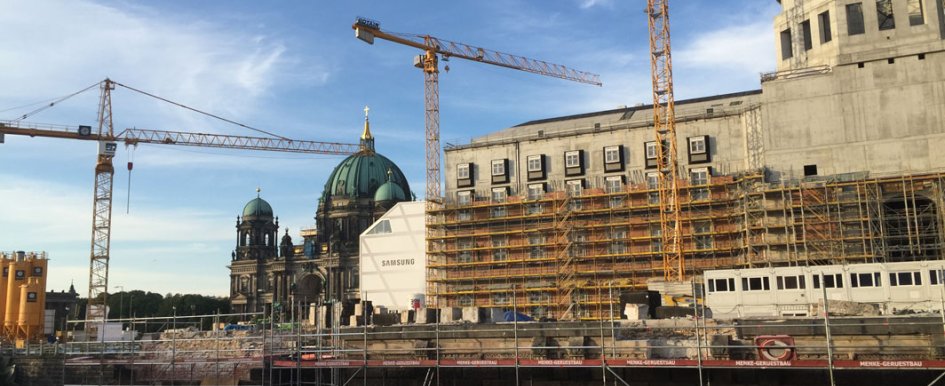
Today’s volatile construction industry, dominated by demanding owners, labor shortages, increasing competition and shrinking profitability, leaves many contractors wondering “How can we survive amidst growing risk and uncertainty?” To combat the instability, contractors must apply an analytical lens to manage their businesses and ensure long-term viability. Successful contractors possess the tools and analytical capabilities necessary to monitor and continuously refine performance, often relying on income statement metrics, such as revenue growth, gross margin or net profit. More advanced companies combine asset, liability or equity metrics from the balance sheet, such as current ratio, accounts receivable turnover, days of cash, return on assets, debt to equity, return on invested capital and debt service coverage ratios.
To extend your company’s analytical capabilities beyond these two financial statements, you should also analyze cash flow metrics, such as cash profitability or free cash flow trending. However, this extensive combination of metrics alone cannot guarantee company success.
Observing One Metric Beyond Cash Flow
Research indicates that nearly 70 percent of companies that go bankrupt are profitable when they close their doors. This startling statistic provokes the question: How can a company fail when it is profitable? While profit and cash flow are critical metrics, viewing them in isolation, exposes companies to risk. In addition to financial analysis, companies must reimagine the way they measure work by paying close attention to the productivity metric throughput. Without adequate attention, throughput is the lethal operational oversight. Refer to the amount of work your company exerts over a specified period as a key indicator of efficiency and performance. The numerator typically consists of some derivative of field-producing revenue like earned revenue per superintendent, project manager or field laborer. The denominator is derived from some variant of time. For example: monthly, weekly or hourly.
Understanding the Throughput Metric
After adjusting accounting by netting out subcontractor revenue and deferring unearned revenue, the calculation for throughput can reveal significant insight. For the data to provide value, employees must understand the implications of such numbers and how to impact the outcome. To demonstrate, consider the scenario represented below.
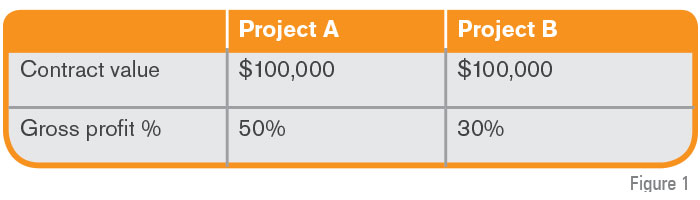
When asked to decide which job the company prefers—assuming equivalent selling, general and administrative (SG&A) expenses—93 percent of survey respondents stated they would elect Project A. Based on the given information, Project A is the logical choice, as it generates the highest gross profit margin. However, this situation omits one piece of information crucial to the decision-making process—time.
Shifting Away From the ‘Pick-Two’ Triangle
There is a common contractor exercise that involves a facilitator drawing a triangle and labeling the sides “quality,” “price” and “speed.” The facilitator then instructs the contractor to pick the two sides most integral to business success. The model is intended to illustrate how contractors are constrained by these resources, forcing them to make a critical trade-off and focus on only two of the three sides. While trade-offs are critical to strategy, what if there is a way to maximize all sides of the triangle? What if competing in today’s economy not only enables, but requires you to emphasize quality, speed and price, not just two of them?
In the competitive construction market, quality is now considered an essential element in all products and services. Companies that sacrifice quality, even temporarily, struggle to compete. The importance of quality is evident in Chipotle’s recent scandal following the outbreak of foodborne illness resulting from undercooked chicken. Chipotle’s brand equity slumped after the release of food poisoning reports. Recouping its image and mitigating future incidents cost the company millions of dollars and valuable time. Crisis management distracted the company’s strategic direction. Meanwhile, Qdoba was innovating its products and pricing model, progressing beyond its fast-casual competitor. Chipotle’s brief lapse in food quality detained its success. Thus, quality is a tactical element companies must get right.
Speed occupies the other side of the triangle. Our increasing demand for haste has accelerated the economy where on-demand, next-day shipping and instant gratification are becoming the norm.
The sluggish construction industry, however, has struggled to keep up. Coltivar has found that over 20 percent of projects take longer to complete than originally scheduled, and productivity in the construction sector has decreased by 0.4 percent over the last thirty years in comparison to a positive 2.2 percent compounded growth in all other industries. Innovative companies recognize the need for speed and are devising methods to achieve momentum despite talent shortages and subcontractor constraints. Prefabrication, 3D printing, equipment innovations and other delivery methods are improving the speed of projects. Still, the industry is not yet approaching full implementation.
The final side of the “pick two” triangle is price. This is where misunderstanding most commonly occurs. The confusion stems from viewing price in nominal terms, rather than as a function of time. When the speed side of the triangle is dissected into a component of time and becomes the denominator of price (e.g., weeks, days, hours), the company can maximize the three sides of the triangle, presenting upside for both the client and the contractor.
Evaluating Projects Based on Throughput
To explore this concept deeper, return to Figure 1. Remember, most people responded that Project A was the favorable choice. However, when additional information on the project is provided, true project value is revealed:
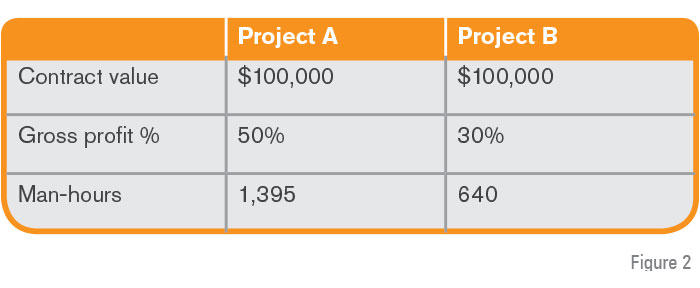
Now which job is more attractive? When applying Figure 2’s throughput information, Project B becomes the better choice. This is true because Project A has a throughput of $71.68 (Contract value/Man-hours) in comparison to Project B at $156.25. To emphasize the implications of this scenario, assume the company’s overhead costs are $125 per man-hour. The company would lose money on Project A while earning a 50 percent gross profit margin.
Contractors frequently stumble when focusing on contract value and gross margin percentages. In fact, the chief executive officer (CEO) of a general contractor (GC) approached Coltivar for guidance as his company struggled with liquidity issues. The company had successfully completed jobs for customers and supported its employees for over twenty years. The GC explained that the management team now was forced to consider its strategic options as it stared bankruptcy in the face. The CEO was perplexed at how nearly every job produced a healthy profit margin, and yet, the company was struggling to stay alive. While the management team analyzed a handful of metrics, they overlooked one of the most telling indicators of company health—throughput. Although the company was earning a decent gross profit percentage on every job, it was not earning adequate margin per day to cover its fixed expenses.
Combining Throughput with Other Key Performance Indicators
One must not lose sight of the big picture when managing the financial side of the business. In fact, the throughput metric is most powerful when used in combination with one or two other key indicators, such as profit margin or capability alignment. The insights from throughput enhance strategic direction, resulting in financial value creation. A mid-sized company incorporated our throughput toolkit into their project pursuit evaluation process and started turning down bad jobs prior to investing in heavy preconstruction resources.
Another contractor was struggling with whether or not to pursue a $350,000 hospitality project. After evaluating the master development schedule and the resources required to complete the project, the team computed a throughput far below the company’s targeted rate. The project pursuit was subsequently declined, and the company, fortunately, bypassed a project with schedule delays and procurement challenges that would have strained its cash flow.
Acknowledging that Resources Are Finite
Although the benefits of measuring and maximizing throughput are clear, some contractors challenge the validity of the metric. They oppose the idea of throughput by arguing that a company should prioritize the amount of earnings, not focusing as much on the timing of the earnings.
Using the example above, they claim Project A earns a gross margin of $50,000 regardless of how long it takes. So, why wouldn’t a company want to pursue that job? The issue is not that the nominal value of the profit erodes over time. Rather, time must be a component because companies only have so many finite resources available to generate returns that cover fixed daily SG&A expenses.
In the construction industry alone, labor is a huge constraint. Research shows that there will be 1.6 million open construction positions by 2022, and there simply aren’t enough workers to fill the demand. This gap will lead to an even bigger labor shortage and impact the contractor’s ability to produce. Beyond the labor hours required to execute the work, companies only have so much equipment and capital assets to dedicate to projects. These limitations force companies to make trade-offs on what they will and will not pursue for work—the very essence of strategy.
When factoring in that companies are constrained by limited resources and the time value of money, the validity of throughput becomes clear. For example, consider a project manager who is offered a $200, 000 salaried position plus benefits with a company. The project manager is thrilled and immediately accepts the position. To her chagrin, she realizes her earnings are spread out over four years, or $50,000 per year.
The job offer is far less appealing when time is a consideration. Without accounting for time or throughput, the project manager falls into the same trap that companies do by resolving that profit is profit regardless of the period over which it is earned.
Adopting Throughput Principles Across the Organization
Throughput is not only valuable for contractors. When companies seek to deliver exceptional experiences to customers, true value is generated for all. Reinventing a company requires strategic discipline to think big, start small and move quickly. Winning contractors invest in building strategies that position their companies to capture premium prices and manage costs more effectively; develop capabilities to deliver exceptional customer experiences; and eliminate blockages to optimize throughput.
The benefits of such efforts are clear—increased revenue, higher engagement, heightened innovation and improved customer loyalty—to name a few. So, how can contractors start incorporating throughput principles in their strategies and operations?
- Build and maintain a minimum twelve-month rolling projection to forecast costs and profit margins.
- Monitor performance through trailing twelve-month indicators.
- Make necessary accounting adjustments to compute a true throughput measure that is relevant to frontline employees.
- Empower estimators and preconstruction teams with a clear throughput goal for project pursuits.
- Communicate throughput goals to the front line. Continuously eliminate points of congestion along the critical path and provide timely updates.
- Collaborate with owners and customers on ways to increase throughput during the decision, preconstruction, construction and closeout phases of the project.
- Create a strategic blueprint for technology investments to enhance critical activities, increasing throughput and improving overall customer experience.