal, you will also want to protect those parts from rust. When your equipment is rust-free and running smoothly, you can concentrate on your clients’ projects.
To choose the best type of lubricant, consider the surface materials, environmental conditions and performance requirements. You should also consult that equipment’s maintenance instructions, warranty or manual before applying lubricants.
So, what’s the best product to use for each surface and condition? Consider these tips for choosing the right lubricant.
Metal-on-Metal
Oil-based products are best for providing a lubricating film that prevents direct contact of moving metal parts. Oils can flow freely, allowing for uniform protection from friction. For long-lasting lubrication, use multi-purpose oil that further protects the surfaces and that won’t break down easily.
For parts that aren’t moving but should — like a frozen nut or bolt — a penetrant can be used. Penetrants are thin, oil-based materials that will quickly seep into narrow spaces like threads on bolts or screws to provide a lubricating film that helps release the stuck piece.
Greases can be used for metal-on-metal applications that require heavy-duty lubrication and protection against rust. Spray products like white lithium grease provide an even layer that sets dry for a thick, protective coating that won’t wash off, melt, freeze or run in any weather. This product is best used on parts like auto hinges, gears, sprockets and pulleys that are exposed to the elements.
Metal-on-Plastic
Lubricants with silicone or PTFE (polytetrafluoroethylene) are best for use on plastic surfaces. PTFE is hydrophobic, meaning it repels water, so lubricants containing it are effective in damp conditions. Silicone lubricants make surfaces ultra-slippery while repelling water. They’re safe to use on rubber, plastic, wood and metal. While some lubricants can be used around painting operations, silicone-based lubricants should not, so check the product’s label.
Plastic-on-Plastic
Silicone or PTFE products are suitable for plastic-to-plastic lubrication, but the silicone will form a thicker, wetter layer that may collect dust and dirt. PTFE will have a thinner, yet harder layer that will not attract dust or absorb grime.
Metal-on-Rubber
PTFE products are best for lubrication of rubber. They provide a thin, hard layer that protects best against the accumulation of dust and dirt.
Removing Rust
Non-acid rust remover products will safely remove rust from metal tools and equipment. They do not contain harsh acids that will damage surfaces, but instead are based on chelation chemistry. The chelates are materials that react with rust and only rust. These products may take a little longer to work but will not harm the surrounding parts, trim, gaskets or painted surfaces and are safer because they maintain a neutral pH. Once the rust is removed, you can quickly apply a film of lubricant or corrosion inhibitor.
Fast Action
It’s going to happen — tools, parts and equipment will become caked with dirt, rust and moisture on the job. But in a time when clients seem to want everything done instantaneously, quick service is critical. Maintaining rust-free equipment that operates efficiently, being able to quickly free up stuck parts and having the ability to make quick repairs at the jobsite will keep clients satisfied with your services.
Abraham Lincoln once said that if he had 6 hours to cut down a tree, he would spend the first 4 sharpening the ax. Time is money and making a small investment in the correct products will help you get your projects done on time and on budget.
Regular maintenance — like keeping things clean and organized during the course of construction — is challenging, but it’s easier than you think. Lubricant products fit easily into your work truck or toolbox and taking the time to spray a piece of working equipment to maintain its condition requires much less effort than repairing it if it’s broken. You can’t afford to buy new tools just because the ones you own have been neglected. If you take care of your tools, they will take care of you.