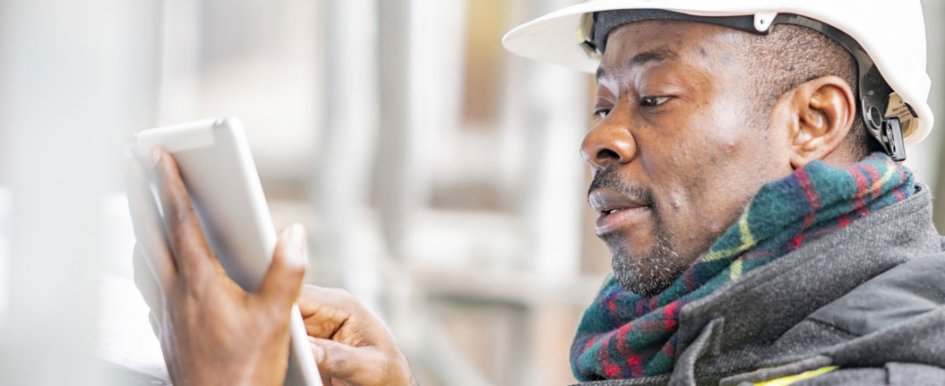
In construction, punch lists are just one element of a comprehensive quality-management program. If you want to reduce defects over time, with the goal of achieving great quality the first time, punch lists alone will not get you there.
When creating a new quality-management program, think about it just as you would any other key component of your business—safety procedures, human resources practices, financial strategy, IT management, etc.—and follow a familiar process that includes setting goals, developing a strategy based on those goals, and executing that strategy and measuring progress.
When you take this approach, quality management becomes part of the culture, and it’s clear that leadership is committed to the program. On the other hand, if you treat your program like a low-priority project, you’ll get results in line with those efforts. Following these seven tips for starting a quality-management program will set your projects up for success.
1. Define Your Goals
Every construction company has different reasons for implementing a quality-management program. These might include mitigating risk and avoiding legal issues; complying with client contracts and insurance requirements; increasing sales by creating competitive advantage; increasing profits by reducing callbacks and waste; improving productivity by eliminating rework; growing the business by implementing scalable systems.
When setting goals, be realistic, but aim high. Many construction company owners buy into the industry misconception that deficiencies are unavoidable. This leads to a certain amount of leniency when it comes to inspections and punch lists. When you commit to achieving the highest quality the first time around and implement the systems that will enable you to eliminate deficiencies over time, all of the goals listed above are achievable.
2. Determine Your Model
As with most business processes, there are many approaches you can take, depending on the goals you have defined, to determining your business model. For example, if your goal is risk mitigation, you might set up your quality department so that the quality manager and their staff do all of the inspections throughout the entirety of the project.
At the other end of the spectrum, if you want to eliminate rework, involve construction managers in quality-management processes, such as jobsite walk-arounds, punch-list management, inspections, trade-partner evaluations and reporting metrics. Based on the goals you have outlined, define the roles and responsibilities for everyone involved in quality-management processes (including quality managers, general managers and trade partners) and communicate them to every member of the team.
3. Commit Resources
Regardless of the model you choose, the teams doing the work must have the necessary resources to do it effectively. If you decide that the quality department is performing all inspections, you may need to bulk up your employee count, making sure there are always enough quality inspectors available for all projects.
If construction managers are to adopt a larger role, they might need resources like ongoing training, software and support staff. When you allocate the resources that support the business model, try not to view quality management as purely a cost center. Remember that the investment you make in quality can yield big returns, especially when your goals are achieved.
4. Hire the Right People
Oftentimes, when creating a new quality-management program, business owners look to one of the best performing superintendents or hire somebody who has expertise in building science. Although these people might have the right skills for identifying deficiencies, they don’t always have the necessary experience for developing and managing business processes and procedures.
Someone who primarily has management skills, with technical skills as a plus, should run a quality program. This might be a project manager or safety program manager who has the expertise to set up and maintain quality-improvement processes and hire qualified inspectors to perform the work.
5. Establish Accountability
It’s important to recognize that a successful program does not depend solely on the quality manager. Every person in the company plays a role in quality management, whether it’s identifying ways to avoid common mistakes, performing inspections or ensuring that the quality team has the necessary resources.
When you build a culture of quality, everyone involved feels accountable for ensuring the work is done right the first time. It’s the difference between employees speaking up when they see a potential problem and keeping their heads down while deciding, “That’s not my job.” Quality is everyone’s responsibility, and it starts at the top—with the leadership team.
6. Define & Report Metrics
Defining and reporting metrics will help you track progress toward reaching your goals. To do this, your metrics and your goals must be in alignment. For example, if your goal is to achieve the highest quality the first time, eliminating rework, a good metric would be the percentage of jobs this is achieved on.
If you want to improve productivity, you might track the amount of time required for rework, which can also be reported in terms of cost savings. Seeing how your metrics change over time can be both informative and motivating. When the team sees that their efforts to reduce deficiencies are resulting in measurable progress, they will continue to implement the processes outlined in the quality program, long after the new wears off.
7. Maintain Engagement
Introducing any type of new initiative takes stamina. It’s not uncommon for companies to launch a quality-management program with a big initial push and high hopes for immediate results. But the reality is that it takes time to roll out new systems, train people on new processes and change mindsets about quality.
Again, think of quality management as a business process and apply the same approach. Create a strategy to introduce new processes incrementally and set milestones that you can work toward over time. Metrics and reporting will help keep employees engaged, especially when you use this information to celebrate successes along the way.
Starting a new quality-management program might feel daunting, but the effort is well worth it. When you approach it as a business process and give it the resources it deserves, a successful program helps you achieve organizational goals that go beyond having shorter punch lists.