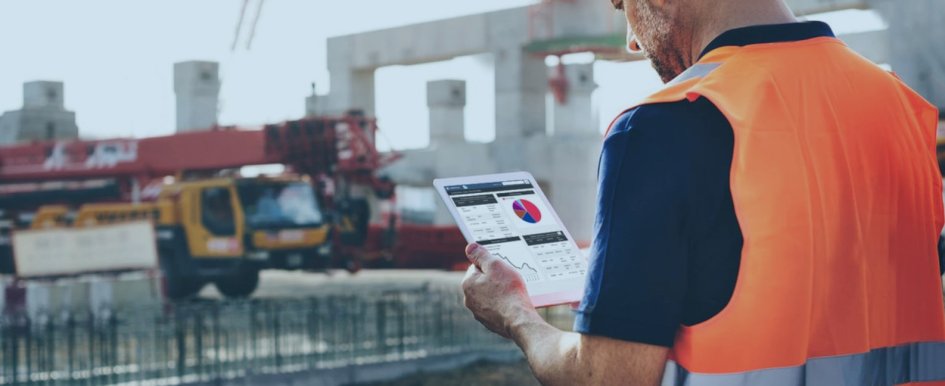
Several years ago, digitization became the battle cry for construction companies that wanted to be on the frontier of the construction technology wave. That was a good start. But now it's time to look deeper.
More than Just Documents
Construction is more than documents, it's processes. Yet, contractors are buying in to document-management-focused software systems for key operations such as safety and quality. And, while the benefits of accessibility to data, paperless jobsites, and mobility are a good step up from paper, they're still holding back the operators on-site from doing their jobs as well as they could.
Why? Because document-management-based systems follow the form (like a permit), and not the process the form must take in the field. When this happens, you have a digital replica of a form, where a user fills out the details, but it gets filed in a digital silo, not allowing it to integrate with other key functions, as they often must do in the field.
Process-based software systems follow the how and the why of the information and data that goes into the form. It takes the document out of the equation, and takes the key data inputs into a live stream where it can sync, integrate and interact in real time with key processes being performed in the field.
When you ask yourself, "How does this process work in the field?," you quickly see that digitizing documents reduces paperweight, but still impedes operational efficiencies. Because forms and documents are inherently siloed, while data, when pulled from documents, can be seamlessly woven into other functions.
Are You Still with Me?
How many times have you opened your document management app to fill in information for your permits, only to have to open another app to get the names of the workers who are performing those tasks (Are they certified and signed off on the job hazard analyses (JHAs)? Then you have to walk over to a permit board in the shed or trailer to understand the permits currently scheduled, permit type, location, date, start time, finish time and description. Then you have to open an inspections app to complete monitoring checks and capture key information throughout the permit life cycle.
Process-based software systems follow the how and the why of the information and data that goes into the form.
How Process-Based Software Handles Tasks
Continuing on with the example of permits, let's follow the permit processes and how software that understands your field needs, tackles your issues.
- Subcontractors need to submit permits for review by either the general contractors (GC) or the facility manager.—Process-based systems provide a portal for subcontractors on a project to submit permits, view revision history, receive notifications of acceptance or rejection, and have the ability to check in or out of the permit. Additionally, HammerTech:
- Provides a dashboard specifically for permit management where reviewers can easily view outstanding permits awaiting review and track existing permits
- Sends an SMS notification to permit reviewers when a permit comes within one hour of its proposed request start time and the permit hasn't been reviewed
- System provides cut-off times for submissions restricting overnight requests for morning permits
- Provides the ability to track all of this information via business intelligence (BI) tools through reporting APIs
- You need to determine the identity and capabilities of the workers who are performing the tasks stated in the permit.—Forms require you to enter in the names of the workers performing the tasks for each permit. That requires double, triple, quadruple data entry. No, thank you.
With process-based systems, worker information is already gathered in the system during enrollment and orientation, and certifications are also tracked. So, eligible workers can simply be selected from a list. This allows the reviewers to also know which JHAs have been assigned to workers and the company undertaking the permit so this can be quickly selected from the accepted list of JHAs on-site.
- You need to see permit locations or permit zones, usually found on-site in a trailer or shed.—Say goodbye to the extra foot traffic. While point solutions allow you to enter the location or permit zone, you usually still need to find a physical map of the booked zones. Not with a process-based system. With systems configured based on the process, you can configure zones by permit type (you can have different zones for hot work permit versus a confined-space permit, versus an elevator work permit). You can upload one or more site maps and draw the permit zones on the map in their physical location, provide a title for the zone and even assign it a color. These are then shown to the user as a digital map on their mobile phone or tablet that they can select from when applying for a permit, all making a cumbersome processes a bit easier.
- You need to create and manage exclusion zones to keep people safe.—This is a big one. Right now, exclusion zones are generally managed manually using keys or tags for check-in and check-out: a process that is prone to error and inherent risks.
Within process-based systems, the GC or facility management team can configure the permit zones as exclusive or not, and configure a digital check-in/check-out process. For example, once a permit is approved, work cannot begin until a worker "starts" the permit, fills in any required or requested information (users can use a checklist or take photos for proof of "all clear") and then sign off on the process so it can become an audit record.
The "finish" process is similar, requiring info to be filled out and signed off. As the user(s) checks in and out, the permit updates status from "scheduled" to "in process" to "finalized." Workers will also receive a SMS reminder within a zone if they have not checked out by the end of the stipulated time on the approved permit.
In addition, users have a calendar view for any exclusive permit/zone combination showing days and times that are completely booked or partly booked to help with managing permit requests, also helping to reduce or avoid clashes.
- You need to monitor and conduct checks throughout the permit life cycle.—Document-based systems will generally provide tables with space for a worker or user to complete monitoring checks and capture key information throughout the permit life cycle. But the data captured and the ease of capturing can be frustrating because the information lives within different apps or forms.
Process-based systems integrate "inspections" with "permit management" to allow an inspection to be configured based on the monitoring requirements. From there, it becomes a one click process for workers or users to undertake an associated inspection on the permit and capture key data. You could even use a QR code that can be filled in and left around the permit entry zone for ease of accessibility and use.
In the End
When searching for systems to alleviate problem areas in your daily operations, safety and quality, it's important to search for software that understands the entire scope of the process you use, and creates solutions that ensure more efficiency throughout that process. Simply digitizing forms and centralizing them within a mobile application isn't enough anymore.
Technology needs to help you do more. While the first step toward embracing new technology was crucial, it's more imperative now (as the industry expands looking for ways to close gaps, reduce risks and increase performance and productivity) that construction companies begin looking deeper into their technology solutions and determine if their software needs require more thorough solutions to ensure operational efficiencies.