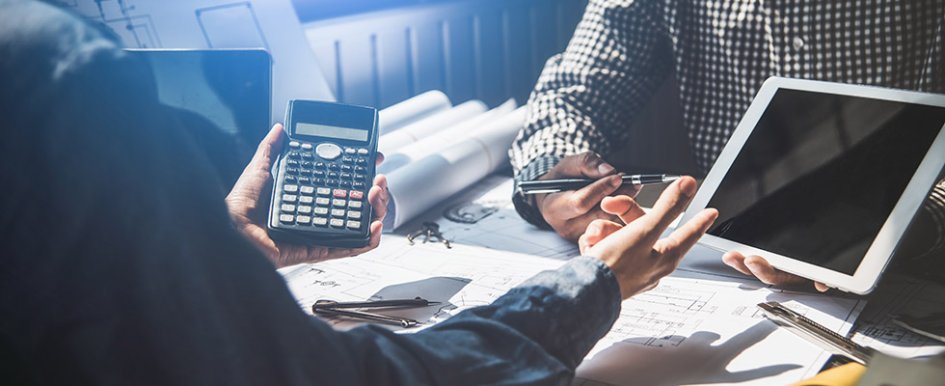
As we navigate the complexities of the construction industry in 2024, the ability to provide accurate cost estimations remains the cornerstone of a contractor’s success. The art of cost estimation is fraught with complexities and often undermined by factors that were either overlooked or impossible to predict. Nonetheless, the importance of developing a precise cost estimate cannot be overstated. It is the foundation upon which a profitable project is built, serving as a road map for resource allocation, risk assessment and financial planning. Contractors face the dual challenge of maintaining competitive pricing while ensuring profitability. As we navigate through 2024, contractors should consider the critical components of labor, material and indirect costs, exploring the challenges they present and the strategies to formulate estimates that pave the way for successful and profitable projects.
Labor Costs
Labor costs often represent one of the most significant expenses in construction projects. Estimating them accurately is challenging due to skilled labor shortages, wage fluctuations and varying productivity levels. These issues can lead to either overestimating, which makes bids less competitive, or underestimating, which eats into profits. The scarcity of skilled workers is pushing wages up, and contractors must find ways to prepare for these changes to remain competitive and profitable. The following list shows challenges contractors face and need to consider when estimating
labor costs.
- Skilled labor shortage — This is not new to contractors anymore. The lack of skilled labor has been an ongoing issue and will always be the biggest challenge. The construction industry faces a severe shortage of skilled labor due to an aging workforce and fewer young people entering the trades. This shortage can increase wages as contractors compete to attract and retain qualified workers, driving up labor costs. Due to the skilled labor shortage, less experienced laborers could be put on a job, resulting in more labor hours. The contractors should review skilled laborers’ abilities and how they would impact each project.
- Increased demand for construction — With a growing population and the need for infrastructure development, there is an increased demand for construction services. This demand can create a competitive labor market in which wages are driven higher, especially for specialized skills in short supply.
- Productivity challenges — Despite technological advances, construction productivity has not increased as quickly as other industries. The physical nature of the work, the complexity of projects and the variability of site conditions can limit productivity gains, meaning that more labor hours may be required to complete a project, inflating costs.
- Regulatory changes — Governments may introduce new regulations regarding wages, benefits and working conditions, which can impact labor costs. Changes to minimum wage laws, health and safety requirements, or apprenticeship programs can increase the cost of labor.
- Inflationary pressures — General inflation affects the cost of living, which puts upward pressure on wages as workers seek to maintain their purchasing power. Many hope that inflation will be stopped or slow down in 2024, but the reality is that contractors must factor these pressures into their cost estimations to ensure that wage estimates remain realistic over the project’s duration.
Wages are expected to experience upward pressure in 2024, and the skilled labor shortage will not be soon resolved. Contractors should review and evaluate their current labor resources quantitatively and qualitatively and incorporate them into cost estimates.
Material Costs
In the past few years, changes in material costs have made it difficult for many contractors to achieve the profit they anticipated when they won the bid. The pricing of construction materials is subject to a complex interplay of global supply chains, economic trends and environmental factors, making it a critical and volatile aspect of project planning. Material costs are subject to myriad external influences, from global economic conditions to local supply chain disruptions. The past few years have taught contractors that materials can become unexpectedly costly or scarce, throwing off even the most meticulous estimates.
Contractors should expect material costs in 2024 to continue fluctuating, with a general trend toward higher prices due to increased demand for construction and potential supply chain uncertainties. These fluctuations can significantly impact the cost estimates for new projects, making it challenging for contractors to submit competitive and accurate bids. As contractors prepare to enter new bids for work, it’s crucial to develop strategies to cope with unstable material prices.
- Market research and analysis — Stay abreast of industry trends and market analyses to anticipate shifts in material costs. Subscribe to construction market intelligence reports and communicate with suppliers to get insights into potential price changes.
- Flexible pricing models — Use flexible pricing models in bids that allow for adjustments in material costs. Include escalation clauses in contracts that specify how price adjustments will be handled if material costs increase beyond a certain point.
- Supplier relationships — Build strong relationships with multiple suppliers to increase negotiating power and ensure access to the best prices. Long-term contracts with suppliers can lock in prices or provide more predictable pricing structures.
- Bulk purchasing and stockpiling — When feasible, purchase materials in bulk or ahead of time to lock in lower prices, especially for materials that are known to be volatile. However, be cautious of the risks associated with overstocking, such as storage costs and potential material waste.
- Hedging strategies — For large projects with long timelines, explore hedging strategies to mitigate the risk of price increases for critical materials.
- Regular review and update — Review and update estimates throughout the project life cycle to reflect any changes in material costs.
Unstable material costs are a significant challenge, but with careful planning, contractors can prepare their project estimations to accommodate these uncertainties. As the market continues to change, staying flexible and informed will be vital to navigating the complexities of material pricing in construction projects.
Indirect Costs
Indirect costs, such as project management, administrative support, equipment rental and utilities, are often harder to pin down but just as crucial to a project’s financial health. These costs can slip through the cracks, leading to budget overruns. It is essential to monitor indirect costs and accurately estimate factors that impact the project cost.
- Conduct a thorough review of past projects to identify recurring indirect expenses.
- Apply a systematic approach to allocate indirect costs proportionally across projects.
- Keep abreast of changes in the cost of equipment and services that could impact overhead.
- Ensure that project managers are trained in financial management and cost control techniques.
Due to inflation and increased interest rates, the cost of doing business has grown. Contractors should consider the economy in general to see how it will impact their business. For example, insurance companies started pulling out of high-risk states, such as California and Florida. Contractors in these states will likely experience increased insurance costs due to fewer available insurers. The cost of doing business will grow. Contractors should be aware of the anticipated cost changes in overhead and plan accordingly.
Accurate cost estimation remains complex, with labor, material and indirect costs presenting their own challenges. However, by leveraging historical insights, embracing technological advancements and fostering strategic relationships, contractors can create sophisticated estimates that reflect the realities of the market. In doing so, they safeguard their anticipated profits and enhance their reputation for reliability and financial acumen. The future of construction may be uncertain, but with strategic cost estimation, contractors can navigate this uncertainty and steer their projects toward success and profitability.