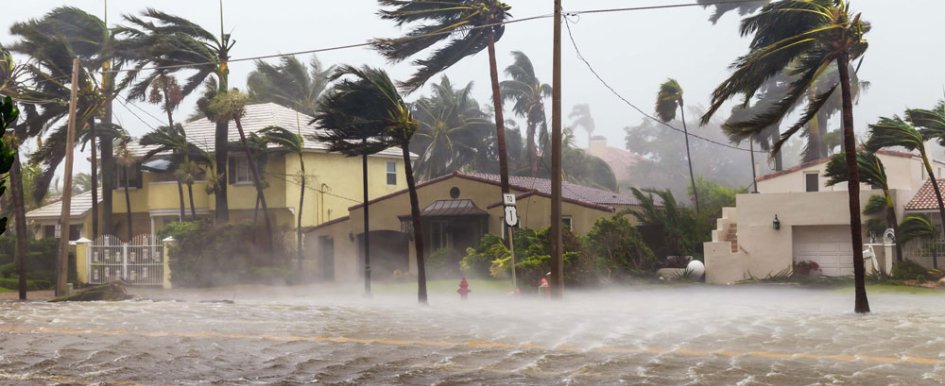
Summer is in full swing, and, for some parts of the country, that means hurricane season is too. If there is anything to be learned from the damage wrought by last year’s Hurricanes Harvey, Maria and Irma, it’s that having a thorough action plan is paramount. And who better to talk to than Senior Superintendent Tim Ham, who manages field-related aspects of Hoar Construction’s various commercial projects in Central Florida. Ham has been an employee at Hoar for 26 years, and helped start the Florida division 20 years ago. He spends the majority of the day planning ahead so that boots on the ground can work efficiently and effectively on the jobsite. This includes ensuring his teams are ready for any potential issue or obstacle that comes their way, including hurricanes. Read his advice on prepping for storm season below.
CBO: What is Hoar’s preparation process for hurricane season?
TH: We have a pretty extensive tropical storm and hurricane plan. One of the first things we do when we start a project is put together a severe weather plan, specific to the project we are working on at the time. Preplanning is extremely important when these storms are coming. We lay out detailed actions that we will take at 72, 48, 24 and 12 hours prior to the storm making landfall, and we start that process as soon as the storm is named. Just a few weeks ago, with the first tropical storm of the year, we went through this process, which begins with getting all of the project partners and jobsite leadership from our team around a table and talking about the volume of work we have going on and the number of areas we need to modify in preparation for the storm. The goal is to determine the amount of work that needs to be done to prepare the entire team and the jobsite for the impending storm. Then, we go to the subcontractors/trade partners who are not from the area, or are from an area that does not get much tropical weather, and work with them to ensure they are also prepared. Water is obviously one of the biggest issues that comes with hurricane preparation. We look at our stormwater management systems to understand what state they are in and what we may have to do to get them in a better position. Of course, we always aim to prevent any building or structure flooding. We are always modifying roadways and water-retention systems, so it’s essential to pay attention to what condition they are in, which indicates how they will hold up in severe weather. Next, we start watching all of the Federal Emergency Management Agency (FEMA) storm advisories. We encourage our team and our trade partners to follow the same source so that everyone is on the same page regarding weather updates. Seventy-two hours before the storm’s estimated landfall, we call another meeting for general readiness, and we let the project owner know about all of the preparation that we are doing. We take photos and video of the jobsite in its current state; get the normal hurricane-prep items, such as generators, water pumps, tarps, etc.; make sure we have anything we may need after the storm to get the project back on schedule; and bring in fuel tanks to fuel any equipment in the case of a fuel shortage. At the 72-hour-mark meeting, we name supervisors and leadership that will be on the emergency list. All of these team members are included on a group email moving forward with project and storm updates. At 48 hours until landfall, we start taking action in preparing the jobsite for a storm. We secure all the objects that could become airborne. All materials, including scaffolding, wall systems and other supplies are secured so they are not exposed to high winds. If we are far enough along in the project process to have roofing materials on-site, we make sure those are secured as well. By the 24-hour mark, we have decided who will be staying local and have given the rest of the jobsite crew instructions for evacuation. The team allocated to remain local knows their safe location to ride out the storm. We stop all deliveries coming to the site and make sure no one is en route to the project. We alert all of our vendors and suppliers about the situation and have the dumpsters on-site emptied, which is extremely important because it controls the amount of debris flying around the jobsite during the storm, and you will need empty dumpsters for cleanup following the storm. Then, we remove all the signage from roadways. Next, we walk the jobsite and make sure everything is in ready condition, designating a huddle point for the first meeting following the storm so that first responders know where to come. All of the equipment on-site is secured, and the team members staying local are given the codes and keys to the equipment that will be on the jobsite. This way, everything is accessible when necessary. In the days following the storm, a recovery plan is put into action. One of the first things we do is assess the damage as a team. Then, we make sure the jobsite is safe, and first responders are filled in on what they need to know upon returning to the jobsite. We look for excessive damage and for areas that could potentially be flooded. The water damage after the storm is often the biggest obstacle to overcome. Keeping a short-term schedule of how repairs will happen and when they will take place is helpful.
CBO: What planning issues or errors do you often see regarding preparation for storm seasons?
TH: Many trade partners we work with are not familiar with what it takes to get through a hurricane with as little damage possible. That’s where I have seen the biggest issues. It’s hard to express to some of those people how important preparation can be. In Florida, there are a couple of main roads out of the state. When a storm is coming and mass evacuation is happening, it can cause more trouble to try to move materials elsewhere, which usually involves getting stuck somewhere with no opportunity to secure those materials. A lot of companies will try to get their equipment and materials to a more northerly place and end up in trouble. Once a contract is executed with a trade partner, we make it a point to specifically review parts of the contract that mention crisis plans. When we have our pre-project conference with the trade partner, we spend time discussing those plans. Then, we discuss this in even more detail as the project progresses.
CBO: What should businesses include in a written hurricane preparation plan?
TH: Make a plan for water management system processes. Too many companies forget about this aspect. For example, we do a lot of projects that have swimming pools on-site. Those pools have to be drained at least a quarter of the way down. We have seen retention ponds fill up to the point that they breach the earth and dams. Understand your elevation above sea level because high tides and storm surges affect flooding as well.
5 Tips for Hurricane Preparedness
- Make a plan before you need it. Start the discussion early, including the parameters and what you will need to prepare.
- Call a formal meeting as soon as the storm is named. Include your jobsite team and representatives of your trade partners/subcontractors.
- Pay careful attention to your water management systems. Determine how water will drain from the jobsite in its current condition.
- Designate one source of news to follow and share this with your trade partners. Wind speeds can give insight into the damage you can expect.
- Secure everything. Keep materials and supplies for structure protection on hand.