Heavy equipment has been powered by hydraulics for a century. Within all of that steel piston power, one weak link exists: the rubber hose. One burst hydraulic hose can stop even the biggest earthmover.
To reduce downtime related to fluid connector components, contractors should make sure that operators use maintenance management software, acquire on-site assembly tools for maintenance, utilize portable location-based services and ensure hose compatibility.
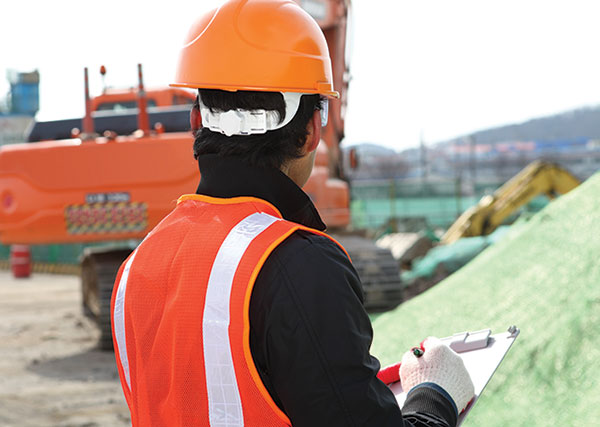
Maintenance Software
Using maintenance management software can help operators avoid the “fix-when-fail” strategy. This type of software provides a product’s age, life cycle capacity and replacement timeline. Asset documentation platforms integrate tracking and maintenance records to drive greater operational efficiency by providing the operator with an easy-to-navigate database of components for planned inspections or failures.
Web- or mobile-based maintenance platforms enable users to quickly recall assembly component details, regardless of where they were made. Instead of taking a faulty part to a store for identification, operators can immediately identify the part by scanning or typing an assigned identification number into the documentation platform’s database, thus saving a considerable amount of time and resources. This type of platform is designed to help customers reduce downtime through increased speed, timing and accuracy of necessary repairs.
On-Site Hose Crimpers
Having a portable or bench-mounted crimper on-site enables anyone to produce factory-quality hose assemblies without driving to a local hose assembly fabricator. Because these crimpers often range in price from $1,500 to $7,000, an on-site crimper isn’t a feasible investment for every operation. A business owner must first determine how much money an on-site hose crimper can save the operation in order to decide if the benefits outweigh the costs.
Local hose distributors can use a formula that compiles data about business operations and equipment to help customers decide whether investing in a crimper or using in-store services will produce the best return on investment (ROI). In order to effectively calculate ROI, the following information is needed:
- Number of hose assemblies replaced or purchased annually
- Total hourly cost of the maintenance personnel (including salary, benefits and all costs associated with employment)
- Total hourly cost of the individual who leaves the facility to obtain a replacement hose (driver or parts runner)
- Distance to the nearest hose fabricator
- Transportation cost per mile
- Hourly cost of equipment downtime; this is usually the highest cost.
- Value of recommended stock order
- Price of the crimper and any accessories
The distributor will also consider every aspect of off-site fabrication, including locating a driver/runner; providing instruction/details; traveling to a hose supplier/fabricator; waiting in line for service; discussing needs/application with a customer service representative; waiting time before hose fabrication begins; fabrication of the hose assembly; paperwork/billing and returning to the shop.
The dollars and hours quickly stack up using off-site fabrication. Hose distributors and equipment operators can evaluate this process to determine if an on-site crimper is needed based on the estimated savings per hose in a given time frame compared to cost of the crimper.
Mobile Work Containers
Mobile work containers are ideal for remote or extreme locations. These containers are fully customizable mobile work spaces that are delivered directly to a jobsite. They can provide the technology, equipment and inventory needed for remote fabrication of hose and tube assemblies, including hose crimpers. If a piece of equipment fails, it can quickly be replaced with a part from the mobile container. This is critical for jobsites located hours away from any type of distributor.
The Right Hose
The adage “an ounce of prevention is worth a pound of cure” has merit when it comes to hydraulic hoses. Prevention means making sure you buy the right hose for the application, which requires selecting a hose with the right internal diameter to ensure proper flow velocity. A flow that is too slow results in sluggish performance, and a flow that is too high can cause pressure drops, leaks and system damage.
The hose pressure rating should be equal to or greater than the maximum system pressure and any surge pressures or peak transient pressures in the system. The temperature rating should meet or exceed the higher of the media or ambient temperature of your application. And, the hose must be compatible with the medium being conveyed. Compatibility includes the inner tube, cover, hose fittings and O-rings.
Owners should ask these questions when choosing the best hose for an application:
- What type of equipment will the hose be used on?
- What environmental factors will the hose be exposed to?
- Are mechanical loads applied to the assembly?
- Will the routing be confined?
- Is there a need to use field attachable fittings?
- Will the assembly be subjected to abrasion?
Specific applications often require specific hoses. For example, where hoses will encounter abrasive surfaces, use tough, abrasion-resistant hoses. When space is tight, consider spiral hoses with smaller outside diameters and bend radii.
Whatever the application may be, remember that the cost of running a business includes more than machine components alone. Business owners should understand all cost-saving opportunities and select the options that will most effectively manage equipment, associates and business operations.