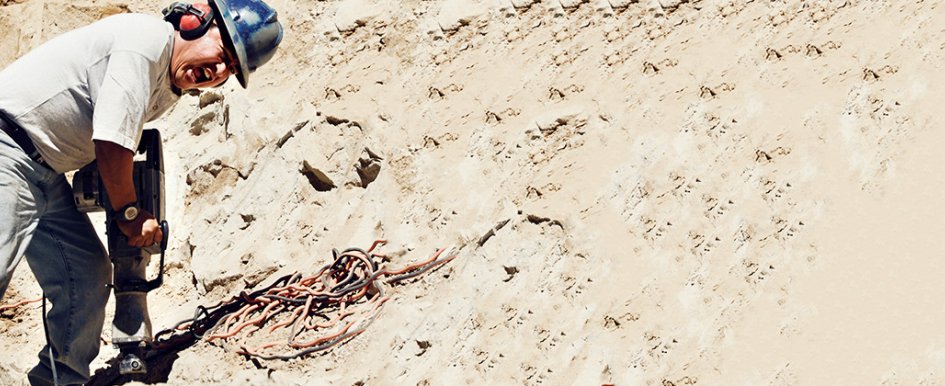
When used effectively, radios are an excellent way to improve safety and productivity on the job when compared to yelling and using hand signals. The jobsite contains countless hazards, and injury prevention is a major concern for all site managers. How many injuries could be prevented if a warning was seen or heard in time? Good construction communications practices can reduce injury and mistakes—saving money and time in the process.
Productivity is improved when construction communication is immediate and does not cause a work delay. Small work delays are everywhere, and they add up to significant losses in productivity. A worker doing something as routine as walking over to his foreman to ask a question is a work delay. Repositioning spotters while a beam is being placed is a work delay. With good communication tools in place, these types of delays are minimized.
The consequences of a breakdown in construction communication can be tragic, resulting in death or serious injury. At the very least, mistakes can happen and work stoppages are inevitable. Jobsites are usually too loud for verbal communication. Hand signals, while often valuable, cannot be relied on to keep the jobsite safe and productive. Radio communications are a great solution to the communication problem, keeping the crew in communication, regardless of their ability to see each other or an opportunity to look up from the work at hand.
Two-way radios are very scalable. It is relatively simple to equip as many users as desired, and a message from a single person is immediately heard by the entire radio group, which is a real advantage for communications from supervisors to construction crews.
However, there are times when even traditional, two-way radios have limitations. When workers need to use both hands, they don’t have a hand to spare to operate the push-to-talk (PTT) button on a typical radio. Additionally, only one person can talk at a time, and that is the person that pushes the PTT first. If someone else has an urgent message like a warning to an equipment operator, their transmission will be blocked, or “stepped on” by anyone else who is speaking. In these instances, wireless intercom systems become extremely valuable. Intercoms offer hands-free communication between team members, which is a huge advantage in hazardous environments where two hands are needed to be effective or to ensure safety. The following are situations when it is appropriate to use two-way radios:
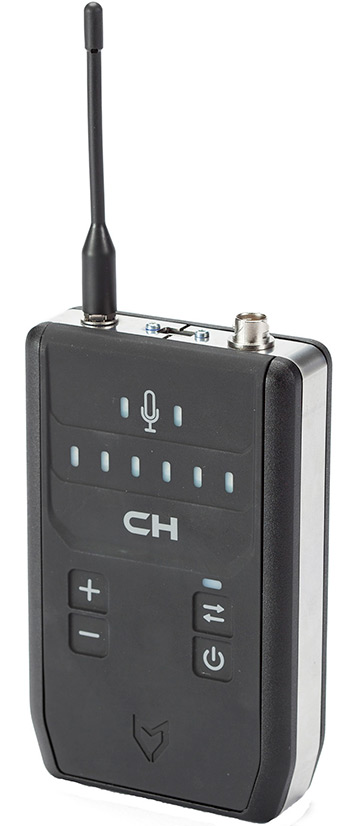
- When there are a large number of listeners with very little back-and-forth communication
- When distances between crews are large, such as over a mile; in these instances, the higher power of a licensed radio system has its advantages. Also, repeater networks can be set up to further increase the range of the system.
On the other hand, the following are situations when it is more appropriate to use wireless intercoms:
- When frequent, simultaneous and conversational communication is desirable or necessary between team members
- When workers cannot see each other
- When hands are busy and it would create a hazard for workers look away from their work or to reach for a PTT button
Some intercoms offer fully conversational, full duplex communication between team members, meaning that anyone can talk at any time. This is an advantage when urgent communication is needed, such as when a crane spotter needs to call “stop” to the movement of the crane. Other intercoms and even some two-way radio systems use a function called voice operated transmission (VOX). VOX is basically like a voice-activated PTT—only one person can speak at a time, but it does keep the hands free for other tasks.
Headsets & Accessories
On a loud construction jobsite, it makes sense to utilize communications accessories like headsets to extract the benefit of using communications devices. If a worker cannot hear a radio message because he already has earplugs in his ears, the advantage of radio communications is lost. Headsets come in multiple styles, ranging from dual-muff designs that clip on to hardhats to lightweight designs that incorporate earplugs for better soundproofing and radio reception. So, what should you consider when choosing an intercom system?
Does the system require a license? The appeal of many intercom systems is that they generally do not require an FCC license. They operate at lower power than most two-way radios and in frequency bands that are set aside for such communication, such as 2.4 GHz or the 902-924 MHz range.
The operating range of the intercom and the ability to penetrate solid objects is perhaps one of the most important obstacles to overcome. Range varies considerably among systems, ranging from a few hundred feet to over three-fourths of a mile. Obviously, range affects the types of projects for which a system can be used.
Base stations are required by most systems. This means that team members must remain in range of the base station in order to maintain communication. The base station can be a fixed device, mounted on the cab of a truck, or it can be mobile and worn by one of the users. Some wireless intercoms do not require a specific base station because the intercoms communicate with each other directly. For many users, this additional flexibility may be desirable.
Separate from a base station, “priority” or supervisory units are another consideration. It can be useful in some environments to have a priority intercom that can override other users. For instance, a foreman may need the ability to break into a conversation with a message at any time.
How many users can be in the intercom network? Also important to consider is how many can speak versus how many employees just listen? It is important to determine how many people on a team need to have constant, direct communication. The number of available users varies with different systems.
Performance in high-noise environments is an important consideration for most intercom users. With multiple mics turned on, noise can become quite a problem, especially on a jobsite that contains heavy machinery. Most high-end, wireless intercom systems use digital signal processing (DSP) to electronically filter out noises. Noise-canceling microphones are another important component of the system.
Battery life is obviously a concern. The battery units need to make it through a full shift without wavering in their reliability. Battery type and size vary among different systems. Some units sacrifice battery life for compact size, while others have robust battery life at the expense of a larger intercom unit. Some systems use interchangeable batteries.
Lastly, consider the ease of setup. Are the units prepared at the factory, or can they be prepared and synchronized together in the field? This can become a big concern if multiple systems are in use in the jobsite area. Some units can be synchronized much like pairing Bluetooth devices—put a unit into synchronizing mode and connect it with other units to form an intercom group. Other systems must be programmed using a computer or by a service center in order to work together. Such systems are frequently sold with specific “listen-only” or “speaking” capabilities enabled.
Finally, costs vary among systems. Robust systems naturally have higher price tags, and often feature greater durability, increased range and battery life, and more compatibility with other communications platforms. A low-power intercom system operating on 2.4 GHz may cost around $600-$700 per user with a range of a few hundred feet or less, while a more sophisticated system in the 900 MHz frequencies operating with longer range of up to 4,000 feet will run around $1,200 per user.
Radio systems can greatly improve safety and productivity on the jobsite. With thoughtful implementation, wireless intercoms offer improvements in communication that will show up as improvements to your bottom line. To choose the right system, it is important to consider the type of work being performed, the communication needs of the users and the environment in which they are working. Finally, do not hesitate to contact communications experts to help make the best decisions for your jobsite communications.