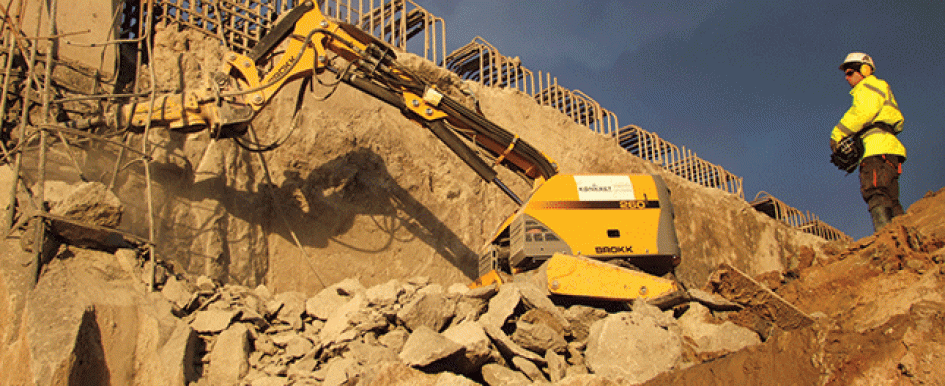
Shards of concrete, high working heights, falling rubble and piles of metal rebar are often definitive features of construction jobsites, making them a hotbed for injuries. Personal protective equipment such as hard hats, boots and safety glasses can help prevent some injuries, but as long as operators are in the line of fire, the threat is there.
Amidst the debris, another threat lurks. It’s less obvious, but no less debilitating—prolonged and repetitive use of handheld equipment. Personal protective equipment can’t completely fend off the injuries these machines and tools can cause to arms, backs, hands, shoulders and wrists.
Handheld equipment—such as rivet busters, breakers or chipping guns—has a place on nearly every construction and demolition jobsite. While advancements have been made to improve the comfort and safety of these tools and machines, many models still produce heavy vibrations that are transferred directly to the operator. Prolonged use can lead to carpal tunnel syndrome, nerve damage and hand-arm vibration syndrome, which make completing
simple tasks such as writing or gripping a steering wheel challenging.
Fortunately, another option attacks the problem of jobsite injuries from several entirely different angles: remote-controlled demolition robots. They are hard-hitting, powerful and versatile
machines that take safety and productivity to a whole new level—and they’ve been doing it for more than 30 years.
Designed for Duty
The first commercially built remote-controlled demolition machine made its debut in 1981. It was designed by a Swedish contractor who had been awarded a job to clean a furnace in a lead smelting plant. The work required his crew to endure above-normal temperatures and use jackhammers at awkward angles. It was a recipe for fatigue, potential burns and hand, arm and back injuries. The contractor devised a solution for working smarter, not harder
—a piece of equipment that could do the same work, while the operator ran the machine from a safe distance. During the next few decades, as the arsenal of remote-controlled demolition machines grew, so did their use in a variety of applications outside of smelting plants.
Today’s remote-controlled demolition machines have a three-arm system that, on some models, can rotate 360 degrees. This allows operators to perform a range of tasks at nearly any angle without fatiguing or straining muscles.
Operators can equip them with attachments, including breakers, buckets, grapples, scabblers and shears to demolish, crush, cut, sort and move material, all while remaining a safe distance from the work. This substantially reduces the risk of injuries or death from hazards such as falling debris.
Remote-controlled demolition machines can be as short as 3 feet and as narrow as 2 feet, so they can maneuver through doorways, into elevators and throughout confined spaces. Some models can even climb stairs. Larger units can be as tall as 8.5 feet and as wide as 7 feet with greater hitting power.
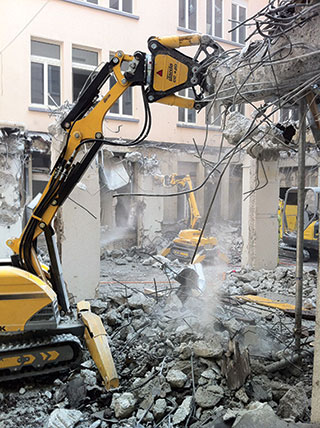
Changing the Battleground
For example, demolishing a building in an urban area can be challenging. Imploding or using a wrecking ball comes with the risk of injuries to bystanders and workers and damage to nearby structures. Instead, contractors can use a remote-controlled demolition machine and a top-down approach. They can equip the machine with a breaker or crusher, mount it to a hoist and break up the roof while pushing demolished material into the building. This virtually eliminates the risk of injuries from falling debris and damage to adjacent buildings. This situation also is less of a nuisance to occupants of surrounding buildings because they don’t need to evacuate. A top-down approach may be one of the only options on projects where structures are located near hazardous materials such as combustible fuel tanks.
Demolition work inside buildings and confined spaces also can be dangerous. Workers can get hurt if ceilings, floors or stairs collapse as they are being demolished or when equipment exceeds low floor load requirements. Aged sewer and water tunnels also can collapse when crews demolish liners. Compact, remote-controlled demolition machines can access this kind of work while remaining outside the immediate work zone. Even something as simple as removing a concrete staircase can be accomplished quickly and safely with a demolition machine.
Projects inside or near hospitals can pose unique challenges as well. Dust can be hazardous, noise can be disruptive to patients, and vibrations can cause problems during nearby surgeries. Work adjacent to museums also must be handled carefully, because vibrations from demolition work can damage precious artifacts. A more stealthy approach is to use a remote-controlled demolition machine equipped with a crusher attachment to quietly pulverize material, producing minimal dust, noise and vibrations.
Finally, many jobsites possess mounds of both concrete and metal, including angle irons, I-beams and rebar. Most often, a torch is the tool of choice for cutting these materials, but this method presents risks ranging from hazardous smoke to potential burns.
Contractors can instead use a remote-controlled demolition machine with a metal shear attachment to safely cut through metal and rebar without the risk of injuries.
While safety is the most notable benefit of remote-controlled demolition machines, they are also fast. These machines can do the work of as many as three operators with handheld equipment in the same amount of time, allowing contractors to bid on jobs with tighter deadlines.
Because remote-controlled demolition machines can be used with a variety of attachments in a diverse range of applications, contractors also can expand their businesses into new markets and bid on more types of jobs that they simply didn’t have the ability to take on before.
Armed and Ready
Safety is one of the most critical issues on every construction or demolition mission. Getting everyone home safe at the end of each day often requires reinforcements beyond standard protective gear. Especially when jobs become tricky or more dangerous, remote-controlled demolition machines can be the ultimate individual, crew and company protective equipment.