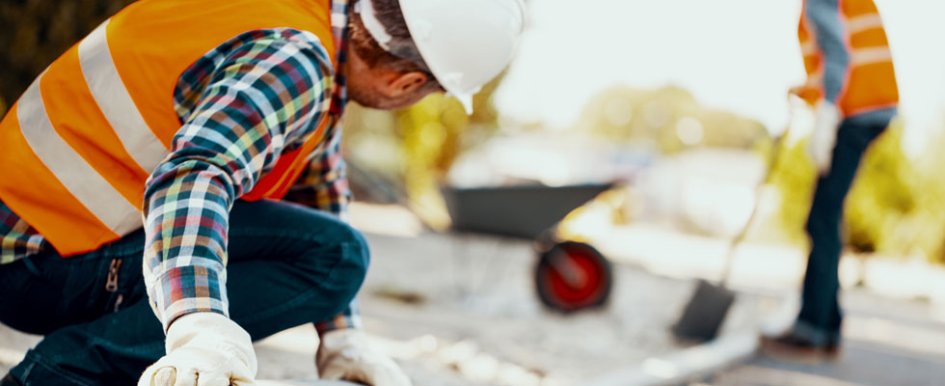
Construction work is no easy task. Not only can the physical work challenge both the body and mind, but jobsites are often filled with hazards that can be exacerbated when crews work long hours under tight deadlines and with limited workers.
Common injuries include overexertion, falls, slips and trips, as well as exposure to harmful substances or environments. At the same time, maintaining a safe work environment is critical to caring for a jobsite’s most valuable asset — its employees — while minimizing risk and increasing efficiency. More than ever, safety is top of mind not only for employers but employees. This is especially true for younger generations.
According to the American Psychological Association, millennials reported personal safety is the leading cause of stress in the workplace. This group, which now makes up 35% of the American workforce, is becoming a driving force in increasing workplace safety across industries. In addition, younger workers are more likely to be injured on the job than older adults. At a time when the construction industry is facing a labor shortfall, creating and keeping safe work environments is critical to attracting and retaining valuable employees.
For employers, safe work environments create not only more productivity but also benefit the bottom line. Total workplace injuries exceed $170 billion each year, according to the National Safety Council. In addition, OSHA estimates that construction companies save $4 to $6 for every $1 invested in safety programs. So where do you start? Following local and national laws and regulations is just the beginning. Consider these tips to make operations safer and more efficient, while demonstrating commitment to keeping workers safe.
1. Foster a Safety-First Culture
Doing this does not happen overnight and creating a safety-first culture is about more than emphasizing protocol and checklists. Instead, it’s about consistently talking about and prioritizing safety at every level, starting with senior leadership and extending to middle management, crew supervisors and every person on a jobsite. Facilitate ongoing conversations about safety, its importance and encourage employees to voice safety concerns with supervisors. Empower crews to raise red flags about safety, vulnerabilities and risks. Those who help improve safety should be applauded and recognized for their efforts.
2. Clean & Maintain Equipment & Tools
Properly cleaning and maintaining equipment and tools can prevent accidents and injuries and avoid costly repairs. One way to do this is by keeping a cleaning and maintenance schedule. Create a log of all equipment in use, including key points in need of inspection. The log should also track when inspections are done, who performed the inspection and how equipment faired on all inspection points. Outdoor equipment is more susceptible to environmental damage and should be inspected regularly. It doesn’t take long for rust to develop, especially for equipment exposed to the elements, so it’s important to prevent it from happening or take care of it as soon as it’s found.
3. Ensure Crews Are Equipped With the Proper PPE
The right personal protective equipment (PPE) can be the difference between a minor injury and something far more serious. Helmets, ear protection, safety goggles, knee pads and high visibility jackets are just a few of the must-haves for many jobsites. Some jobsites may have specific hazards that need to be accounted for. Consider the jobs being done, and what PPE is appropriate.
4. Choose the Right Products for Lubricating, Cleaning & More
A little product research can go a long way. Choose products that are safer for people and the environment. Search for products formulated with clean solvents and oils that have been treated to remove harmful chemical contaminants.
5. Prioritize Mentorship
According to the Bureau of Labor Statistics, more than 60% of construction accidents occur within an employee’s first year of work. Being proactive and assigning new workers a mentor can help ease the transition and place emphasis on important safety practices and procedures. An extra set of eyes on new employees can also ensure proper education to prevent accidents before they happen. On-the-ground mentors act as a safety resource especially for the younger generation of trade professionals to minimize risk and increase efficiency.
6. Never Stop Learning
Business owners can also benefit by encouraging crews to constantly grow their knowledge and skill sets. One simple way to do this is to look for online training resources. Explore programs where participants can learn the science behind safe products, what to look for when choosing maintenance products, and how to take precautions around harmful chemicals. Check out the safety section of the Associated Builders and Contractors website for a complete list of safety materials on everything from fall protection and eye safety to safe lifting practices and ladder safety.
With more than 700,000 employers and more than 7 million employees, the construction industry is one of the largest contributors to the U.S. economy and keeping employees safe is critical. This is especially true during a time when the industry is facing a shortage of professionals and attracting a new generation and retaining talent is more important than ever.